Skomplikowana geometria, napięty harmonogram – case study z zabezpieczenia chemoodpornego zbiornika reakcyjnego
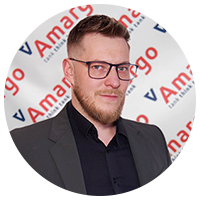
Grzegorz Zając, Ekspert z zakresu zbiorników i instalacji przemysłowych z tworzyw sztucznych
Praca w działach technicznych i utrzymania ruchu to nieustanne balansowanie między presją czasu, ograniczonymi zasobami a ogromną odpowiedzialnością za sprawne funkcjonowanie infrastruktury. Każda awaria lub nieoczekiwane wydłużenie prac serwisowych mogą skutkować nieplanowanym przestojem linii produkcyjnej, co bezpośrednio przekłada się na straty i destabilizuje działalność przedsiębiorstwa.
Można tego uniknąć. Zamiast czekać na nieprzewidziane awarie prowadzące do kosztownych przestojów, warto optymalnie wykorzystać planowane przerwy technologiczne.
Jak dobrze wykorzystać planowaną przerwę w produkcji?
Dla każdego zakładu przemysłowego planowana przerwa technologiczna to ujęty w harmonogramie pracy fabryki okres, który jest idealnym momentem na przeprowadzenie niezbędnych prac serwisowych i naprawczych. Szczególnie w obrębie kluczowych elementów linii, które są w ciągłej eksploatacji, dla których ciężko zaplanować te prace w trakcie standardowego funkcjonowania zakładu, bez ryzyka zakłócenia procesów.
W tym okresie pojawiają się jednak wyzwania związane z koniecznością wyboru priorytetowych zadań przy ograniczonym budżecie, opóźnionymi decyzjami przełożonych oraz problemami logistycznymi – takimi jak niechęć wykonawców do realizacji prac na odległych obszarach czy w mniej dogodnych terminach.
Wszelkie działania serwisowe i konserwacyjne wymagają precyzyjnego harmonogramu oraz skutecznej koordynacji zespołów: zakładowego i wykonawcy. Wszystko po to, by uniknąć opóźnień i zapewnić sprawne wznowienie produkcji w terminie ujętym w harmonogramie pracy zakładu.
Aby lepiej zobrazować te wyzwania oraz sposoby radzenia sobie z nimi, przedstawiamy case study jednej z ostatnich realizacji.
Czynności zabezpieczające zbiornik procesowy
Jeden z wiodących producentów z branży przetwórstwa aluminium zgłosił się do Amargo z pilnym zleceniem. Potrzebował zabezpieczenia chemoodpornego dla stalowego zbiornika reakcyjnego z mieszadłem. Zbiornik ten miał pojemność około 30 m³ i był przeznaczony do pracy z rozcieńczonym kwasem siarkowym.
Ochrona powierzchni wewnętrznej zbiornika miała na celu wydłużenie trwałości i wydajności oraz zapobieżenie poważnym awariom, które mogłyby wykluczyć go z użytkowania na dłuższy czas.
Na pierwszy rzut oka – zadanie stosunkowo proste.
