ZAKRES PUBLIKACJI: ZBIORNIKI MAGAZYNOWE UDT | PROJEKTOWANIE ZBIORNIKÓW I INSTALACJI | STACJE NO
BRANŻA: PRODUCENT STALII
Case study: zbiorniki dozorowe UDT na NaOH i HCl wyposażone we wskaźnik jakości spoin wraz z absorberem oparów i stacją NO
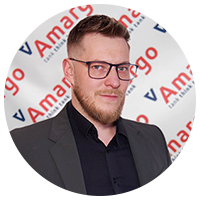
Grzegorz Zając, Ekspert z zakresu zbiorników i instalacji przemysłowych z tworzyw sztucznych
Cel inwestycji
Zapewnienie ciągłości produkcji poprzez wymianę wyeksploatowanych zbiorników dozorowych UDT na kwas solny HCl i wodorotlenek sodu NaOH, którym skończył się założony okres żywotności wraz z zapewnieniem odpowiedniego rozwiązania pozwalającego na odprowadzenie oparów HCl oraz realizacją stacji tankowania czynników roboczych
Na terenie przedsiębiorstwa zajmującego się produkcją stali znajdowały się tworzywowe zbiorniki magazynowe na substancje żrące tj. kwas solny HCl o stężeniu 33-38% oraz wodorotlenek sodu NaOH o stężeniu < 50%. Klient zwrócił się do nas za pośrednictwem obsługującej go firmy z prośbą o naprawę dekla górnego, wymianę zaworu oddechowego i przegląd stanu armatury zbiornikowej.
Podczas spotkania na miejscu u Inwestora i zapoznaniu się z dokumentacją istniejących zbiorników dozorowych okazało się, że minął założony 10-letni okres ich żywotności. W związku z tym, że nadawały się one do naprawy, a ocena stanu zbiorników pod kątem dopuszczenia do dalszej eksploatacji była utrudniona, optymalnym rozwiązaniem była decyzja o budowie nowych zbiorników magazynowych z 20-letnim okresem żywotności.
W zakres prac Amargo weszły opracowanie projektu, produkcja i dostawa chemoodpornych zbiorników magazynowych UDT z niezbędnym wyposażeniem, wykonanie absorbera oparów, stacji rozładunkowych, a także prace polegające na demontażu dotychczasowych zbiorników. Dodatkowo zlecenie obejmowało remont istniejących wanien zabezpieczająco-przechwytujących poprzez malowanie chemoodporne.
Poniżej opisujemy najważniejsze elementy związane z realizacją.
Zbiorniki magazynowe dozorowe na HCl i NaOH produkowane zgodnie z procedurą UDT
Produkcja nowych zbiorników bezciśnieniowych przeznaczonych do magazynowania materiałów trujących lub żrących wiązała się z procedurą dozorową (zbiorniki na HCl i NaOH podlegają pod dozór Urzędu Dozoru Technicznego). W takim przypadków jeszcze przed rozpoczęciem produkcji należało doprecyzować założenia koncepcyjne, wykonać projekt i uzgodnić dokumentację techniczno-projektową w jednostce UDT. Uzgodnienia te są zawsze przeprowadzane w oparciu o wymagania zawarte w Rozporządzeniu Ministra Gospodarki z dnia 16 kwietnia 2002 r. w sprawie warunków technicznych dozoru technicznego, jakim powinny odpowiadać zbiorniki bezciśnieniowe i niskociśnieniowe przeznaczone do magazynowania materiałów trujących lub żrących oraz w normie DVS 2205.
Weryfikacji podlega wtedy nie tylko dokumentacja, ale także kwalifikacje, udział w dedykowanych szkoleniach i certyfikaty osób realizujących produkcję zbiornika, a także zakres stosowanych do niej materiałów. W przypadku inwestycji w zbiorniki dozorowe, szczególnie wtedy, gdy Inwestorowi zależy na szybkim czasie realizacji należy pamiętać, że każde zmiany będą wymagały ponownych uzgodnień. To dlatego niezwykle ważne jest, by już na wstępie posiadać rzetelne dane. Dzięki temu można ograniczyć czas niezbędny na przebieg procedur.
