Magazynowanie stężonego kwasu siarkowego H2SO4 (VI) w wielkogabarytowych zbiornikach z tworzywa
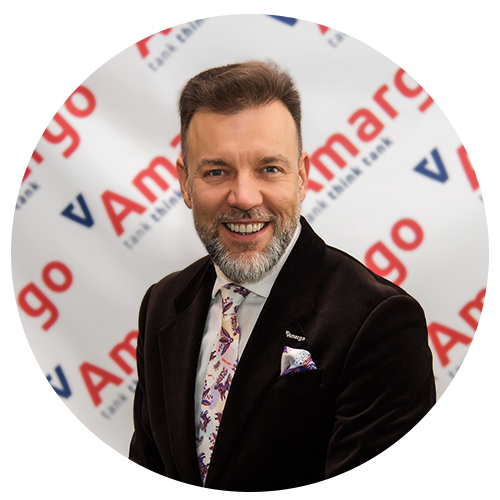
Autor: Szczepan Gorbacz, Prezes Zarządu Amargo
Ekspert z zakresu zbiorników i instalacji z tworzyw sztucznych
W niniejszym artykule poruszamy zagadnienia dotyczące przemysłowych, wielkogabarytowych chemoodpornych układów zbiorników tworzywowych oraz instalacji przeznaczonych do pracy ze związkami żrącymi takimi jak np. kwas siarkowy czy kwas azotowy i inne substancje o właściwościach silnie utleniających, które często wywołują efekt wyraźnych spękań naprężeniowych w zgrzewach lub spoinach arkuszy płyt zbiornika, z których został zbudowany.
Dla wyjaśnienia i rozpoczynając nieco od historii oraz tradycji w zakresie projektowania oraz doboru materiałów i rozwiązań w zakresie magazynowania kwasu siarkowego o wysokim stężeniu (tj. rzędu 96-98%), jak również częstych warunkach pracy w podwyższonej temperaturze – należy zaznaczyć, iż przez długie lata powszechnie wybieranym materiałem w tym zakresie była stal węglowa, w tym z różnymi technologiami pokrycia powierzchni ścian oraz dna w celu ograniczenia ryzyka korozji.
Wspomniane technologie polegające na gumowaniu / malowaniu nie dawały jednak zadowalających efektów i wymagały dość częstych interwencji oraz napraw, co na ogół jest bardzo kłopotliwe i kosztowne. Wiąże się to po pierwsze z koniecznością zatrzymania pracy zbiornika oraz instalacji (wymierne straty finansowe przedsiębiorstwa przemysłowego) oraz po drugie – z bardzo wymagającym przygotowaniem wnętrza zbiornika, tak by zapewnić bezpieczną pracę ekipom remontowym – mamy tu na myśli neutralizację atmosfery, zapewnienie specjalistycznej wentylacji, automaty oddechowe i szereg innych środków ochrony bezpośredniej. Warto także podkreślić, że remont czy też naprawa zbiornika poprzez nałożenie warstwy chemoodpornej, która to musi zostać trwale połączona z podłożem poprzez przyklejenie / zespolenie, wymaga spełnienia nadzwyczaj wysokich wymagań tj. bardzo dużej czystości podłoża, równości oraz eliminacji ubytków, odtłuszczenia, odrdzewiania.
Jeśli wzmiankowo mielibyśmy poruszyć kwestię odporności innych specjalistycznych gatunków stali na kwas siarkowy – możemy przywołać opracowania: C.M. Schillmoller, Selection and performance of stainless steels and other nickel-bearing alloys in sulphuric acid, Nickel Institute NiDi Technical series, No. 10 057, www.nickelinstitute.org oraz Guide to corrosion-resistant nickel alloys, Haynes International, Inc., H-2114b, www.haynesintl.com, uwzględnione także w publikacji na portalu stalenierdzewne.pl.
Dane uwzględnione w przytoczonych materiałach potwierdzają, iż wykonanie zbiornika z zaawansowanych specjalistycznych odmian stali jest bardzo kosztowne i nadal nie daje całkowitej odporności oraz długoletniej żywotności magazynu kwasu siarkowego.
