Izolacja zbiorników z tworzyw termoplastycznych – podstawowe informacje, które warto wiedzieć
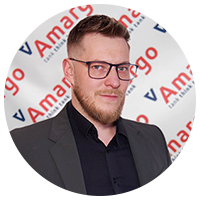
Grzegorz Zając, Ekspert z zakresu zbiorników i instalacji przemysłowych z tworzyw sztucznych
Konstrukcje zbiorników bezciśnieniowych z tworzyw termoplastycznych należy odpowiednio izolować termicznie w celu utrzymania prawidłowych właściwości fizyczno-chemicznych magazynowanego czynnika oraz zapewnienia wymaganych parametrów pracy w warunkach otoczenia, jakie panują w jego miejscu posadowienia.
Etapem poprzedzającym produkcję zbiornika bezciśnieniowego jest zawsze zebranie wyczerpujących informacji na temat warunków pracy. Te dane mają krytyczny wpływ na zastosowane materiały, przewidziane technologie wytwarzania, jak i żywotność zbiornika. W kolejnym etapie przeprowadzane są obliczenia wytrzymałościowe (inaczej obliczenia statyki) dla założonych parametrów. Izolację zbiornika dobiera się na etapie projektowania konstrukcji.
W materiale przedstawiamy najważniejsze informacje nt. izolacji naziemnych zbiorników z tworzyw termoplastycznych przed stratami ciepła oraz rozwiązań pozwalających zapewnić odpowiednią temperaturę medium.
Izolacja termiczna zbiorników wełną mineralną
W codziennej praktyce – zależnie od wyniku obliczeń strat ciepła – stosuje się wełnę mineralną o grubości 50 mm lub 100 mm. Zawsze dąży się do tego, by straty były jak najmniejsze. Ociepleniu podlega głównie cylinder (ściany zbiornika), który ze względu na największą powierzchnię konstrukcji oddaje najwięcej ciepła, jak również jego dach. Dla zbiorników zewnętrznych, które pracują w warunkach, w których mogą występować temperatury skrajne np. –20°C ociepla się także dno. Izolowane powinny być szczególnie konstrukcje z polipropylenu PP lub PVC – materiału bardziej kruchego i podatnego na uszkodzenia w przypadkach spadków temperatury. W niektórych przypadkach izolacją obejmuje się także rurociągi przesyłowe transportujące medium ze zbiornika na dalszą część instalacji.
Wyliczając grubość wełny mineralnej do izolacji zbiornika może się okazać, że zastosowanie 100 mm materiału będzie wiązało się ze stosunkowo niewielkim kosztem, ale pozwoli uzyskać zdecydowanie lepszą izolacyjność i oszczędzić energię potrzebą do podgrzewania medium.
W przypadku zastosowania wełny mineralnej mamy do czynienia z tzw. konstrukcją dwupłaszczową zbiornika. Od wewnątrz znajduje się cylinder właściwy, następnie montowana jest izolacja i całość „zamyka się” płaszczem ochronnym. Płaszcz zewnętrzny może być wykonany zarówno z płyty polietylenowej PE, polipropylenowej PP czy blachy aluminiowej – wszystko w zależności od potrzeb Inwestora.
W przypadku zbiorników magazynowych podlegających pod dozór Urzędu Dozoru Technicznego UDT wyposażonych w wannę wychwytową, ocieplenie stosuje się na zbiornik główny przechowujący medium, nie na wannę.
W ostatnim czasie w Amargo przeprowadzono interesujące analizy pod kątem konstrukcji zbiornika o średnicy 4 m, wysokości 13 m (pojemność rzędu 150 m3), produkowanego metodą nawojową. Do założeń przyjęto, że wewnątrz zbiornika należy zapewnić temperaturę 50°C, natomiast na zewnątrz – okresowo może się pojawiać –20°C. Okazało się, że w takim przypadku w przekroju ścianki występują miejsca, gdzie spada temperatura, co niekorzystnie wpływa na tworzywo. Skutkiem tego będzie ryzyko występowania naprężeń wewnątrzmateriałowych. Dla takich założeń należy więc zwrócić uwagę na ocieplenie także dna zbiornika. Tego typu naprężenia w płycie dennej zbiornika w dłuższej perspektywie czasu mogłyby powodować pęknięcia (tworzywo mogłoby „wariować w swojej strukturze”) i awarie. Do ocieplenia dna zbiornika należy w takich przypadkach zastosować materiał odporny na ściskanie, np. styrodur.