Po uzgodnieniach z UDT i otrzymaniu sprawozdania mogliśmy przystąpić do produkcji zbiorników według projektów. Po ich wytworzeniu zostały one poddane próbom kontroli jakości po stronie Amargo – jako producenta – i przy udziale inspektorów Urzędu Dozoru Technicznego. Pozytywne wyniki prób pozwoliły na trwałe ocechowanie zbiorników i przypisanie im indywidualnych numerów seryjnych. Wówczas przygotowano także tzw. paszporty zbiorników.
Zbiorniki dozorowe UDT na substancje żrące – jak zapewnić odporność chemiczną?
Zbiorniki magazynowe dozorowe wyprodukowaliśmy jako konstrukcje bezciśnieniowe z czarnego polietylenu PE100 metodą AmargTank ClassicWeld® z gotowych arkuszy tworzywa. Płyty zostały sformatowane na pile, następnie zgrzane na zgrzewarce doczołowej do płyt, tworząc cylindry. Podłogi oraz dach połączono z płaszczami cylindrów za pomocą spawu ekstruzyjnego. Zastosowany materiał PE100 jest surowcem stosunkowo często stosowanym do produkcji zbiorników magazynowych na media niebezpieczne i agresywne. Wysoka odporność chemiczna certyfikowanego tworzywa oraz szczelna i hermetyczna konstrukcja zapewnią bezpieczne i właściwe magazynowanie substancji.
Każdy ze zbiorników o pojemności całkowitej 21,1 m3 jest przeznaczony do magazynowania NaOH o gęstości 1,52 g/cm3 i stężeniu < 50% oraz HCl o gęstości 1,20 g/cm3 w stężeniu 33-38% przez okres nie dłuższy niż zaprojektowane 20 lat żywotności zbiornika (przy zapewnieniu przechowywania w określonych w dokumentacji parametrach roboczych, m.in. maksymalnej roboczej temperatury czynników roboczych (dla NaOH 30°C, dla HCl 20°C)).
Zbiornik na NaOH został posadowiony wewnątrz pomieszczenia, z kolei zbiornik na HCl – na zewnątrz, pod zadaszoną wiatą. Zbiorniki zostały wyposażone we włazy rewizyjne oraz niezbędne króćce, które są dedykowane pod kątem napełniania, odpowietrzania, poboru ze zbiorników oraz do montażu czujników przepełnienia, poziomowskazów suchych (linowych) oraz sond radarowych poziomu.