Dodatkowo, z reguły każdemu odpowiedzialnemu użytkownikowi zbiornika kwasu siarkowego zależy na tym, by warunki przechowywanego medium były zachowane na najwyższym poziomie – krótko rzecz ujmując, by parametry fizykochemiczne kwasu, w tym czystość i barwa, nie ulegały zmianom podczas magazynowania w zbiorniku. Jak wiadomo kwas siarkowy w kontakcie ze stalą wchodzi w reakcję, dotyczy to zwłaszcza tych partii zbiornika, w których dochodzi do systematycznej zmiany poziomu cieczy – odsłonięcia i narażenia powierzchni stalowej zbiornika na kontakt z atmosferą tlenową.
Powłoki antykorozyjne wewnątrz zbiornika magazynowego na kwas siarkowy
Mając na względzie czystość magazynowego kwasu oraz wymagania odbiorców medium dotyczące składu chemicznego roztworu kwasu oraz jego barwy – co jest warunkiem uzyskania podczas obrotu na rynku odpowiednio wyższej ceny, wynikającej z jakościowego surowca – część zakładów przemysłowych decyduje się na zlecenie wykonania dodatkowej powłoki antykorozyjnej wewnątrz zbiornika poprzez pokrycie wewnętrznej powierzchni stalowej wykładziną z płyt ECTFE (symbol zgodny z normą EN ISO-1043-1), jednostronnie kaszerowanych materiałem szklanym GK 2,3 mm (tworzywo fluoropolimerowe). Po wykonaniu wykładziny chemoodpornej z tworzywa sztucznego (kopolimeru etylenu i chlorotrifluoroetylen), pomimo wykonywanych testów iskrowych szczelności, inwestorzy życzą sobie wykonanie w odstępach czasowych pomiaru jakości kwasu, gdzie parametrami gwarantowanymi jest wielkość wzrostu stężeń żelaza i barwa kwasu, wynikające z magazynowania kwasu w okresie 3 miesięcy (porównanie parametrów kwasu wlewanego do zbiornika i z niego wylewanego).
Wykonanie wspomnianych cienkowarstwowych wykładzin chemoodpornych przy wykorzystaniu tworzyw z rodziny fluorowców realizowane jest w ramach uprawnień dozorowych UDT przez specjalistów Amargo, jednak w niniejszym opracowaniu skupimy się na innym unikalnym rozwiązaniu, jakie proponujemy dzięki szerokim możliwościom wdrażanej nawojowej linii produkcyjnej, wytłaczającej beznaprężeniową (NoStress) wstęgę tworzywa formowanego na dany wymiar zbiornika.
Zbiorniki magazynowe na kwas siarkowy z tworzyw termoplastycznych produkowane z gotowych płyt tworzywa
Cylindryczny chemoodporny zbiornik z tworzywa sztucznego np. polietylenu wysokiej gęstości molekularnej HDPE – klasy PE100 (wytrzymałość 10 N/mm2) można wykonać poprzez obróbkę oraz zgrzewanie lub spawanie płaskich, uprzednio ekstrudowanych arkuszy tworzywa – dostępnych handlowo na rynku. Natomiast prowadząc proces odpowiedzialnego projektowania takiego zbiornika, należy po pierwsze zweryfikować odporność chemiczną bazując na specjalistycznych katalogach i wytycznych opartych o dane producentów, które są powiązane z danymi materiału pierwotnego – granulatu użytego do wytłoczenia wspomnianych płaskich arkuszy.
Odporność chemiczna jest szczególnie ważna z uwagi na możliwe negatywne efekty w wyniku spękań naprężeniowych. Jak zaznaczono na wstępie, roztwór kwasu siarkowego H2SO4 (VI) o wysokich stężeniach, zwłaszcza w wyższych temperaturach to silny utleniacz. W efekcie, w trakcie okresu eksploatacji zbiornika medium atakuje najbardziej wrażliwe miejsca jakimi są spawy ekstruzyjne oraz zgrzewy tworzywa, szczególnie gdy są w nich skumulowane naprężenia wewnątrzmateriałowe pozostałe po procesie ekstruzji, zwijania arkuszy w cylinder, bądź formowania obszernych w przekroju spoin ekstruzyjnych. Wynika to z faktu, że podczas stygnięcia masy wyekstrudowanej, plastycznej spoiny dochodzi do skurczu materiałowego i „ściągania” sąsiednich struktur materiałowych w obszar kurczącej się masy tworzywa.
