Produkcja innowacyjnych zbiorników z tworzyw termoplastycznych metodą nawojową – co przemysł na niej zyska?
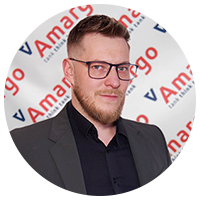
Grzegorz Zając, Ekspert z zakresu zbiorników i instalacji przemysłowych z tworzyw sztucznych
Inwestycja Amargo w linię technologiczną do produkcji beznaprężeniowych rur oraz cylindrów zbiorników z tworzywa termoplastycznego metodą nawojową pozwala na realizację projektów, w których ze względu na warunki procesów przemysłowych zastosowanie tradycyjnie zgrzewanych zbiorników bywa utrudnione. Dodatkowo umożliwia budowę zbiorników, wykonanie urządzeń czy aparatów wedle koncepcji inwestora w ramach samodzielnej niezależnej realizacji – przy wykorzystaniu półproduktu w postaci zakupionego cylindra / rury.
W publikacji przedstawiamy specyfikę technologii nawojowej, wskazujemy na cechy świadczące o jej innowacyjności oraz omawiamy korzyści w zakresie bezpieczeństwa, ekonomii i ekologii, jakie niesie projektantom, inwestorom i użytkownikom zbiorników.
Linia nawojowa produkcji beznaprężeniowej z termoplastów
Linia produkcyjna do wytwarzania cylindrów zbiorników i rur technologią ekstruzji uplastycznionej wstęgi tworzywa i nawijania umożliwia uzyskanie średnic rzędu 1000÷4000 mm i długości aż do 7 m w jednym cyklu. W przypadku zbiorników jest to tzw. technologia AmargTank SafeSeamLess®, MultiLayer® oraz MultiLayer DoubleWall®.
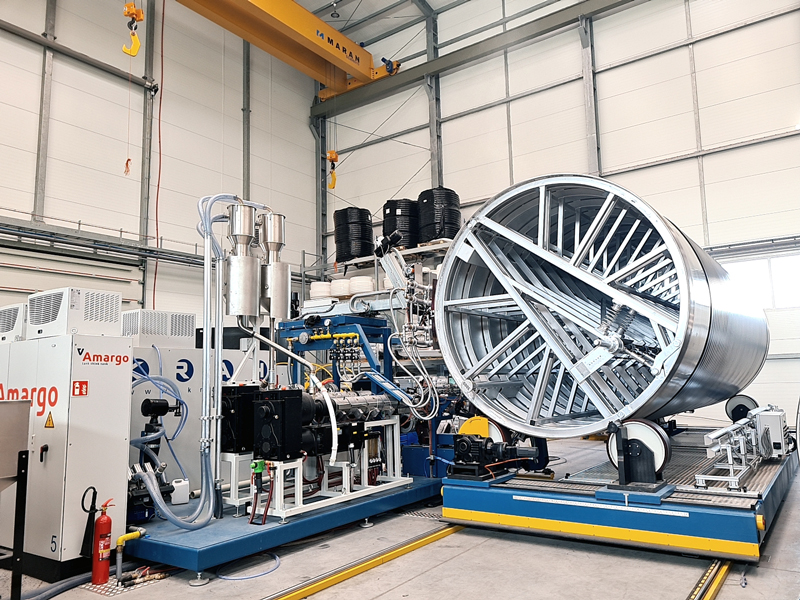
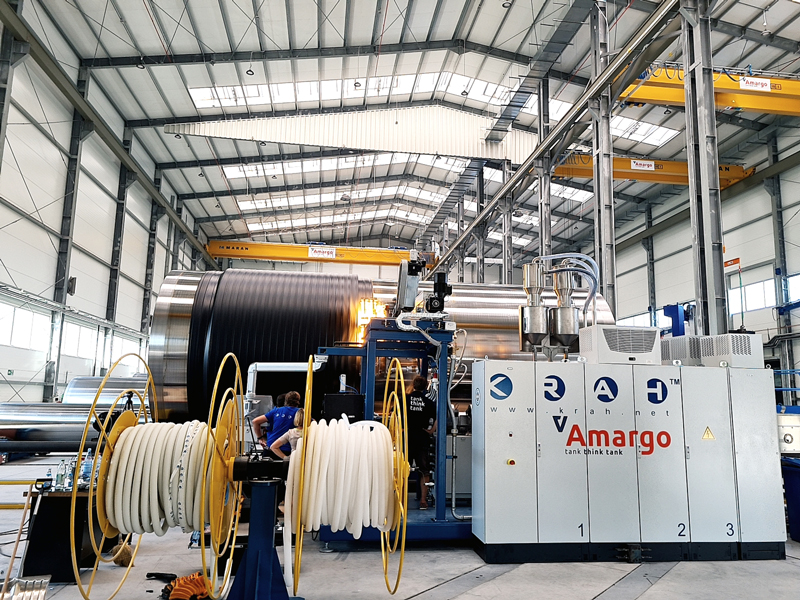
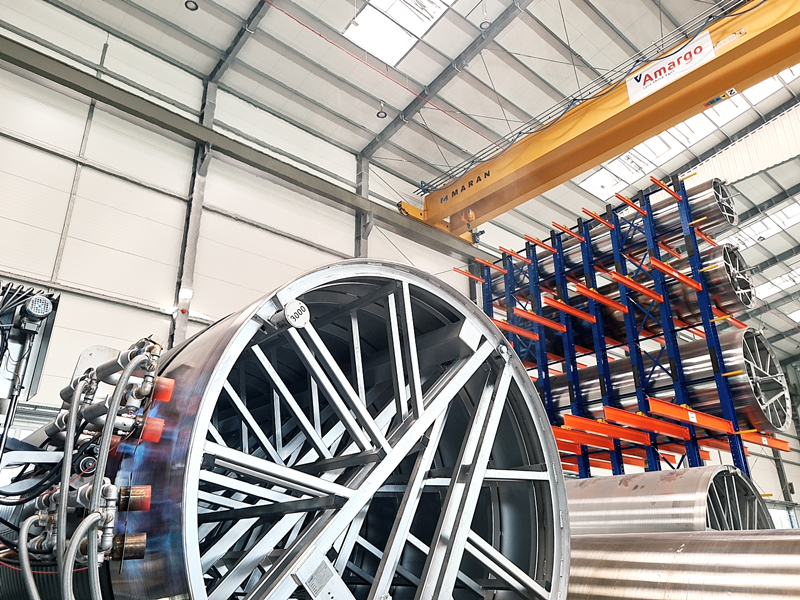
Prace nad wdrożeniem technologii rozpoczęły się w 2019 roku i były pokłosiem nieustającego postępu technologicznego, konkurencyjności na rynku zbiorników, jak również restrykcyjnych zapisów prawnych w zakresie ochrony środowiska, które zobowiązują do ulepszania dotychczasowych rozwiązań. Wszystko po to, by w pełni bezpiecznie magazynować substancje agresywne o wysokiej reaktywności, zapewniając bezpieczeństwo personelowi i dbając o mienie przedsiębiorstw produkcyjnych.