Montaż wełny mineralnej na zbiorniku
Wełnę mineralną do izolowania zbiornika z tworzywa sztucznego montuje się na kilka sposobów:
- Wykonanie konstrukcji wsporczej wokół zbiornika, która będzie podtrzymywała materiał izolacyjny. Rozwiązanie stosuje się zwłaszcza dla wysokich zbiorników (np. rzędu 8 m). Dodatkowo jako elementy pośrednie montuje się bednarki, które utrzymują wełnę na poszczególnych wysokościach zbiornika. Stanowią one podparcia dla materiału izolacyjnego, który pod wpływem ciężaru mógłby się zgniatać.
- Stosowanie wełny mineralnej połączonej z jednostronną okładziną z siatki galwanizowanej przyszytej galwanizowanym drutem do warstwy wełny, która nadaje jej sztywność. W takim przypadku nie potrzebne są elementy do wspierania materiału. W zależności od wielkości zbiornika montuje się listwy z tworzywa do których zamocowany jest cienki drucik połączony z wełną. Dzięki temu izolacja pozostanie na swoim miejscu i nie przemieści się niezależnie od manewrowania zbiornikiem podczas transportu czy posadowienia.
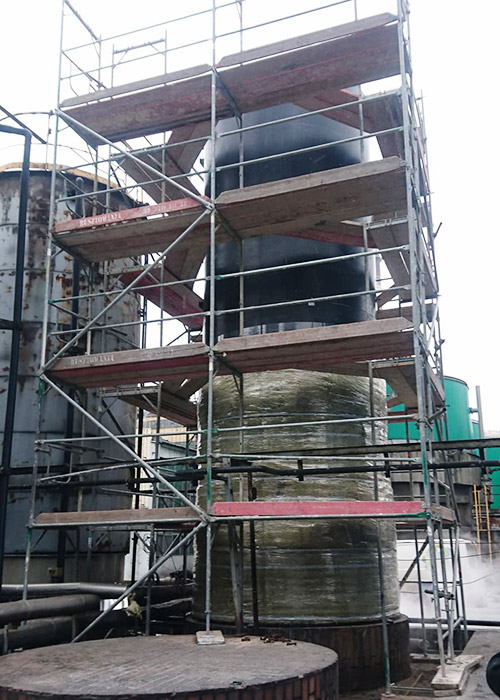
Montaż wełny mineralnej na posadowionym zbiorniku NaOH, na którym dodatkowo zostanie zamontowana obudowa z blachy aluminiowej
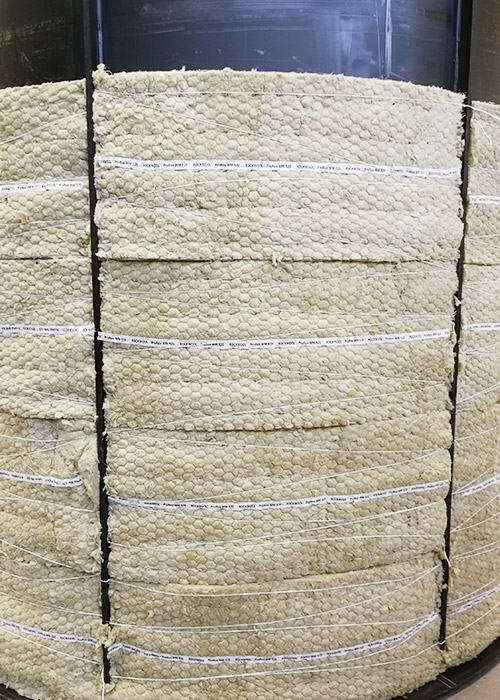
Montaż izolacji na zbiorniku magazynowym – wełna mineralna połączona z jednostronną okładziną z siatki galwanizowanej
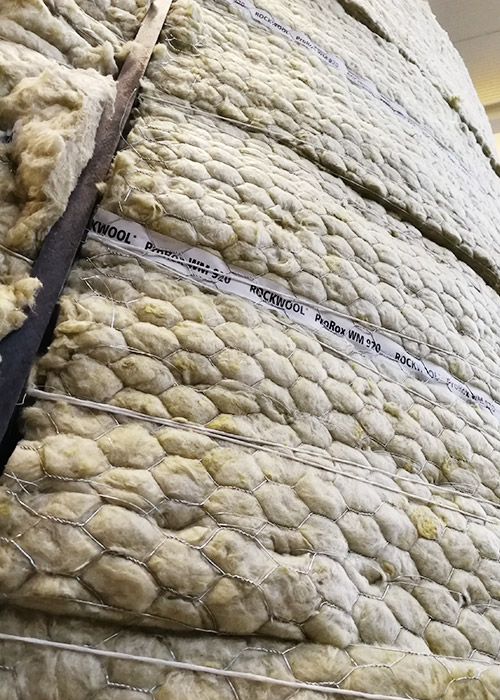
Widok w przybliżeniu na wełnę z siatką galwanizowaną, która nadaje materiałowi izolacyjnemu sztywność
Ocieplenie zbiornika pianką natryskową PUR
Pomimo że najczęściej stosowanym materiałem do izolacji zbiorników z tworzyw sztucznych jest wełna mineralna, warto w tym miejscu wspomnieć o możliwości ocieplenia za pomocą pianki natryskowej PUR. O ile montaż wełny jest realizowany samodzielnie przez ekipę producenta, o tyle w przypadku pianki PUR na ogół zachodzi konieczność zaangażowania firmy zewnętrznej, dodatkowych zabezpieczeń na hali i przycinania powierzchni z pianki. W chwili obecnej jest to rzadko stosowane rozwiązanie.