Dodatkowo wśród wyposażenia magazynów chemii znalazły się m.in. szafy AKiP umożliwiające sterowanie pracą pompy załadunkowej czynnika roboczego oraz kontrolę stanu napełnienia zbiorników.
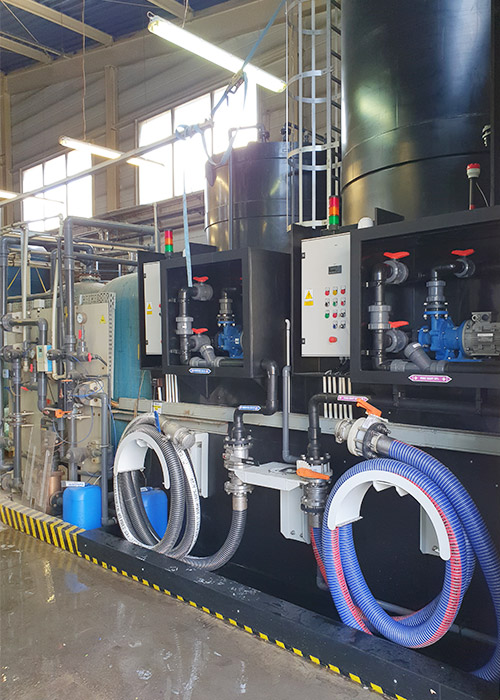
Widok na instalację wewnątrz budynku – zbiornik magazynowy NaOH oraz stacje rozładunkowe obu zbiorników
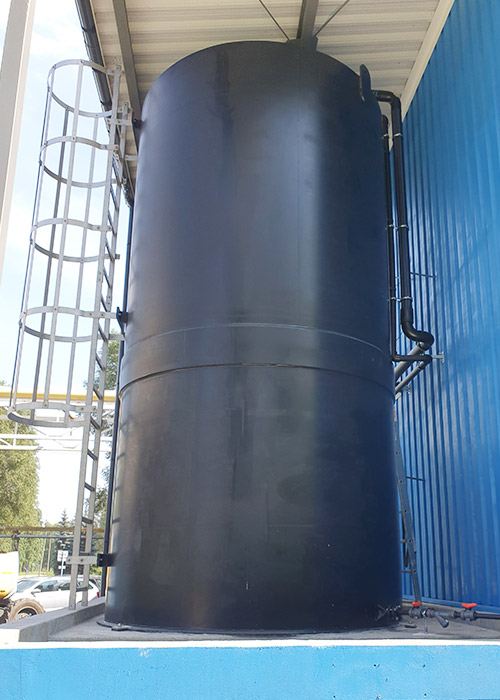
Widok na zbiornik magazynowy HCl znajdujący się na zewnątrz budynku pod zadaszoną wiatą
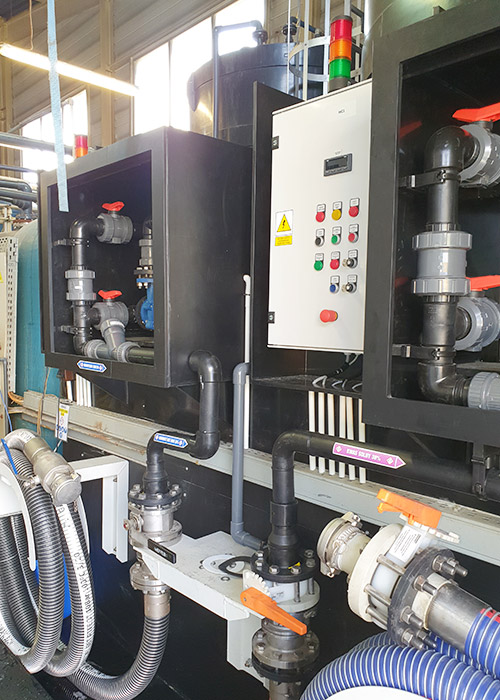
Widok na układy rozładunku substancji żrących do zbiorników dozorowych
Wyposażamy zbiorniki dozorowe UDT we wskaźniki jakości spoin
Z uwagi na to, że zbiorniki na NaOH i HCl podlegają pod dozór UDT, mając określony okres żywotności podlegają wedle Rozporządzenia Ministra Gospodarki z dnia 16 kwietnia 2002 roku w sprawie warunków technicznych dozoru technicznego, jakim powinny odpowiadać zbiorniki bezciśnieniowe i niskociśnieniowe przeznaczone do magazynowania materiałów trujących lub żrących okresowym badaniom rewizyjnym.
W przypadku zbiorników wykonanych z tworzyw sztucznych i materiałów kompozytowych rewizja wewnętrzna oraz próba szczelności powinny być wykonywane nie rzadziej niż co 10 lat, natomiast rewizja zewnętrzna nie rzadziej niż co 2 lata.
Zbiorniki do przechowywania agresywnej chemii wyposażyliśmy we wskaźniki jakości spoin (po 2 wskaźniki na każdy zbiornik). Zostały one wykonane z takiego samego materiału jak zbiorniki, czyli z PE100, jako płyty przyspawane do dna w części roboczej zbiornika. Podczas wykonywania rewizji wewnętrznej w trakcie okresu eksploatacji (czyli według rozporządzenia po 10 latach) oraz po jego zakończeniu, możliwe będzie odcięcie wskaźnika w wyznaczonym na projekcie miejscu, w celu przesłania próbki do dalszego badania laboratoryjnego. Badania takie pomogą ocenić przydatność zbiornika, połączeń spajanych oraz materiału, z którego wykonany jest zbiornik, do ewentualnego przedłużenia okresu eksploatacji.