Do pewnego czasu w Amargo zbiorniki chemoodporne produkowane były wyłącznie na poprzez zgrzewanie i spawanie gotowych płyt tworzywa (tzw. zbiorniki AmargTank ClassicWeld®). Wdrożenie technologii nawojowej otworzyło drzwi do większego spektrum zastosowań. Zanim opowiemy o możliwościach i aspektach technicznych wpływających na kwestie nie tylko bezpieczeństwa, ale także te ekonomiczne i ekologiczne, wskażemy na czym polega zasadnicza różnica obu tych technologii.
Czym różnią się technologie produkcji zbiorników: tradycyjna i nawojowa?
W dużym skrócie technologia produkcji zbiorników AmargTank ClassicWeld® z wykorzystaniem półproduktów – czyli wspomnianych płaskich płyt ekstrudowanego tworzywa oraz drutu spawalniczego w formie zwojów – opiera się na wykorzystaniu gotowych arkuszy o stałych wymiarach handlowych np. 2000 x 1000 mm, 3000 x 1500 mm, 4000 x 2000 mm oraz stałych grubościach. Poszczególne arkusze tniemy, a następnie zgrzewamy oraz spawamy ekstruzyjnie lub gorącym powietrzem.
Z kolei wdrożona przez nas jakiś czas temu technologia nawojowa opiera się o system ekstrudowanych ścianek i profili nakładanych w jednoczesnym procesie wraz z podgrzewaniem stalowego obrotowego rdzenia prowadzącego (swego rodzaju formy usuwanej po ostygnięciu i przy zmianie średnicy). W kolejnym etapie następuje dalsza obróbka znana z sektora termoplastów. W efekcie powstaje bezspoinowa, uformowana na dany kształt i wymiar rura – czyli nasza część cylindryczna zbiornika – pobocznica, z wyeliminowaniem większości barier i ograniczeń związanych z wytwarzaniem zbiorników z prefabrykowanych płyt tworzywa. Sama produkcja dzięki nowej linii odbywa się zgodnie z normą europejską DIN 16 961 i zależnie od formy zakończenia odcinków rur do dostaw dołączane są certyfikaty jakości, w tym według normy EN 10 204-2.2.
Dla odróżnienia od standardowej technologii nazewnictwo zbiorników produkowanych metodą nawojową jest następujące:
- zbiorniki AmargTank SafeSeamLess®, czyli wykonane nawojowo jako lita pełna ścianka – bez naprężeń,
- zbiorniki wykonane nawojowo jako ścianka lita wewnątrz + wzmocnienie profilem okrągłym:
- AmargTank MultiLayer® – profilowanie, bez zewnętrznej powłoki,
- AmargTank MultiLayer DoubleWall® – profilowanie + warstwa zewnętrzna.
