ZAKRES PUBLIKACJI: ZBIORNIK CHEMOODPORNY | ZBIORNIK PROCESOWY | PROJEKTOWANIE ZBIORNIKÓW I INSTALACJI
BRANŻA: PRZEMYSŁ KOSMETYCZNY
Inwestycja zapewniająca rozwój przedsiębiorstwa – zbiorniki procesowe z instalacjami w ramach budowy nowej linii technologicznej
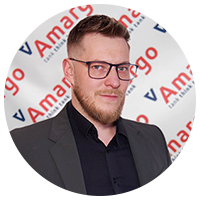
Grzegorz Zając, Ekspert z zakresu zbiorników i instalacji przemysłowych z tworzyw sztucznych
Jak nie tylko spełniać, ale i wyprzedzać rosnące oczekiwania swoich Klientów? Przedsiębiorstwa przemysłowe, które odpowiadają na dynamicznie zmieniające się potrzeby rynku oraz podążają za najnowszymi trendami, konsekwentnie stawiają na innowacje i rozwój technologiczny. Inwestując w nowoczesne zaplecze produkcyjne, zakłady mają szanse wprowadzać na rynek coraz bardziej zróżnicowany asortyment.
W artykule pokazujemy historię realizacji dla jednego z kluczowych oddziałów producenta kosmetyków, który skupił swoje działania na uruchomieniu nowoczesnej linii technologicznej. Celem było zwiększenie wydajności produkcji, a także wprowadzenie nowych produktów. Dzięki temu firma umacnia swoją pozycję na rynku, dostosowując ofertę do indywidualnych preferencji swoich Klientów.
Założenia koncepcyjne inwestycji w nową linię technologiczną
Przełożenie koncepcji wzorcowej instalacji na projekt
Projekt nowej linii technologicznej bazował na sprawdzonym modelu instalacji, która funkcjonuje w innym oddziale koncernu. Wdrożenie tej koncepcji zakładało adaptację istniejących rozwiązań do specyficznych potrzeb zakładu. Wykorzystanie sprawdzonych technologii miało na celu zminimalizować ryzyko i usprawnić proces uruchomienia.
Wykonanie zautomatyzowanej linii technologicznej w określonych oknach czasowych
Budowa linii technologicznej obejmowała zbiorniki procesowe oraz towarzyszące im instalacje. Całość miała być w pełni zautomatyzowana, aby zoptymalizować procesy produkcyjne i zapewnić efektywność. Prace te musiały zostać zrealizowane zgodnie z określonym harmonogramem, uwzględniając tzw. „okna czasowe” minimalizujące przestoje produkcyjne.
Dostosowanie armatury do wewnętrznych standardów zakładu
Armatura technologiczna musiała spełniać wewnętrzne wymogi przedsiębiorstwa (zarówno jeśli chodzi o funkcjonalność jak i markę produktu).
Projekt zbiorników procesowych oraz linii przesyłu i dozowania medium
Na etapie zlecenia, Inwestor dysponował już schematem instalacji procesowej (P&ID), który bazował na linii pracującej w siostrzanym zakładzie. Celem projektu było dostosowanie istniejącego schematu do specyficznych warunków panujących w przedsiębiorstwie.
Kluczowe zadania obejmowały precyzyjne określenie lokalizacji urządzeń instalacji oraz dobór odpowiedniej armatury, w tym mieszadeł, pomp i zaworów. W ramach projektu Klient otrzymał rysunki wykonawcze zbiorników, zestawienie materiałów, szacunkowy harmonogram prac oraz karty materiałów zaprojektowanych do produkcji zbiorników wraz z dokumentacją techniczną dodatkowego wyposażenia.
Efektem prac było zainstalowanie trzech nowych zbiorników:
- zbiornik procesowy na wodny roztwór chlorku sodu,
- zbiornik pośredni na Betainę,
- zbiornik pośredni na Aluminium Zirconium.
Zostały one wyposażone w instalacje do transferu i dozowania czynnika roboczego. Każdy z nich pełni kluczową rolę w procesie produkcji, umożliwiając efektywne zarządzanie przepływem medium oraz precyzyjne dozowanie surowca do dalszych etapów produkcji.
Co zdecydowało o współpracy z Amargo?