Dodatkowa instalacja grzewcza dla zbiorników z tworzyw sztucznych
Warto podkreślić, że wełna mineralna wystarczy przed uniknięciem strat ciepła, ale nie ochroni niektórych czynników roboczych przed utratą właściwości fizyczno-chemicznych, co może w znaczący sposób przysporzyć problemów w realizowanym procesie produkcyjnym. W przypadku, gdy w zbiorniku zewnętrznym znajduje się np. woda, prawdopodobnie zajdzie konieczność zastosowania instalacji grzewczej w postaci kabli (1, 2 lub 3 obwody). W codziennej praktyce nazywa się ją „instalacją grzejną +5°C”. Takie rozwiązanie stosuje się także w sytuacjach, w których temperatura medium nie może spaść poniżej określonej temperatury np. 20°C (np. ług sodowy o stężeniu 50%).
W całej analizie funkcja ogrzewania zbiornika jest wynikowa. Po drodze należy odpowiedzieć sobie na pytania nie tylko w zakresie warunków posadowienia zbiornika, ale także warunków pracy. Ważną kwestią jest to, w jakiej temperaturze będzie dostarczane medium, a jaka ma być docelowa temperatura medium w zbiorniku.
Dla przykładu w warunkach zimowych dostarczane medium może być nieco wychłodzone i mieć temperaturę np. 30°C, a wedle procesu wymagane jest, by „normalnie” było to 50°C. Wtedy mówimy o dogrzewaniu czynnika roboczego. Jeśli nawet taka substancja zostanie przywieziona w temperaturze 50°C, to należy przeanalizować (głównie w kontekście zbiornika magazynowego), ile czasu medium będzie przebywało w zbiorniku zanim zostanie zużyte. Jeśli będzie to np. okres 1 miesiąca, to występuje ryzyko, że może ono stracić swoją temperaturę. Wtedy – analogicznie jak we wcześniejszych przykładach – należy przeanalizować jakie mogą być straty ciepła w ciągu 1 miesiąca. Jeśli będą zbyt duże – należy uwzględnić dodatkową izolację i zweryfikować możliwe straty. W sytuacjach, gdy nadal będą one wysokie, stosuje się elementy grzejne. Ich główną funkcją jest utrzymanie zadanej temperatury oraz dogrzanie medium w przypadku przywiezienia go w niższej temperaturze.