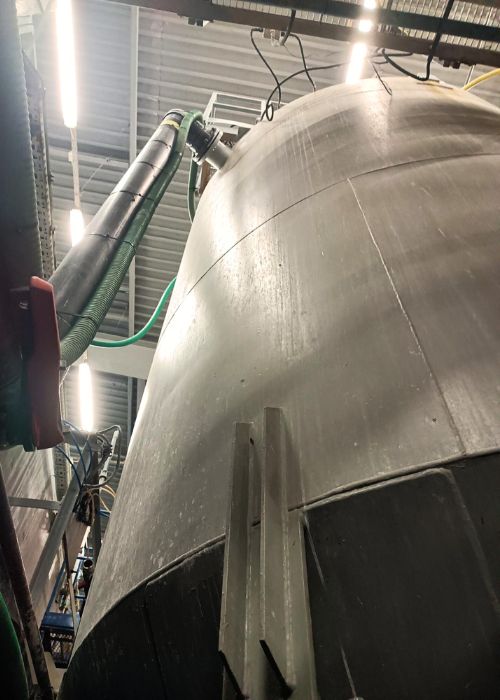
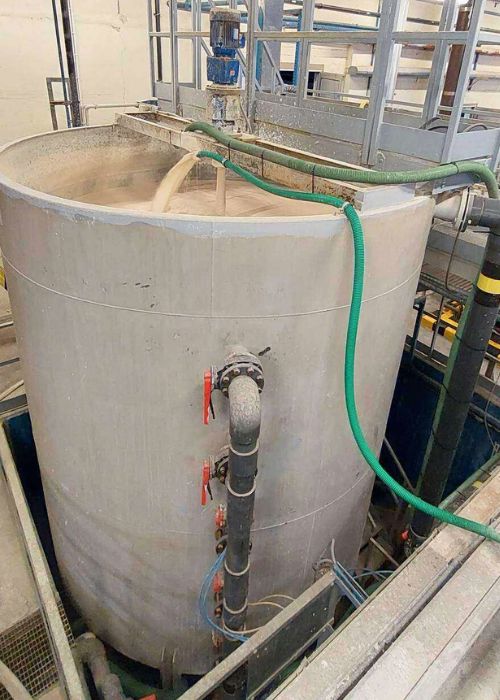
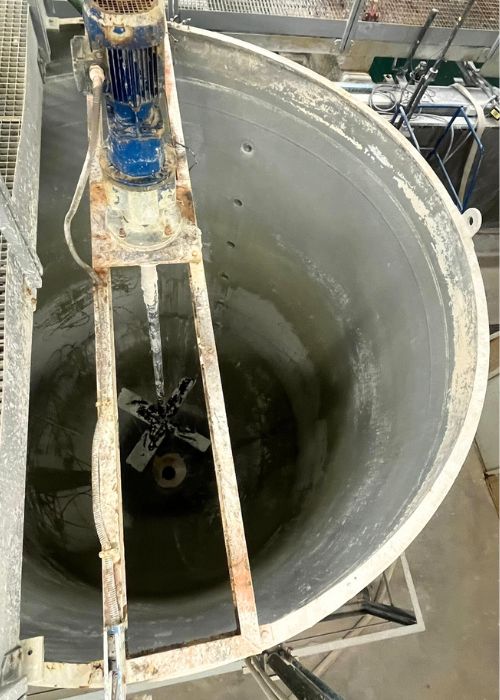
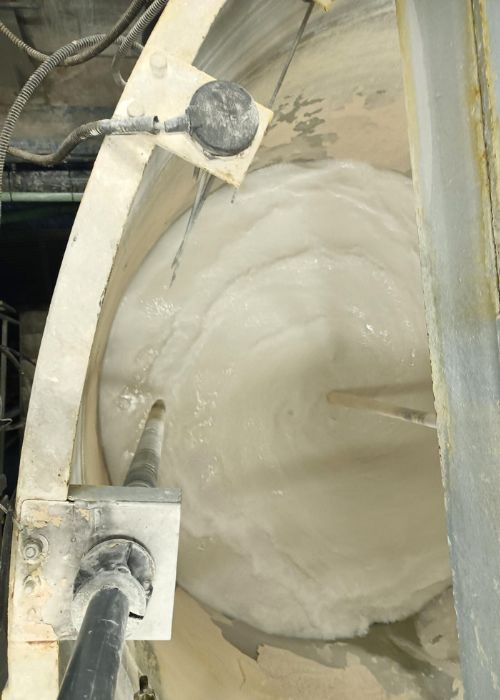
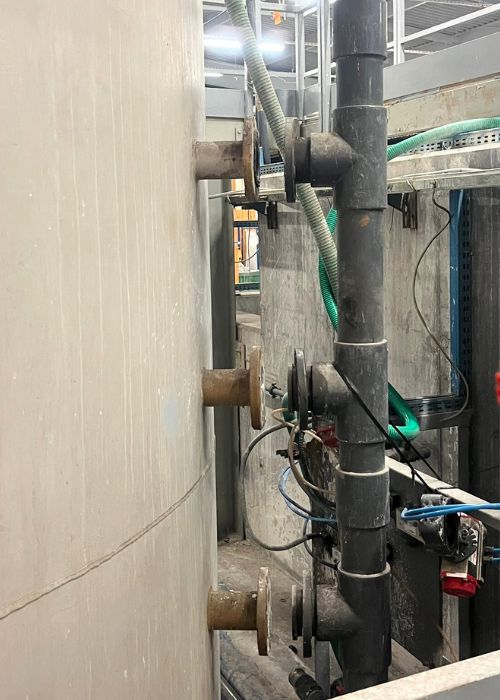
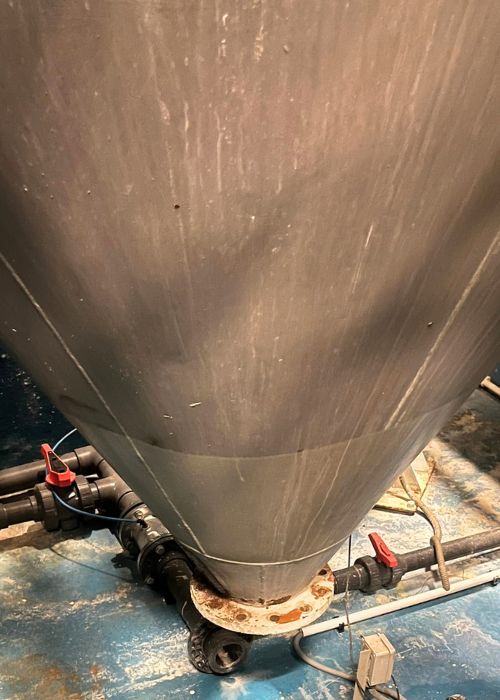
Zbiornik przed wykonaniem zabezpieczenia powierzchni wewnętrznej.
Wyzwanie 1.: Okres świąteczno-noworoczny – idealny moment dla zakładu, ale czy dla wykonawcy?
Z uwagi na to, że zbiornik pracujący na hali Anodowni był w ciągłej eksploatacji, jego zabezpieczenie musiało zostać zrealizowane w trakcie przerwy technologicznej przypadającej na okres świąteczno-noworoczny.
Klient obawiał się, czy uda się znaleźć wykonawcę, którego pracownicy będą gotowi do intensywnej pracy w czasie, który na ogół wykorzystują na urlop wypoczynkowy.
Wyzwanie 2.: Skomplikowana geometria zbiornika
Zadanie było wymagające nie tylko ze względu na termin, ale również na skomplikowaną geometrię zbiornika. Posiadał on liczne króćce oraz dno stożkowe, co wymagało niestandardowego podejścia oraz precyzyjnego zaprojektowania i wykonania wkładki chemoodpornej.
Nie czekamy – sprawdzamy i działamy!
Błyskawiczna reakcja na zgłoszenie, sprawnie przeprowadzona wizja lokalna w zakładzie oraz dokładna ocena stanu powierzchni zbiornika pozwoliły zweryfikować optymalne rozwiązanie techniczne.
Klient rozważał wykonanie zabezpieczenia z tworzywa sztucznego lub stali. Po zapoznaniu się z naszymi dotychczasowymi realizacjami i merytorycznymi argumentami przemawiającymi za proponowanym rozwiązaniem, zdecydował się na wykonanie wykładziny chemoodpornej z polipropylenu PP.
Przedstawiliśmy mu szczegółową koncepcję przebiegu prac, dostosowaną do jego potrzeb i wymaganego terminu realizacji. W międzyczasie zmobilizowaliśmy doświadczoną ekipę Amargo, która potwierdziła gotowość do pracy w dni świąteczne.
Bezpośrednia i transparentna komunikacja z Klientem pozwoliła uniknąć nieporozumień i zapewnić skuteczny przebieg realizacji.