Do decyzji o współpracy z Amargo przekonały nas podobne realizacje firmy, które były przeprowadzane już od etapu koncepcji. Kolejnym atutem było zaplecze projektowe i wykonawcze, dzięki czemu mogliśmy bez obaw zlecić kompleksowy zakres prac. Inwestycja pozwala na wprowadzenie nowego produktu na rynek.
Maciej Kowalewski, Projekt Leader w przedsiębiorstwie kosmetycznym
Zbiornik procesowy (technologiczny) na przygotowanie roztworu solanki
Zbiornik procesowy na chlorek sodu (NaCl) w stężeniu 20% i gęstości do 1,15 g/cm³ został wykonany w technologii AmargTank ClassicWeld®. Konstrukcja zbiornika, o pojemności roboczej 5,8 m³, została zbudowana z gotowych arkuszy tworzywa PP-H. Posiada on pionowy, cylindryczny kształt oraz dno skośne ze spadkiem wynoszącym około 2%, co umożliwia efektywne odprowadzanie medium. W dolnej części zamontowano króciec odpływu.
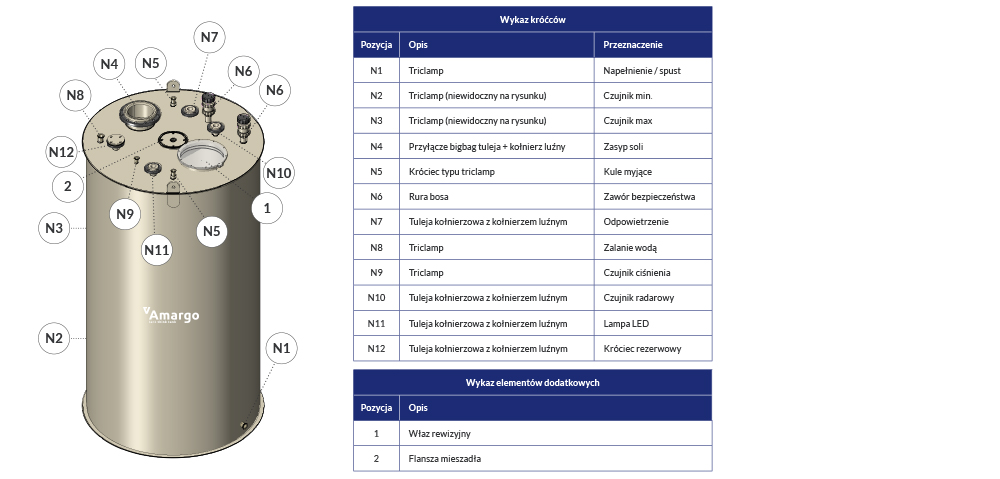
Rys. 1. Zbiornik procesowy na roztwór solanki.
Na etapie projektowania i produkcji przewidziano wyposażenie zbiornika procesowego na roztwór solanki w następujące elementy:
- właz z pokrywą transparentną z poliwęglanu ułatwiający kontrolę wizualną,
- wolnoobrotowe mieszadło łopatkowe do przygotowania roztworu solanki,
- mikrofiltr do filtracji powietrza eliminujący ryzyko zanieczyszczenia medium oraz pozwalający utrzymać jakość roztworu,
- obrotowe głowice myjące do skutecznego czyszczenia mieszalnika na całej wewnętrznej powierzchni.