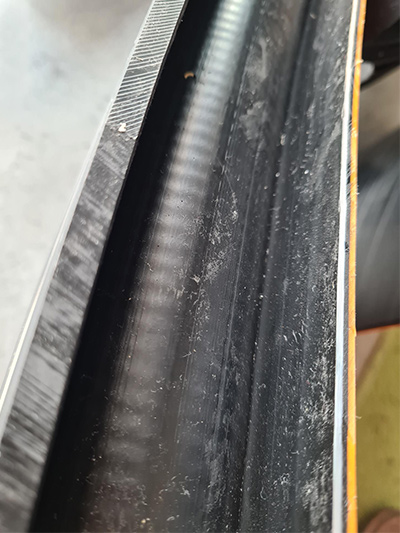
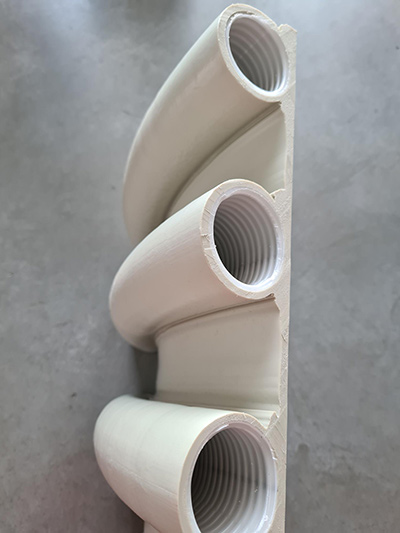
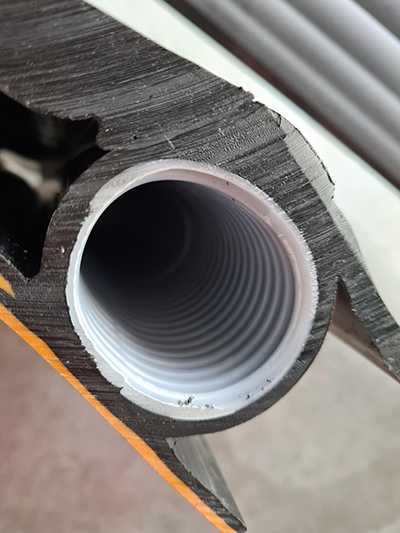
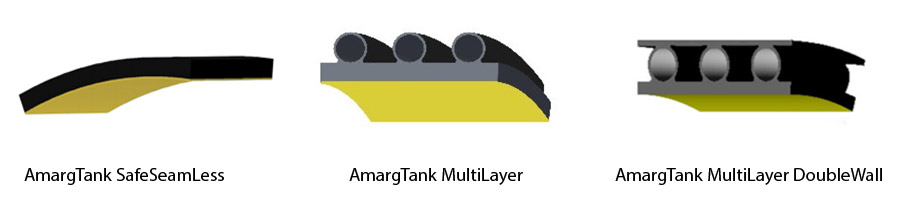
W tym miejscu chcemy podkreślić, że nie jest to standardowa technologia nawojowa, którą stosują głównie producenci rur kanalizacyjnych dużych średnic, gdzie możliwe jest uzyskanie jednego profilu. Ścianka wewnętrzna takiego profilu jest zbyt cienka do zastosowań przemysłowych i nie jest odporna na związki będące silnymi utleniaczami, a dodatkowo jest narażona na pełzanie tworzywa czy częściową migrację medium w termoplast. Takie rozwiązanie nie pozwala na dopuszczenie produktu do zaawansowanych aplikacji, w tym wykonywania zbiorników magazynowych, które podlegają pod dozór techniczny UDT.