Znając wspomniane informacje możliwy będzie dobór elementów grzejnych i ich mocy (może być wystarczająca np. grzałka 2 kW, 3 kW, 6kW.
Jeden z Inwestorów posiada zbiornik magazynowy ługu sodowego, który z uwagi na posadowienie zewnętrzne jest narażony na minusowe temperatury. W opinii przedsiębiorstwa rurociągi transportujące medium ze zbiornika na instalację o długości 50 m były zbyt mało ocieplone. W celu wyeliminowania zagrożenia krystalizacją płynącego rurociągiem ługu i zapewnienia odpowiedniej temperatury na końcu drogi przesyłu, zamierzano podnieść temperaturę w zbiorniku. W naszej ocenie bardziej racjonalne aniżeli sztuczne podbijanie temperatury w zbiorniku byłoby zastosowanie układu ogrzewania rurociągów, co zaproponowaliśmy Inwestorowi.
Przewody grzewcze montuje się do zbiornika spiralnie za pomocą samoprzylepnej taśmy aluminiowej. Pomiar temperatury zachodzi na płaszczu zbiornika. Sterowanie układem grzewczym jest realizowane poprzez stycznik za pomocą termostatu elektronicznego. Układ sterujący jest wyposażony w dodatkowy termostat mechaniczny ograniczający temperaturę instalacji do zadanej temperatury granicznej.
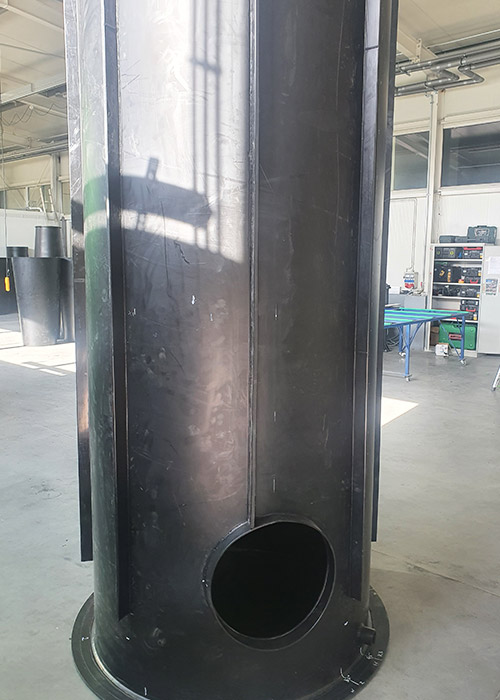
Konstrukcja zbiornika magazynowego z listwami z tworzywa przygotowana do montażu instalacji grzewczej elektrycznej oraz izolacji termicznej wełną mineralną
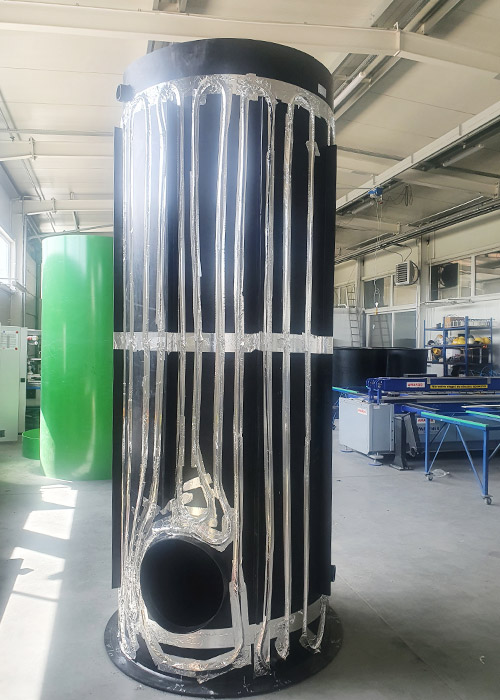
Montaż instalacji ogrzewania elektrycznego kablem grzewczym za pomocą samoprzylepnej taśmy aluminiowej na zbiorniku z tworzywa sztucznego

Widok na zbiornik od drugiej strony – przewody grzewcze mocowane spiralnie na cylindrze (płaszczu) zbiornika
Instalacja grzewcza w środku zbiornika w rurkach PEX
Inną z możliwości jest zastosowanie długiej, zwiniętej rurki PEX, w której umieszczony jest kabel grzejny. Rurkę wprowadza się do wnętrza zbiornika, natomiast jej obydwa końce wyprowadza się przez dach. Zaletą rozwiązania jest to, że jeśli instalacja ulegnie po latach uszkodzeniu, do jej naprawy (wymiany) nie ma potrzeby ingerowania w konstrukcję zbiornika.