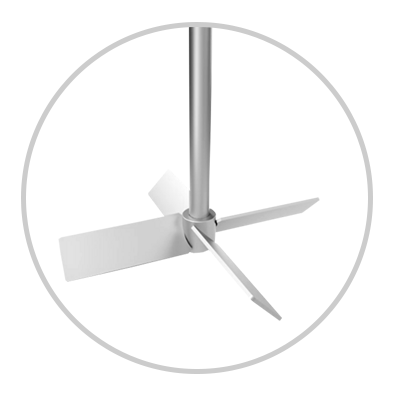
Mieszadło łopatkowe
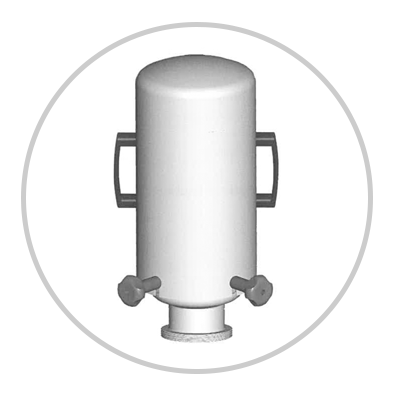
Mikrofiltr
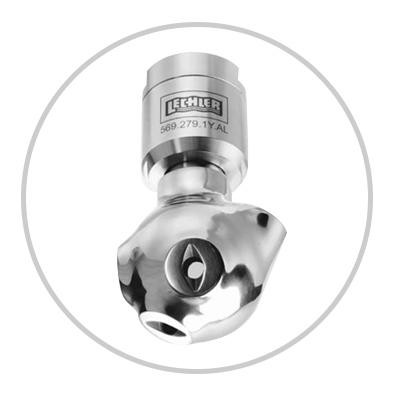
Głowica (kula) myjąca
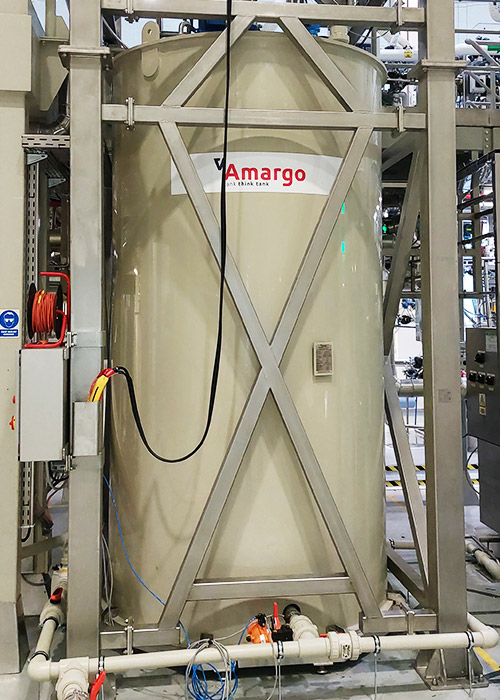
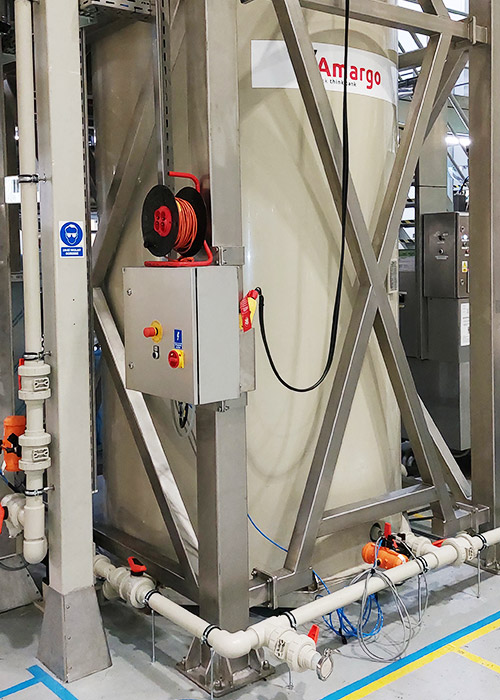
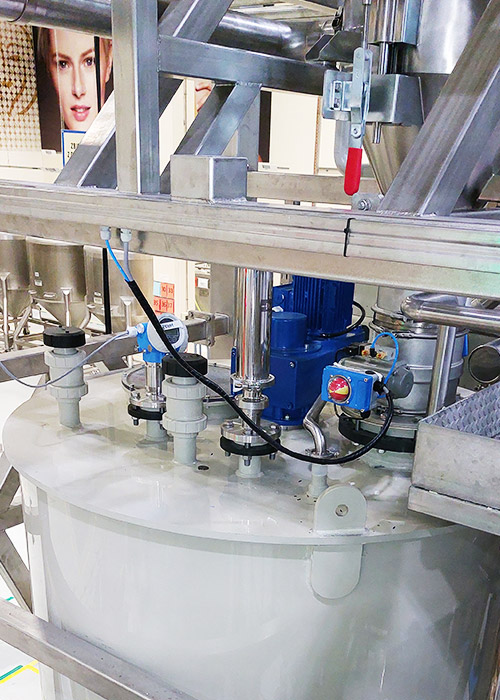
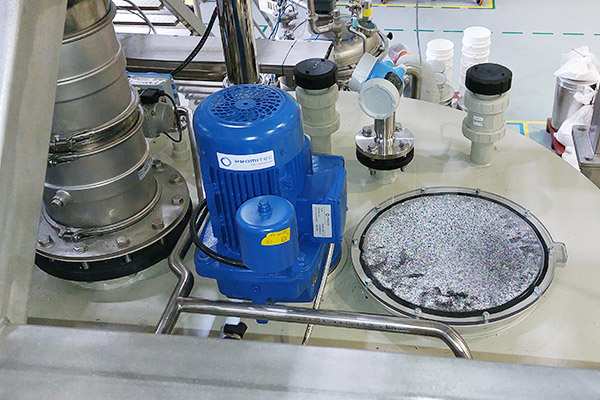
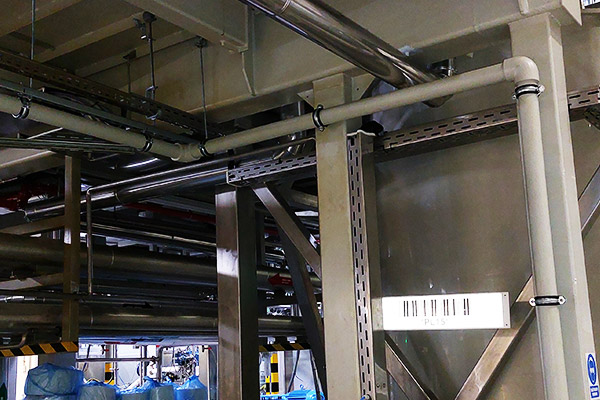
Zbiornik procesowy na roztwór solanki – zdjęcia z realizacji.
Zbiorniki pośrednie na Betainę i Aluminium Zirconium
W innej części linii technologicznej zainstalowano prostopadłościenne zbiorniki pośrednie na Betainę i Aluminium Zirconium. Surowce te będą dostarczane do nich ze zbiorników IBC, a następnie dozowane na dalsze etapy procesu produkcyjnego.
Oba zbiorniki mają dno skośne, które jest pochylone w kierunku króćca odpływowego, co umożliwia efektywne opróżnianie. Cała konstrukcja zbiorników została wykonana w technologii AmargTank MultiPower®, wykorzystując płyty modułowe (inaczej sandwichowe) o wysokiej wytrzymałości.