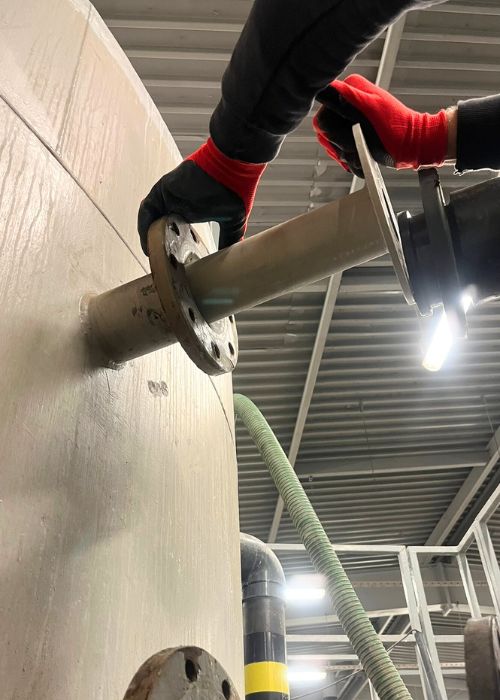
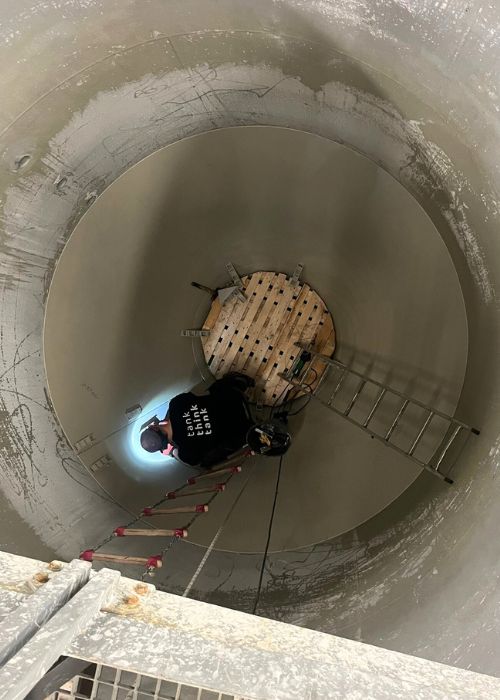
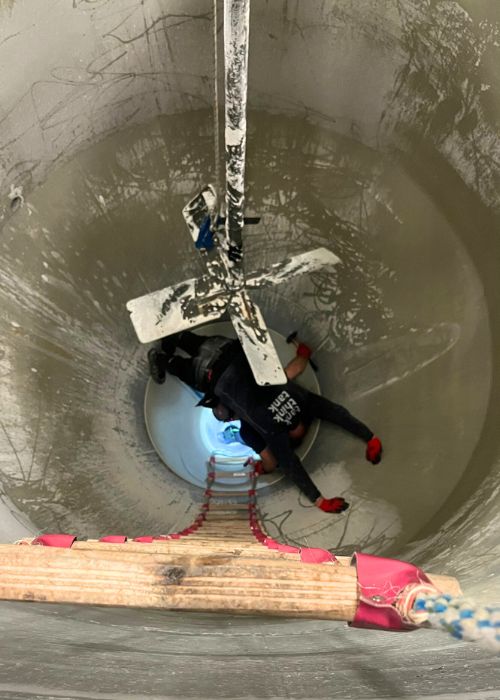
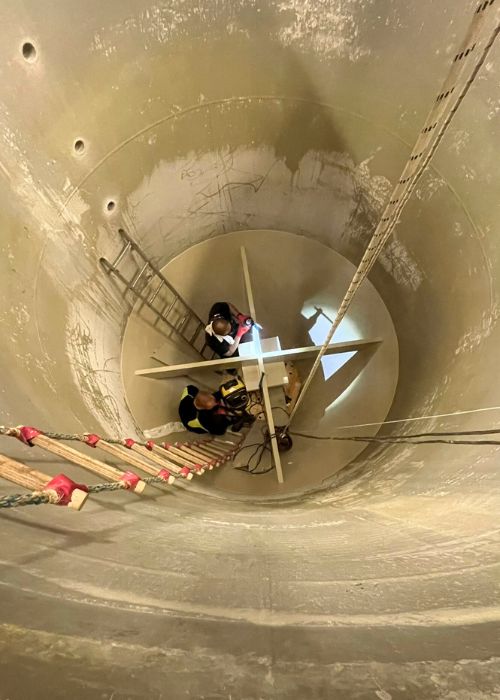
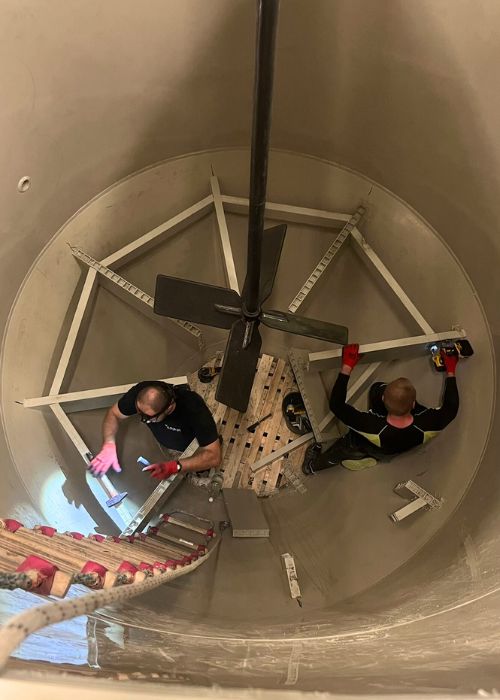