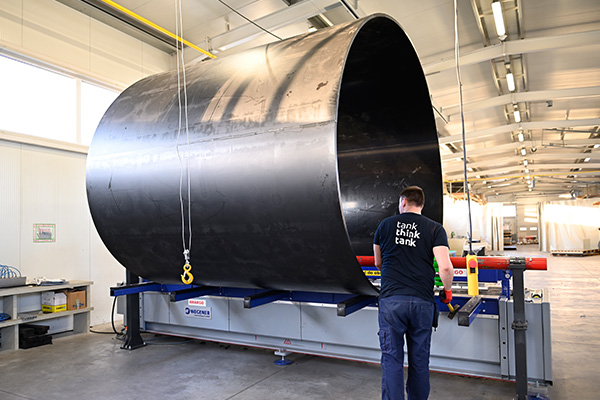
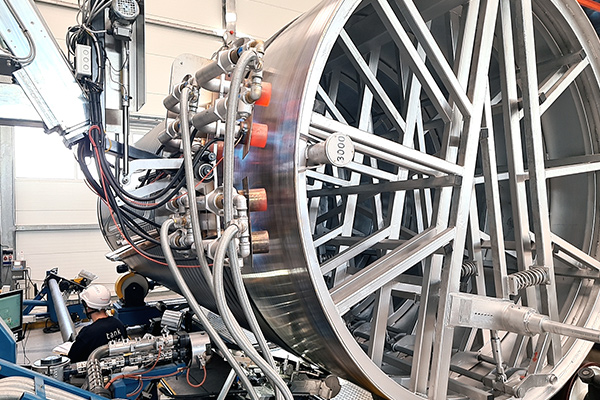
Wybór technologii produkcji zbiornika przemysłowego w kontekście parametrów medium, pojemności i gabarytów konstrukcji
Porównując obie technologie, w pierwszym przypadku wymiar zbiornika jest ograniczony formatem arkuszy oraz obróbką mechaniczną i spawaniem czy zgrzewaniem. To umożliwia wykonanie cylindrów do wysokości jedynie 4 m (inne opcje to połączenia mufowe, fazowanie krawędzi, centrowanie czy spawy potrójne, które są obarczone błędem, czasochłonne i kosztowne w wykonaniu oraz skupiające miejscowe naprężenia). Poza wysokością zbiornika dochodzą znaczne ograniczenia co do średnicy, wynikające z braku możliwości zwijania płaskich arkuszy tworzywa i uwarunkowania normowe z uwagi na fakt nieprzekraczania dopuszczalnych naprężeń wewnątrzmateriałowych.
W odróżnieniu od zbiorników wytwarzanych w sposób tradycyjny posiadających zamknięty zakres wymiarowy technologia nawojowa pozwala uzyskać duże pojemności. Dla porównania średnica zbiornika może wynieść ok. 4–4,5 metra, a długość cylindra 5–7 metrów (zależnie od długości walca, tzw. mandrela), z możliwością podwójnego wydłużenia za pomocą spawu wykonywanego przez robot znajdujący się na stanowisku obok linii. Poza samą linią zakład dysponuje także zespołem czterech suwnic w obu nawach hali o wysokości 19 metrów, co umożliwia produkcję zbiorników o łącznej wysokości czy długości rzędu 10–3 metrów.
Przy produkcji z płyt, nawet przy wykorzystaniu zgrzewarki liniowej o długości 4000 mm i największych dostępnych handlowo arkuszy tj. 4000 x 2000 mm, konieczne jest wykonanie dodatkowych połączeń spawanych, co z kolei wymusza inny schemat obliczeń, uwzględnienie współczynników spoin w cylindrze oraz oczywiście czas potrzebny na obustronne zespawanie ekstruderem przykładowo obu cylindrów.
Oczywiście poza samymi możliwościami gabarytowymi zbiorników różnic między obiema technologiami jest znacznie więcej.
Kiedy produkcja zbiornika z arkuszy tworzywa jest niemożliwa – wpływ rodzaju czynnika roboczego, temperatury pracy i zapisów DVS
Zanim wskażemy konkretny przykład chcielibyśmy wspomnieć, że w wielu procesach technologicznych wykorzystuje się substancje o znacznym stężeniu i gęstości oraz wysokiej temperaturze pracy. Gdy dojdą do tego ograniczenia przestrzeni to przy doborze zbiornika okazuje się, że sama geometria nie pozwoli zachować jego odpowiedniej pojemności.
Z powodu sztywności, wysokiej wartości modułu elastyczności poszczególnych rodzajów tworzyw dąży się do ograniczania powstawania szkodliwych naprężeń wewnątrzmateriałowych w wyniku zwijania arkuszy. Wskazania i wytyczne w zakresie możliwości wykonania cylindrów z płyt płaskich zawarte są w opracowaniu DVS (tab. 1).
Tab. 1. Zależność między grubością ścianek zbiornika a minimalną średnicą cylindra (mm) według DVS.