Każdy zbiornik wyposażono w kątowy zawór pływakowy, do którego zamocowano pionową rurę napełniającą z PP. Rura ta jest zakończona 200 mm nad dnem zbiornika, co zapobiega powstawaniu w nim fali podczas napełniania. Dodatkowo, w rurze wykonano otwór nad lustrem wody oraz pod przyłączem kołnierzowym, aby zniwelować efekt ciśnienia przeciwstawnego działającego na membranę zaworu pływakowego.
W przypadku zbiornika na Betainę, z uwagi na charakter medium, zamontowano dodatkowo pionowe mieszadło kubełkowe. Jego zadaniem jest zapewnienie równomiernego mieszania substancji w całej objętości zbiornika oraz zapobieganie gromadzeniu się osadów w dolnych partiach.
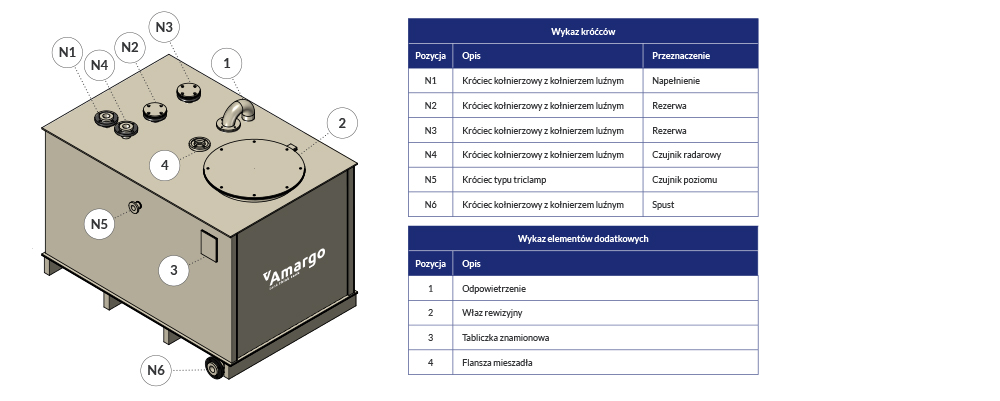
Rys.2. Zbiornik bezciśnieniowy na Betainę o pojemności roboczej 1,65 m3. Zbiornik na Aluminium Zirconium o pojemności roboczej 2,6 m3, podobnej konstrukcji, bez mieszadła.