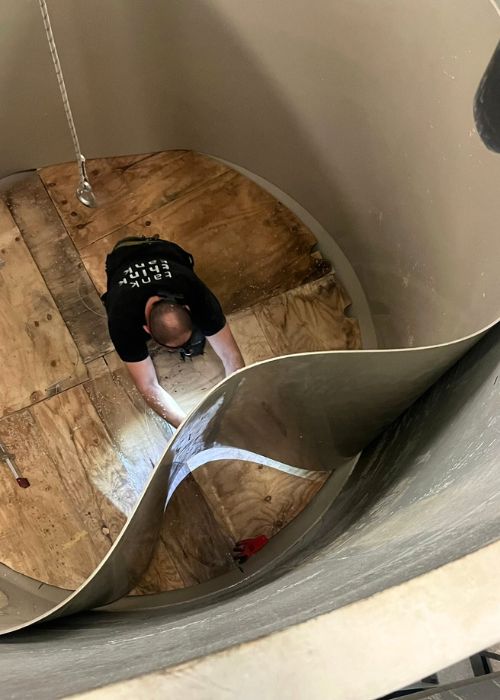
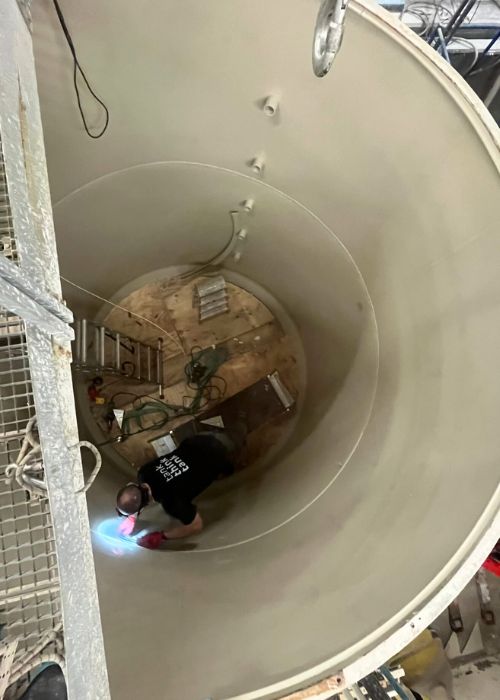
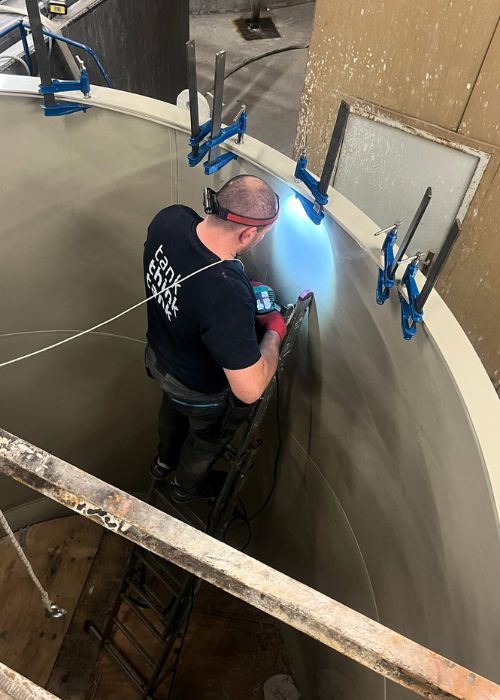
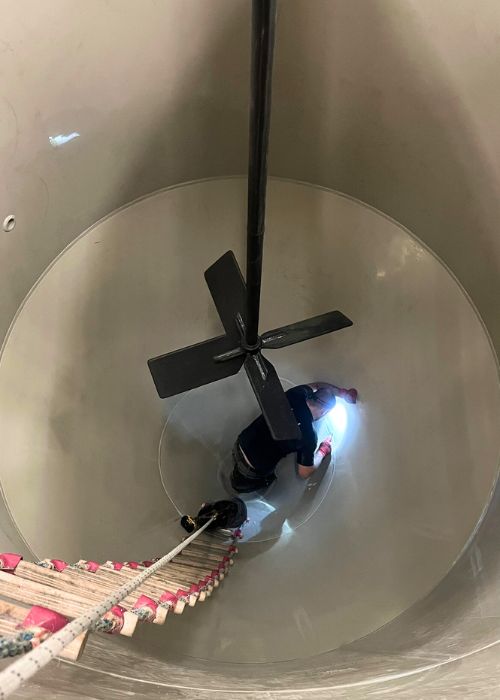
Przebieg montażu wkładki z polipropylenu PP, odpornego na działanie kwasów.