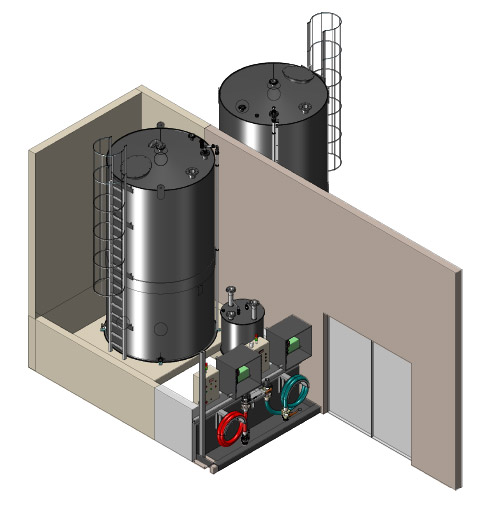
Wizualizacja instalacji magazynowania – widok od wewnątrz budynku na zbiornik NaOH, absorber oparów HCL oraz stacje NO
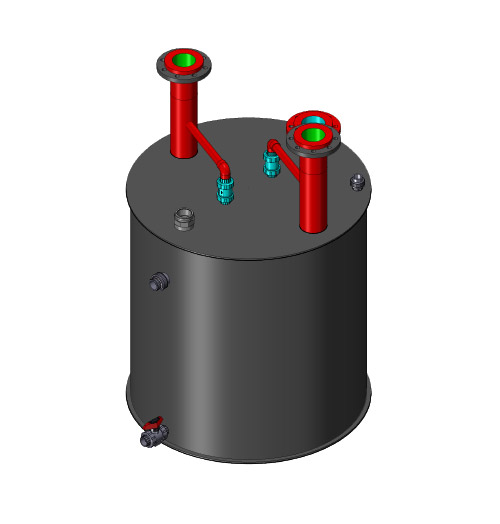
Tworzywowy absorber oparów kwasu solnego HCl (płuczka wodna)
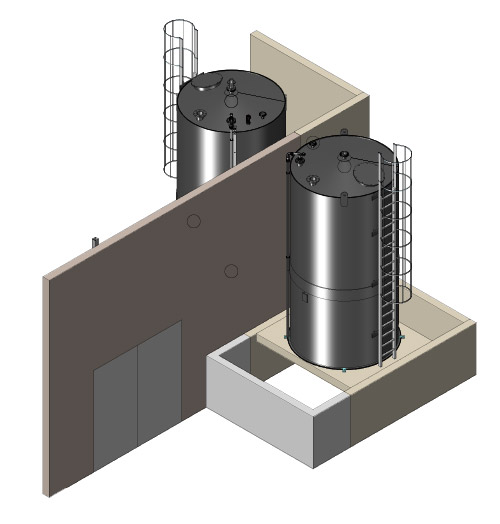
Wizualizacja instalacji magazynowania – widok od zewnątrz budynku na zbiornik HCl posadowiony na fundamencie, pod zadaszoną wiatą
Eliminacja zagrożeń związanych z użytkowaniem kwasu chlorowodorowego HCl – budowa polietylenowego absorbera oparów
Kwas chlorowodorowy HCl (kwas solny) jest jednym z najważniejszych kwasów w przemyśle. Jest on wykorzystywany m.in. do oczyszczania powierzchni metali. Z uwagi na to, że pary chlorowodoru są niebezpieczne dla człowieka, należy eliminować zagrożenia, jakie wiążą się z użytkowaniem przemysłowym tego kwasu, szczególnie podczas napełniania zbiornika.
W przypadku zbiorników na kwas solny można zastosować różne opcje, w zależności od gabarytu zbiornika i intensywności użytkowania:
- absorber ze złożem sorpcyjnym (absorbery na króćcu zbiornika),
- płuczkę wodną (tzw. zamknięcie hydrauliczne) – opary kwasu solnego poprzez duże ilości małych otworów przechodzą przez wodę i następuje neutralizacja na mokro. Woda zależnie od wersji absorbera wymieniana jest automatycznie (w sposób ciągły podczas działania, według pomiaru stężenie) lub manualnie,
- duże absorbery – płuczki z wypełnieniem złożem w postaci przestrzennych pierścieni, z wentylatorem, natryskiwaniem przeciwprądowo wody.
W ramach omawianej inwestycji zaprojektowano i wykonano absorber oparów (płuczkę wodną) HCl o stężeniu < 38% o pojemności całkowitej 0,55 m3, przeznaczony do odprowadzania oparów kwasu solnego pochodzących z dozorowego zbiornika magazynowego. Absorber w kształcie cylindra został wyprodukowany z czarnych płyt polietylenu PE100 w technologii AmargTank ClassicWeld®. Polietylenową podłogę oraz dach połączono z płaszczem cylindra za pomocą spawu ekstruzyjnego. Zastosowane w konstrukcji absorbera tworzywo jest odporne na korozyjne działanie szkodliwych oparów i zapewni jego długotrwałe użytkowanie.