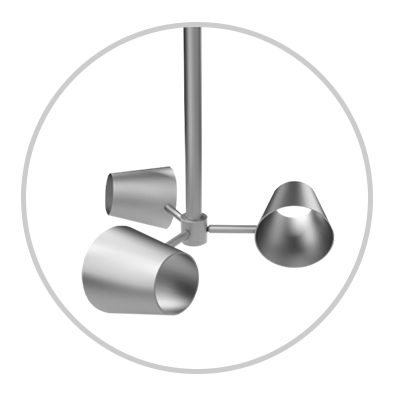
Mieszadło kubełkowe
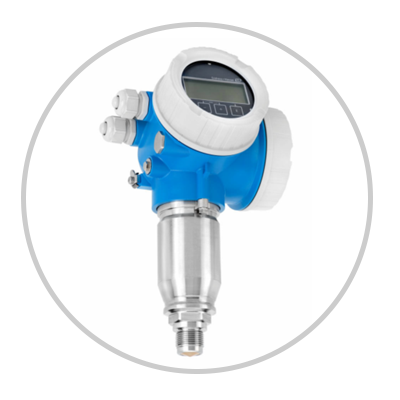
Czujnik radarowy
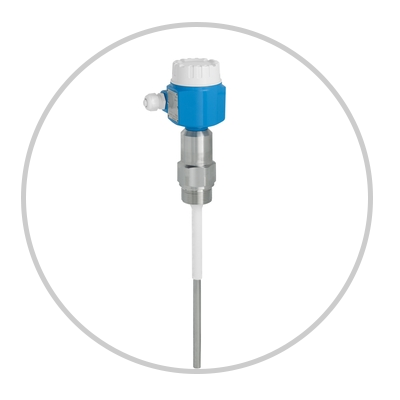
Pojemnościowy sygnalizator poziomu
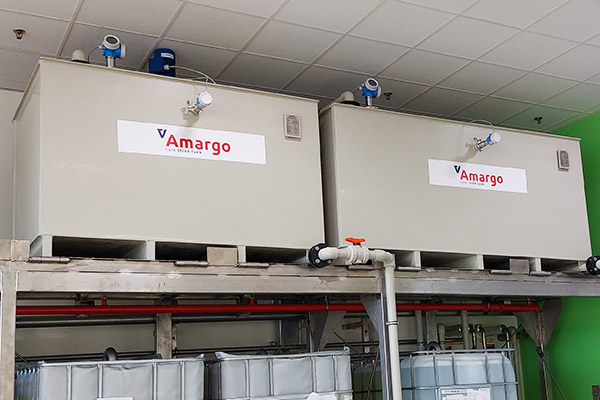
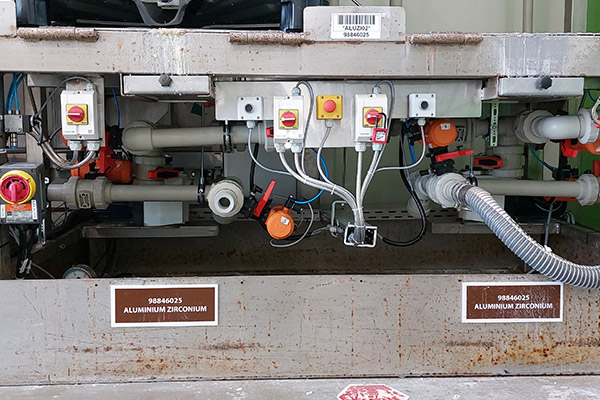
Zbiorniki pośrednie na Betainę i Aluminium Zirconium – zdjęcia z realizacji.
Zautomatyzowana linia przesyłu i dozowania substancji do i ze zbiorników pośrednich
Poza samymi zbiornikami wraz z oprzyrządowaniem wykonano montaż instalacji:
- napełniającej zbiorniki,
- dozującej od zbiorników na linię technologiczną.
Wśród elementów instalacji znalazły się:
- rurociągi chemoodporne z tworzywa,
- pompy ze sprzęgłem magnetycznym (samozasysające pompy wirowe),
- zawory manualne,
- zawory automatyczne,
- zawory odpowietrzające i napowietrzające.