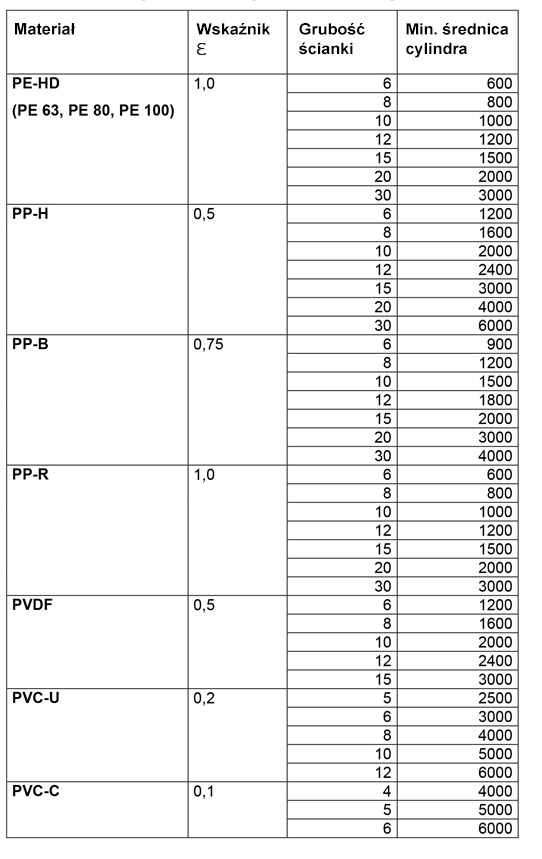
Uwzględniając powyższe wytyczne, w skrajnych przypadkach dopuszczalna grubość zbiornika może wynieść maksymalnie jedynie 5–6 mm, co niestety jest niewystarczające do przeniesienia obciążeń. Chcąc zwiększyć grubość należałoby wykonywać skomplikowany, czasochłonny i drogi proces temprowania lub relaksacji tworzywa (podgrzewanie płyt materiału w całej objętości i przekroju przed rozpoczęciem procesu zwijania lub tzw. odprężanie materiału), a co za tym idzie – byłoby nieracjonalne kosztowo. Natomiast stosując nowoczesną technologię beznaprężeniowej ekstruzji wstęgi tworzywa – od razu na dany kształt – możemy wykonać analogiczny zbiornik z grubością ścianki litej nawet rzędu 100 mm.
W jednym z przedsiębiorstw chemicznych ze względu na parametry pracy zbiornika procesowego tj. mieszaninę, w której znaczną ilość stanowił kwas fosforowy o stężeniu do 45% oraz temperaturze roboczej 80 st. C (krótkotrwałej 85 st. C), na bazie obliczeń otrzymaliśmy minimalną grubość ścianki wynoszącą 40 mm. To z kolei, po uwzględnieniu dopuszczalnego wskaźnika wydłużenia struktur krawędziowych ɛ, który dla tworzywa polipropylenu homopolimeru typ PP-H (np. oznaczenie handlowe Simona PP-DWU AlphaPlus) wedle normy DVS wynosi 0,5, dało nam informację o możliwości wykonania cylindra o średnicy minimum aż 8000 mm. Dopiero taka wielkość pozwoliłaby uniknąć przekroczenia maksymalnych dopuszczalnych sił i naprężeń wewnątrzmateriałowych. Projekt naszego Klienta zakładał natomiast kilkukrotnie mniejszą średnicę.
Możliwości techniczne maszyny zgrzewającej oraz zwijającej w cylinder dawały możliwość pokonania sił oporu i zwinięcia płyt o grubości nawet 30–50 mm, ale w przekroju ścianki powstałyby nadmierne naprężenia. W związku z tym wykonanie takiego zbiornika z gotowych płyt tworzywa nie byłoby możliwe ze względu na naprężenia, które mogą pojawić się w płycie i w dalszym okresie eksploatacji mogłyby skutkować propagacją pęknięć do kolejnych warstw materiału, całkowitym uszkodzeniem ścianek zbiornika, nieszczelnością i trwałą awarią.
Receptą na to było zastosowanie cylindra wykonanego metodą beznaprężeniowej ekstruzji wstęgi termoplastycznego tworzywa, czyli systemem nawojowym. Rura nawojowa jest materiałem, w którym stres w tworzywie jest mniejszy i bezpiecznie możemy dokładać milimetrów na grubości ścianki. Daje to większą swobodę projektowania, wykraczającą poza ograniczenia wynikające z DVS.
Dzięki ekstruzji na gorąco połączonej z jednoczesnym formowaniem kształtu unikamy pojawienia się naprężeń wewnątrzmateriałowych, co pozwala na wykonanie zbiorników o nawet małej średnicy, ale z dużą grubością ścianki litej (np. zbiornik o średnicy 1800 mm i grubości ścianki rzędu 30–50 mm). W praktyce możliwa staje się realizacja zbiorników na większą grupę środków chemicznych i pracujących w wysokich temperaturach (zależą one od rodzaju tworzywa, średnio jest to 80 st. C), z substancjami skrajnie niebezpiecznymi, gazami z biofiltracji, unieszkodliwiania odpadów.
To informacje, które mogą mieć znaczenie dla projektantów, którzy planują zbiornik dostosowując jego wymiary do powierzchni, jaką dysponują – niestety dobór technologii wykonania jest zależny od wielu czynników.
To wszystko jest ważne nie tylko dla projektantów i technologów ze względu na szeroki wachlarz zastosowań, jak również dla działów inwestycyjnych pod kątem korzyści ekonomicznych, jakie daje technologia nawojowa. Ale co konkretnie wpływa na oszczędności?
Przy wykonaniu zbiornika AmargTank SafeSeamLess® metodą nawojową wytłaczamy na linii produkcyjnej płynną wstęgę tworzywa o konkretnej, wręcz dowolnej grubości (ale wynikającej ze statyki!). Do tego po produkcji pozostaje jedynie ograniczona ilość odpadów materiału, którą możemy ponownie użyć na linii do mniej wymagających zastosowań. Przy wykorzystaniu płyt jesteśmy zmuszeni obliczoną w programie grubość ścianki podnieść w górę, stosownie do wielkości handlowych.