Absorber został wyposażony w:
- czujnik przepełnienia/właściwego poziomu wody w absorberze,
- zawór kulowy elektryczny uzupełniania wody w absorberze sterowany poprzez szafę AKiP zbiornika magazynowego HCl.
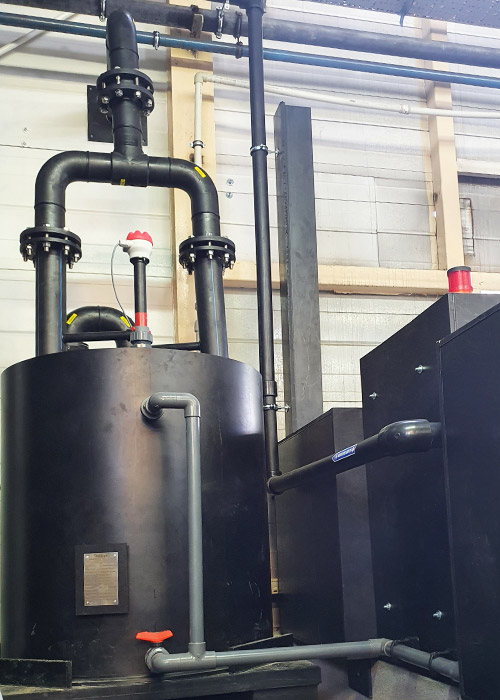
Absorber oparów żrącego kwasu solnego HCl wykonany z PE100 (płuczka wodna)
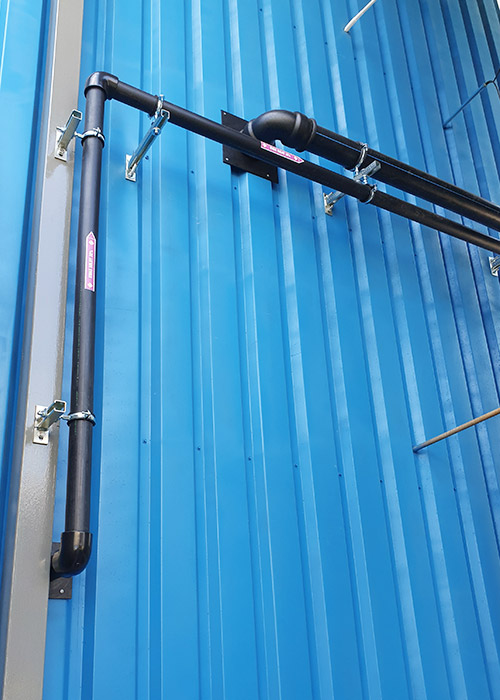
Widok na rurociąg z tworzywa zasilający zbiornik dozorowy HCL oraz na rurociąg wylotu oparów kwasu do absorbera
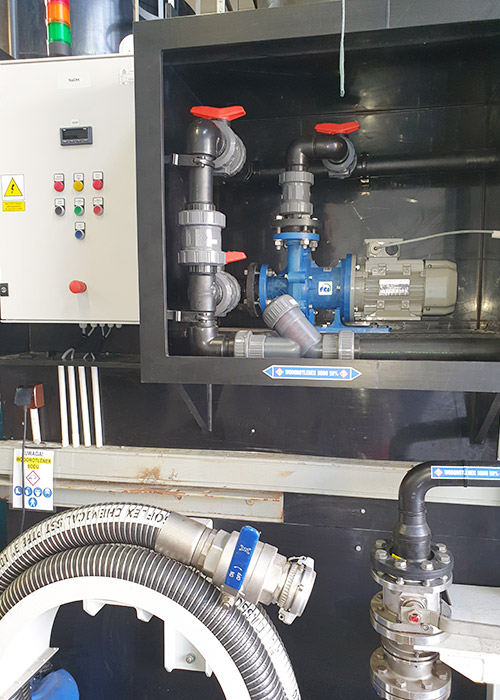
Szafa rozładunkowa jednoprzedziałowa z PE100 do rozładunku kwasu z pompą sterowaną przez szafę AKiP
Przemysłowa instalacja rozładunku – stanowiska NO kwasu solnego i wodorotlenku sodu
Instalacja magazynowa została wyposażona w stanowiska rozładunku kwasu solnego 33-38% oraz NaOH 50% z cystern samochodowych (dwa urządzenia NO wykonane na bazie elastycznych przewodów przeładunkowych, każde wyposażone w złącza awaryjnego rozłączania, które w sytuacji, gdy cysterna zacznie odjeżdżać od stanowiska rozłączą ją od reszty instalacji).