Ścisła współpraca i podział zadań pozwoliły zdążyć na czas
Kluczowym aspektem było skoordynowanie działań Amargo z zespołem utrzymania ruchu Klienta – każdy punkt harmonogramu został dopracowany tak, by zmieścić się w założonym czasie.
Prace rozpoczęły się zgodnie z planem. Klient wstępnie wyczyścił zbiornik z zalegającego medium, a następnie do działania przystąpiła ekipa Amargo.
Najpierw zdemontowaliśmy mieszadło, a później rozpoczęliśmy montaż wkładki chemoodpornej z polipropylenu (PP) o odpowiedniej grubości, spełniającej określone wymagania techniczne.
Ścisła współpraca z zakładowym działem utrzymania ruchu pozwoliła przyspieszyć proces realizacji – kolejne króćce były podłączane etapowo w trakcie montażu poszczególnych elementów wykładziny, co pozwoliło uniknąć zbędnego oczekiwania na zakończenie wszystkich prac.
Warto podkreślić, że ze względu na okres świąteczny i trwającą przerwę technologiczną, na terenie całej fabryki przebywało ze strony inwestora jedynie kilka osób.
Na zakończenie przeprowadziliśmy próbę szczelności metodą iskrowania, upewniając się, że zabezpieczenie chemoodporne powierzchni zbiornika reakcyjnego spełnia wymagania stawiane przez Klienta.
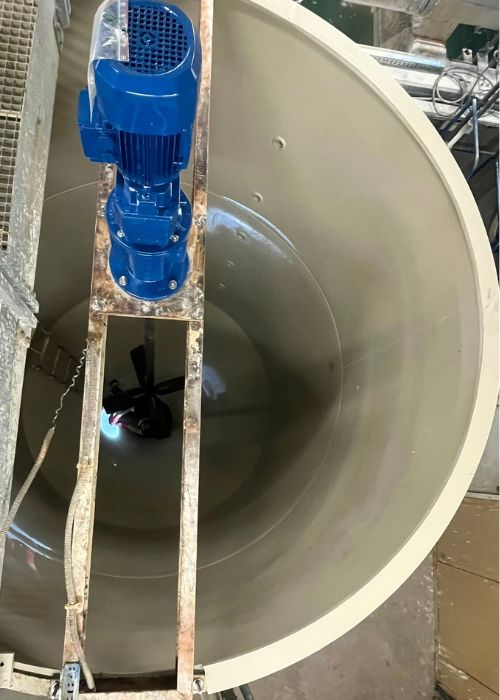
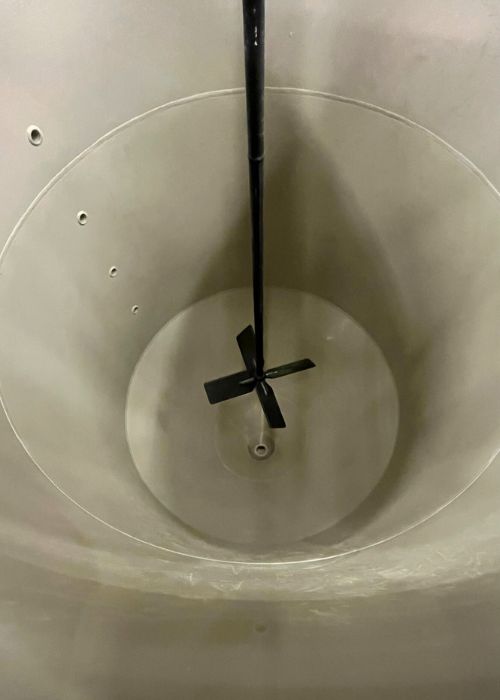
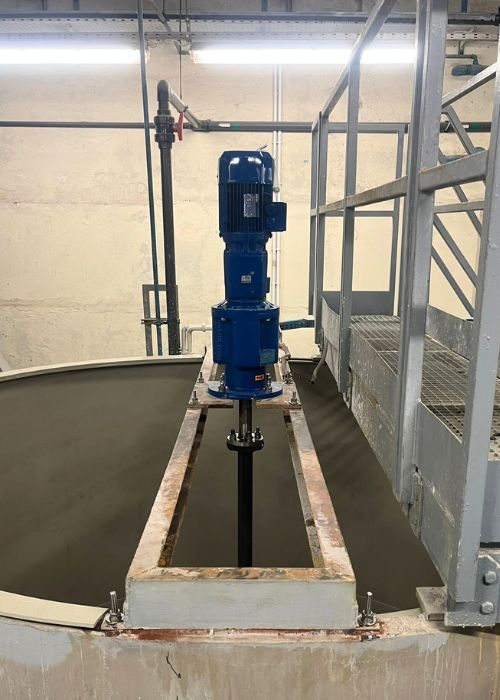
Zbiornik po wykonaniu wykładziny chemoodpornej.