Jeśli wymiana przewodu nie będzie trwała zbyt długo (zazwyczaj jest to maksymalnie 1 godzina, a nie kilka dni), to nie ma potrzeby opróżniania zbiornika, a medium nie zdąży wystygnąć. To wyraźna zaleta w odróżnieniu do grzałki zamontowanej na stałe na dnie zbiornika. Do jej wymiany należy wówczas opróżnić zbiornik, zneutralizować, wejść do środka, odkręcić / zdemontować zniszczoną grzałkę i zamontować nową (czasami stosuje się też grzałki na lince chemoodpornej).
W przypadku, gdy przewody ułożone są na ścianie zewnętrznej zbiornika, pod izolacją np. z wełny, do naprawy zbiornik należy „rozebrać” z ocieplenia, zdemontować kable i założyć nowe.
Warto podkreślić, że zastosowanie instalacji grzewczej w środku zbiornika w rurkach PEX jest możliwe głównie dla zbiorników magazynowych. Rozwiązanie nie dotyczy zbiorników procesowych, w których wnętrzu znajduje się np. mieszadło.
Systemy redundantne jako dobra praktyka
Dobrą praktyką zapewniającą ciągłość procesu jest wyposażenie zbiorników magazynowych w systemy redundantne (zdublowane). Dzięki temu zwiększone jest bezpieczeństwo układu ogrzewania. W sytuacji, gdy jeden z nich ulegnie awarii, drugi pracuje ograniczając przestoje produkcyjne. Dodatkowe zastosowanie systemu sterowania w razie usterki wywoła alarm w obrębie zbiornika oraz w miejscu, w którym przebywają osoby odpowiedzialne za kontrolę pracy układu.
Okresowe przeglądy izolacji termicznej zbiornika oraz instalacji ogrzewania rurociągów
Na koniec warto wspomnieć o przeglądach instalacji ogrzewania zbiornika w okresie jesiennym oraz wiosennym, które mogą obejmować swoim zakresem:
- sprawdzenie poprawności połączeń,
- sprawdzenie układu sterowania,
- sprawdzenie stanu aparatury łączeniowej,
- pomiar stanu izolacji dla obwodów,
- sprawdzenie kamerą termowizyjną (wychwycenie słabych punktów izolacji np. wskutek wycieków),
- pomiary prądów przewodów grzewczych,
- drobne naprawy materiałowe (np. wymiana zacisku, listwy, dławika),
- kontrolę stanu izolacji i ewentualne drobne naprawy.
Właściwe podejście do kwestii izolacji termicznej naziemnych zbiorników z tworzyw termoplastycznych pozwala zachować stabilność procesów produkcyjnych i bez wątpienia wpływa na bezpieczeństwo oraz żywotność układu. Warto zatem dokładnie przeanalizować proces i dobrać takie rozwiązania z zakresu izolacji, które będą ekonomiczne i pozwolą zapewnić odpowiednie parametry pracy zbiornika.
Porozmawiajmy o rozwiązaniu Twojego wyzwania
Rozmowa to klucz do sukcesu. Skorzystaj z naszej wiedzy i doświadczenia.