Jakie zalety niesie za sobą wdrożenie automatyzacji?
Transfer i dozowanie medium na nowej linii technologicznej zostały w pełni zautomatyzowane. System sterowania ma kluczowe znaczenie, ponieważ nie tylko zwiększa wydajność i efektywność procesu, ale także zapewnia bezpieczeństwo oraz komfortowe warunki pracy dla personelu. Dzięki automatyzacji możliwe jest precyzyjne monitorowanie i kontrolowanie przepływu substancji, co redukuje ryzyko błędów ludzkich i poprawia jakość produkcji.
Dodatkowo, automatyczne systemy zabezpieczeń i alarmów, zintegrowane z linii, minimalizują ryzyko wystąpienia awarii oraz umożliwiają szybką reakcję w przypadku nieprawidłowości. Pracownicy zyskują również więcej czasu na nadzór i optymalizację procesów, co przyczynia się do zwiększenia ogólnej efektywności zakładu.
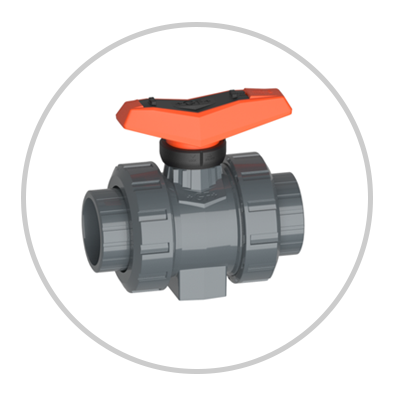
Zawór manualny
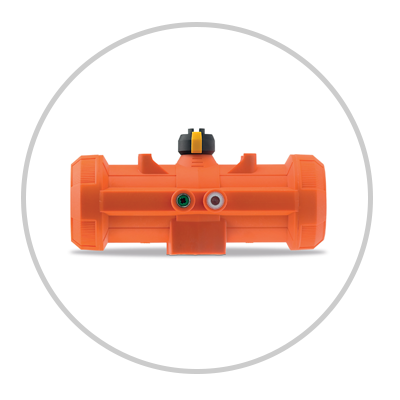
Zawór automatyczny
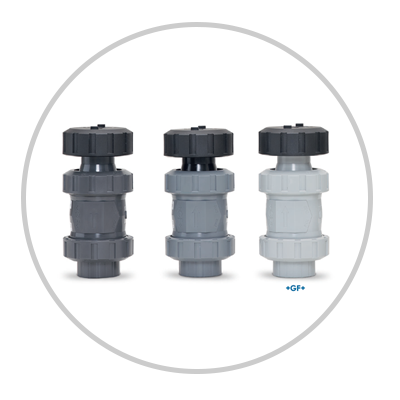
Zawory odpowietrzające
i napowietrzające
Podsumujmy korzyści, jakie zyskał Inwestor
Zmaterializowanie koncepcji i przekształcenie jej na projekt umożliwiło skuteczną realizację planu rozwojowego przedsiębiorstwa, co przyczyniło się do zwiększenia jego konkurencyjności na rynku.
Wykonanie instalacji zgodnie z wymaganymi standardami oraz w ustalonych ramach czasowych pozwoliło na odpowiednie przygotowanie do terminowego uruchomienia nowej linii technologicznej, co minimalizuje ryzyko opóźnień w produkcji.
Implementacja zautomatyzowanych rozwiązań zapewnia kontrolowany i bezpieczny przebieg procesów technologicznych. To z kolei przekłada się na niezawodność, zwiększoną wydajność oraz wysoką jakość produkcji, co sprzyja dalszemu rozwojowi przedsiębiorstwa.
W publikacji wykorzystano zdjęcia Endress+Hauser, +Georg Fischer+, Hennlich oraz materiały własne.
Jeśli i Ty mierzysz się z wyzwaniami związanymi ze strategicznymi inwestycjami przedsiębiorstwa, rozważ konsultację z naszym zespołem ekspertów. Pomożemy Ci obrać właściwą ścieżkę postępowania, która umożliwi osiągnięcie celów bez zbędnych komplikacji.
Porozmawiajmy o rozwiązaniu Twojego wyzwania
Rozmowa to klucz do sukcesu. Skorzystaj z naszej wiedzy i doświadczenia.