Realizacja zabezpieczenia chemoodpornego zbiornika reakcyjnego w tak krótkim i wymagającym terminie była dużym wyzwaniem. Dzięki elastyczności, profesjonalizmowi i skutecznej współpracy zespołu Amargo i Klienta, udało się sprostać wszystkim wymaganiom.
Prace naprawcze nie zaburzyły planu zakładu – zbiornik został uruchomiony w założonym czasie i będzie mógł pracować bezpiecznie przez kolejne lata.
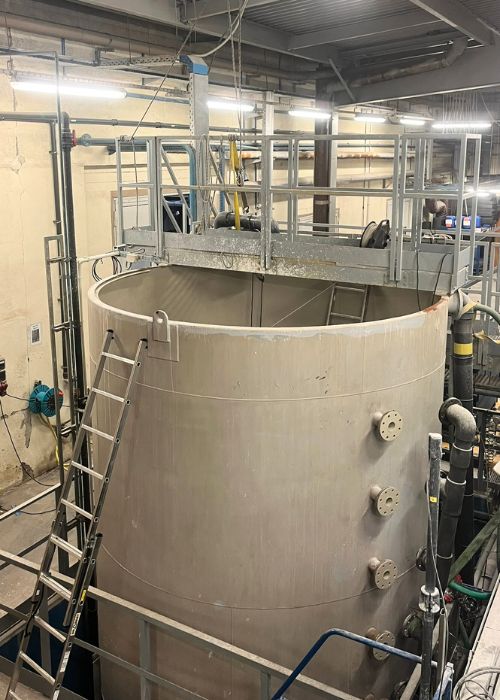
Podsumowanie prac związanych z zabezpieczeniem powierzchni zbiornika
- Demontaż mieszadła umożliwiający wykonanie wyłożenia
- Montaż wyłożenia zbiornika wykładziną z polipropylenu i przymocowania jej do istniejącej powierzchni
- Wykonanie kołnierzy pod istniejące przyłącza
- Ponowny montaż zdemontowanych wcześniej elementów
- Odbiór prac (próba szczelności, przekazanie atestów na zastosowane materiały)
Mimo trudności to często właśnie wyzwania sprawiają, że satysfakcja z realizacji zadania w założonym czasie i budżecie jest bezcenna. Stanowi nie tylko motywację do dalszego działania, ale także buduje uznanie w oczach przełożonych i zespołu, wzmacniając autorytet w organizacji.
Jeśli szukasz sprawdzonego rozwiązania zabezpieczającego powierzchnię zbiornika, skontaktuj się z nami i sprawdź zalety zastosowania wykładzin z tworzyw sztucznych.
Porozmawiajmy o rozwiązaniu Twojego wyzwania
Rozmowa to klucz do sukcesu. Skorzystaj z naszej wiedzy i doświadczenia.