Dodatkowo w przypadku zbiorników o wysokościach np. 4 czy 6 m, w dolnej partii zbiornika ciśnienie jest większe/siły są większe, w związku z czym w tej części ścianka jest grubsza i zmniejsza się ku górze. Z reguły ze względów ekonomicznych jej wysokość jest zależna od wymiaru handlowego płyty tworzywa – czyli załóżmy przy wykorzystaniu płyt o wymiarach 3000 x 1500 mm stosujemy racjonalnie do szerokości płyty 1500 mm jedną, większą grubość tworzywa, a dopiero wyżej cieńszą. Z kolei rury nawijane helikalnie pozwalają na optymalne wykorzystanie tworzywa z różną grubością, stopniując ją np. co 20–30 cm, zależnie od wysokości zbiornika. W przypadku budowy zbiornika o takich samych gabarytach i funkcji oszczędności materiałowe względem produkcji z pojedynczych arkuszy mogą wynosić nawet 27%.
Jeśli dodatkowo pod uwagę weźmiemy brak odpadów z dostępnych na rynku wielkości płyt, brak zużycia spoiwa (drutu spawalniczego), możliwość zastosowania mniejszych grubości ścianek (pamiętajmy, że statyka liczona dla płyty spawanej narzuca uwzględnienie w obliczeniach współczynników osłabienia spoin, a tym samym wymusza stosowanie większej grubości ścianki), to w efekcie spadek ilości tworzywa do produkcji metodą nawojową może wynieść nawet 38%. Dodatkowo dzięki technologii możemy wykonać zbiornik pionowy o litej ściance i z profilem (AmargTank MultiLayer®), co dodatkowo wpływa na zmniejszenie wagi zbiornika.
To wszystko przynosi nie tylko korzyści ekonomiczne dla inwestorów – warto podkreślić ekologiczny aspekt technologii, którego największym beneficjentem jest nasza planeta.
Bezpieczna eksploatacja i żywotność zbiorników przemysłowych na substancje chemiczne
Pozostając jeszcze przy konstrukcji zbiorników produkowanych metodą nawojową warto podkreślić, co pokrótce zostało już naznaczone wcześniej, że specyfika wytwarzania rur wiąże się z brakiem miejsc zgrzewów na cylindrze. Ma to znaczenie w kontekście bezpiecznej eksploatacji i żywotności zbiorników.
Już na etapie obliczeń statyki zbiornika program dla tej samej geometrii i warunków pracy pozwala zastosować mniejszą grubość tworzywa nawijanego helikalnie beznaprężeniowo i bezspoinowo. Tym samym konstrukcja cylindra, nawet o dużych gabarytach, jest pozbawiona szwów, czyli miejsc zgrzewu, które to – przy uwzględnieniu współczynników redukcyjnych – wpływają wymiernie na wzrost grubości ścianek, aby uzyskać optymalną wytrzymałość zbiornika. Warto nadmienić, że wytrzymałość konstrukcji warunkowana jest wytrzymałością najsłabszych miejsc – w tym wypadku spoin / zgrzein. Cylindry pozbawione spoin / zgrzein płyt są bezpieczniejsze, ponieważ miejsca narażone na nieszczelność są całkowicie wyeliminowane.
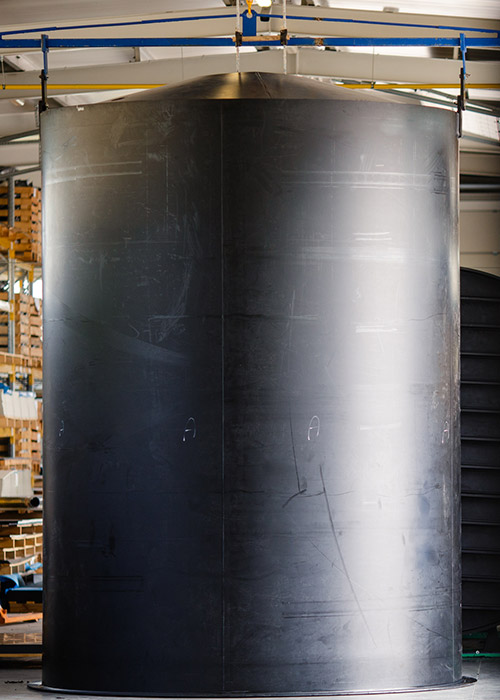
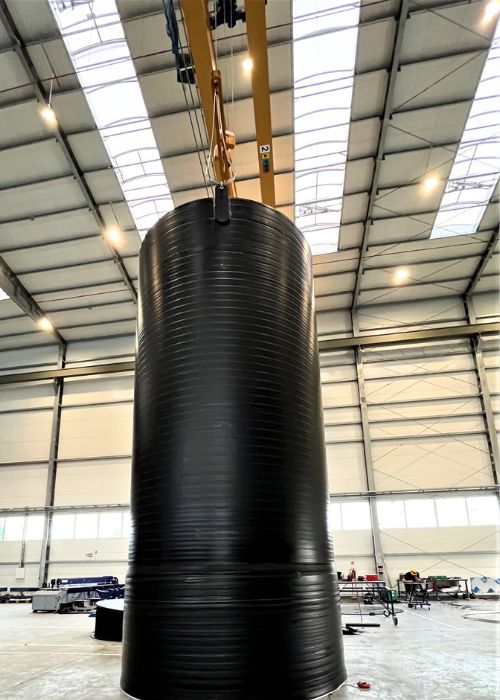
Możliwości materiałowe w konstrukcjach zbiorników przemysłowych
Jak wskazano wcześniej, zbiorniki z rury nawojowej można wykorzystać do zastosowań, dla których statyka zgrzewanego klasycznie zbiornika osiąga punkt krytyczny. Poza optymalną i racjonalną konstrukcją zbiornika technologia daje użytkownikom także inne korzyści.