Na stanowisku znalazły się szafy rozładunkowe jednoprzedziałowe przeznaczone do rozładunku czynników roboczych z autocysterny. Elementy szaf zostały wykonane z PE100 (poza przednią szybą z poliwęglanu transparentnego). Każda z szaf została wyposażona w dno w kształcie wanny na skropliny oraz króciec odpływowy wraz z zaworem kulowym PVC.
W skład każdego układu rozładunkowego wchodzi elektryczna pompa rozładunkowa sterowana poprzez szafę AKiP danego zbiornika magazynowego. Instalacja daje możliwość rozładunku autocysterny poprzez pompę elektryczną, jak również jest wyposażona w układ umożliwiający rozładunek poprzez sprężarkę na wyposażeniu autocysterny.
Projekt urządzeń napełniająco-opróżniających UNO podlegał uzgodnieniu i zgłoszeniu w Transportowym Dozorze Technicznym (TDT).
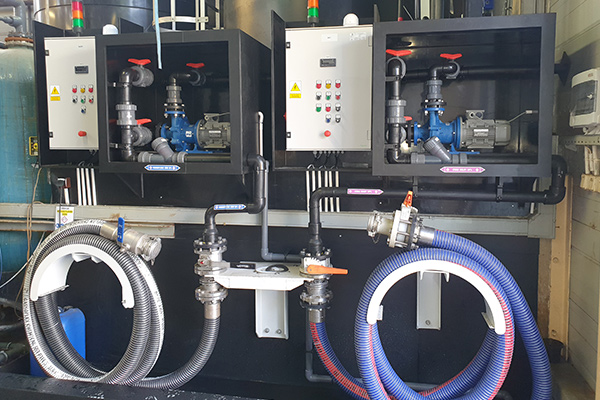
Widok na stanowiska rozładunkowe NaOH i HCl z układem rozładunku pompą elektryczną lub układem rozładunku sprężarka na wyposażeniu autocysterny
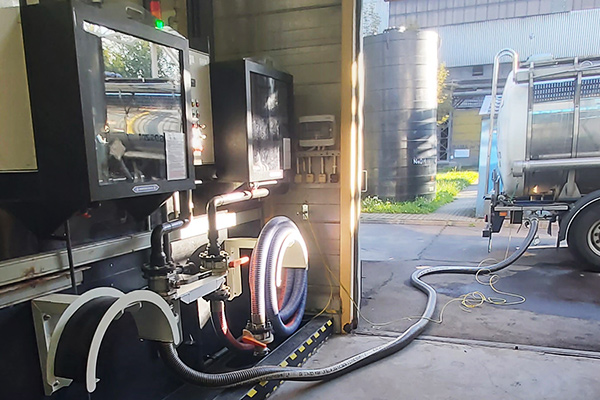
Rozładunek NaOH do zbiornika bezciśnieniowego z polietylenu PE100 stacja NO zbiorników
Jakie korzyści dzięki inwestycji w nowe zbiorniki dozorowe zyskało przedsiębiorstwo?
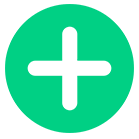
Oszczędności związane z naprawami
Naprawy zbiorników bez świadomości ukończonego okresu żywotności byłyby nieracjonalne ekonomiczne (wykonanie badań rewizyjnych byłoby utrudnione) – Klient zyskał nowe zbiorniki przeznaczone do pracy przez kolejnych 20 lat, wyposażone we wskaźniki jakości spoin, które ułatwią badania rewizyjne UDT
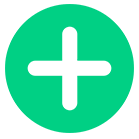
Zachowanie ciągłości produkcji
Nowe zbiorniki dozorowe wyposażone w stacje rozładunku z automatyką pozwolą zapewnić ciągłość i niezawodność realizowanych procesów
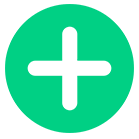
Bezpieczeństwo procesów
Zapewnienie odporności chemicznej instalacji magazynowania, wraz z rozwiązaniem pozwalającym na bezpieczne odprowadzenie szkodliwych oparów HCl
Porozmawiajmy o rozwiązaniu Twojego wyzwania
Rozmowa to klucz do sukcesu. Skorzystaj z naszej wiedzy i doświadczenia.