W zależności od konkretnych potrzeb klienta do produkcji takich zbiorników możemy zastosować szeroką gamę tworzyw, w tym polietylen HDPE, PE 100 RC (Resistance to Crack – odporny na propagację pęknięć), polipropylen PP-R, PP-B, PE-EL (elektroprzewodzący), PP-S (trudnozapalny) czy PPS-EL.
W produkcji metodą nawojową mamy możliwość użycia granulatu –zarówno w formie pierwotnej, jak i mieszanek z dodatkami specjalistycznymi i pigmentami oraz dodatkami stabilizującymi na UV i wpływ warunków zewnętrznych. Wśród takich granulatów modyfikowanych mogę jako przykład podać polietylen Hostalen typ PE-RT (Resistance to Temperature) o podwyższonej odporności cieplnej, dający możliwość projektowania polietylenowych zbiorników odpornych na temperaturę 80 st. C. oraz wykazujący wysoką odporność na większość niebezpiecznych substancji chemicznych, w szerokim zakresie ich stężeń. Takie rozwiązanie znajduje zastosowanie np. przy produkcji zasobników do odzysku ciepła z agresywnych ścieków przemysłowych – tzw. akumulatorów ciepła / chłodu i to w wykonaniu w pełni chemoodpornym. Dzięki niemu wykonawca instalacji w zakres których wchodzą zbiorniki chemoodporne, bez ryzyka zapewni długi okres gwarancji, a użytkownik końcowy zyska realne oszczędności kosztów utrzymania ruchu, gdyż zbiorniki nie będą wymagały częstych konserwacji i przeglądów.
Poza wspomnianym przykładem użycie granulatów modyfikowanych oraz z włóknem szklanym w strukturze tworzywa umożliwia stosowanie zbiorników w zawansowanych aplikacjach, co daje jeszcze większą swobodę projektowania i aplikacji w obszarach, w których zwyczajnie tworzywo nie było dedykowane.
Wykorzystanie dodatkowych włókien w tworzywie jest innowacją, którą sukcesywnie rozwijamy. Mają one wpływ na zwiększenie sztywności i odporności na ciśnienie, które odgrywa ważną rolę w procesie wymiarowania zbiornika i wynika z rodzaju medium (jego gęstości i lepkości).
Bezpieczeństwo przechowywania substancji agresywnych w zbiornikach
Powracając do kwestii bezpieczeństwa – w standardowej technologii w celu kontroli poziomu medium czy stanu przepełnienia wykonuje się drugi płaszcz o pełnej wytrzymałości (tzw. zbiornik w zbiorniku), a następnie zabudowuje się sondę detekcji wycieku działającą na zasadzie przewodzenia elektrycznego lub pływak. Bywają to jednak systemy mało dokładne i mało efektywne, ale są one najbardziej optymalne dla takich konstrukcji.
W standardowej technologii realizuje się więc konstrukcje dwupłaszczowe z monitoringiem „zewnętrznym” lub wykonuje się wannę wychwytującą. Przy zbiornikach wykonywanych innowacyjną technologią nawojową stosujemy tworzywowy system dwuścienny (AmargTank MultiLayer DoubleWall®), co daje możliwość monitorowania części międzywarstwowej. Jednym słowem są warunki do aplikacji w przestrzeni międzyściankowej tworzywa np. systemu nad- lub podciśnieniowego monitoringu szczelności / detekcji wycieków. To daje użytkownikowi zbiornika możliwość precyzyjnego pomiaru zmian ciśnienia pomiędzy obiema płaszczyznami zbiornika: wewnętrzną i zewnętrzną.
Poglądowy schemat systemu dwuściennego z detekcją przestrzeni międzywarstwowej (AmargTank MultiLayer DoubleWall®)
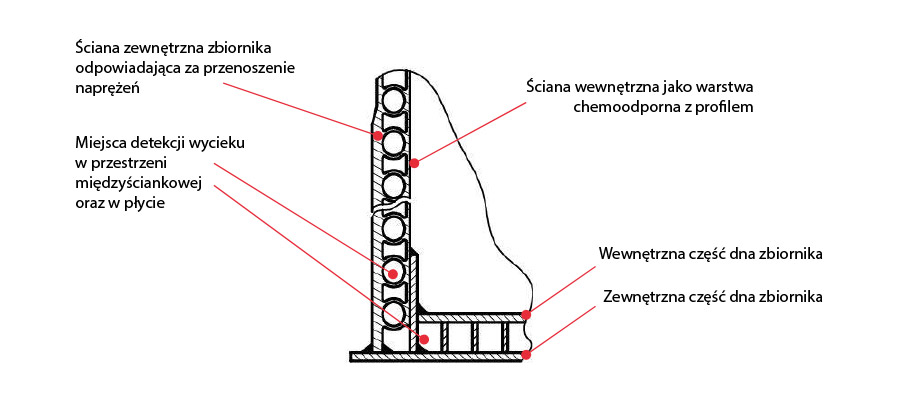
Korzyści konstrukcji dwuściennej w kontekście zastosowania zbiorników przemysłowych z tworzywa
W przeciwieństwie do zbiorników wykonywanych z jednolitych materiałów, z uwagi na brak znajomości technik łączenia zróżnicowanych warstw, w przypadku konstrukcji cylindra metodą nawojową możemy wykonać ściankę dwuwarstwową z szerokiej gamy różnych od siebie materiałów. To zapewnia zmultiplikowane korzyści wykorzystywania (mam tu na myśli możliwość wykonania ścianki wewnętrznej (mającej kontakt z medium) z materiału o innych właściwościach aniżeli część zewnętrzna – konstrukcyjna zbiornika).
Dodatkowo takie rozwiązanie może stanowić od strony użytkowej np. barierę antydyfuzyjną lub służyć do monitorowania stanu zbiornika (np. w przypadku zbiorników z mieszadłem dzięki wewnętrznej warstwie w innym kolorze możemy sprawniej dokonywać weryfikacji stopnia ścierania się tejże warstwy).
Od strony ekonomicznej konstrukcja dwuścienna daje nam możliwość użycia tańszego materiału na zewnątrz zbiornika, a wewnątrz – zależnie od przeznaczenia – np. z atestem PZH – Państwowego Zakładu Higieny. Do tego dochodzi możliwość budowy zbiornika z zabudowaną warstwą izolacji (np. profil wypełniony poliuretanem), co w przypadku zbiorników zewnętrznych bywa niezwykle istotne.
Najważniejsze linie produktowe z zakresu zbiorników wytwarzanych technologią nawojową
Wśród obecnie oferowanych rozwiązań znajdują się:
- chemoodporne zbiorniki magazynowe dozorowe na kwas siarkowy H2SO4 o stężeniu 96-98% o jednorodnej w przekroju ściance litej,
- dwuścienne zbiorniki tworzywowe magazynowe UDT podziemne odcieków kwasu siarkowego (VI), popłuczyn, ścieków przemysłowych wraz z modułową chemoodporną pompownią,
- dwuścienne zbiorniki magazynowe UDT podziemne np. na koagulanty PIX wraz z izolacją i ogrzewaniem,
- zasobniki ścieków w ramach pomp ciepła (odzysk ciepła ze ścieków) oraz akumulatory gorącej wody i chemikaliów, a także agresywnych ścieków przemysłowych,
- komory i obudowy zasuw lub pomp wykonane z niekorodującego odpornego tworzywa polietylenu wysokiej gęstości PE-HD,
- poziomy odstojnik popłuczyn z rury dwuściennej z gładkimi ściankami – zewnętrzną czarną, gwarantującą pełną odporność na promieniowanie UV i wewnętrzną jasną ułatwiającą inspekcję wraz z układem pompowym wody nadosadowej i zintegrowanym wspawanym ekstruzyjnie fabrycznie pionem tłocznym oraz systemem sterowania – jako kompletne działające urządzenie.
Oczywiście w zależności od zastosowania i konkretnych potrzeb, zbiorniki wyposażamy w kominy z włazami i pokrywami oraz systemy detekcji wycieku do przestrzeni międzyściankowej, czujniki pomiaru poziomu, sygnalizacji napełnienia itp. o których już wcześniej nieco wspominaliśmy.
Do współpracy zapraszamy zarówno projektantów, jak również przedstawicieli działów technicznych i utrzymania ruchu reprezentujących zakłady, w których wykorzystywane są substancje żrące o wysokich stężeniach, gęstości oraz temperaturze pracy – wspólnie sprostamy wszelkim wyzwaniom technicznym.
Porozmawiajmy o rozwiązaniu Twojego wyzwania
Rozmowa to klucz do sukcesu. Skorzystaj z naszej wiedzy i doświadczenia.