W wyniku penetracji wgłębnej medium dochodzi do zniszczeń struktury tworzywa i kolejno przechodzenia do coraz to głębszych warstw materiału. Proces oczywiście postępuje w czasie z odpowiednim zmniejszeniem intensywności, jednak jeśli sumaryczna grubość materiału nie zapewnia odpowiedniego naddatku gwarantującego przeniesienie wytrzymałości nawet przez część przekroju ścianki (ciągle niezdegradowaną) – wówczas zbiornik może ulec uszkodzeniu i przeciekowi.
Mówiąc o odporności chemicznej użytego gatunku tworzywa do budowy zbiornika magazynowego kwasu siarkowego należy także wskazać, iż wykonując obliczenia uwzględnia się adekwatne współczynniki, zawarte w ww. tabelach.
Reasumując – przy zachowaniu reżimu projektowego, wytycznych DVS w zakresie możliwych akceptowalnych naprężeń w strukturach tworzywa (tabela „Permissible edge fibre elongation according to DVS 2205 Part 2) często okazuje się, iż zwykłą technologią zgrzewania tworzywa nie można wykonać zbiornika na omawiany kwas z zapewnieniem długoletniej, bezawaryjnej żywotności. Doskonałą alternatywą są zbiorniki magazynowe wytwarzane metodą nawojową (szerzej pisaliśmy o niej w artykule „Produkcja innowacyjnych zbiorników z tworzyw termoplastycznych metodą nawojową – co przemysł na niej zyska?”).
Technologia nawojowa AmargTank SafeSeamLess® jako sprawdzona metoda wytwarzania zbiorników na silnie żrące substancje
Mając na względzie powyższe i jednocześnie zapewniając bezpieczne funkcjonowanie zbiornika, stosujemy technologię produkcji w pełni chemoodpornych zbiorników dozorowych UDT (oraz niepodlegających UDT – technologicznych/procesowych) na tzw. „ciężką chemię” systemem ciągłej beznaprężeniowej ekstruzji płaszcza zbiornika, dającą możliwość wykonania pełnej litej ścianki o grubości przekroju rzędu nawet 180 milimetrów.
Co dzięki technologii nawojowej może zyskać użytkownik zbiornika kwasu siarkowego
- Oszczędności kosztów inwestycyjnych oraz w zakresie wydatków remontowych dzięki możliwości wydłużenia czasu eksploatacji zbiornika w wyniku zastosowania bezpiecznych grubości ścianki tworzywa (odpowiednik naddatku na korozję stosowany powszechnie podczas projektowania zbiorników stalowych, gdzie czasami sięga 30 – 50% nominału).
- Wzrost rentowności bieżącej działalności produkcyjnej dzięki uzyskiwaniu podczas obrotu wysokiej ceny kwasu; jest to możliwe dzięki zachowaniu nieskazitelnej czystości magazynowanego roztworu kwasu, gdyż do budowy zbiornika nie używa się ani grama stali, w efekcie nie ma możliwości, by związek wchodził w reakcję i tracił swe pierwotne parametry jakościowe.
- Eliminację kosztów utrzymania ruchu – nie ma potrzeby wykonywania na zewnątrz zbiornika jakichkolwiek specjalistycznych powłok czy też barier antykorozyjnych i ich odtwarzania w cyklach 2-3 letnich, gdyż stosowane w Amargo do produkcji mieszanki tworzyw charakteryzują się dużą odpornością na żrące chemikalia, korozję atmosferyczną, promieniowanie UV i zmienne warunki otoczenia, co skutkuje wymiernymi oszczędnościami podczas wieloletniej eksploatacji zbiorników.
- Bezpieczeństwo użytkowania i zachowanie ciągłości produkcji, na co wpływa homogeniczność materiału w całym przekroju (dla typu jednomateriałowego tworzywa) oraz brak naprężeń strukturalnych ścianki, a w efekcie brak uszkodzeń i pęknięć – czyli nie dochodzi do rozszczelnień i awarii systemu, dlatego też przerwy remontowe i zatrzymania ciągów produkcyjnych należą do rzadkości.
- Znaczną izolacyjność cieplną zbiornika – nawet przy braku stosowania dodatkowych warstw izolacyjnych, gdyż stosowany jako budulec zbiornika materiał (tworzywo z grupy termoplastów) odznacza się małym przewodnictwem cieplnym (współczynnik przewodzenia ciepła np. dla PE-HWU wynosi λ = 0,38 W/m·K), co w efekcie zapewnia dobrą izolację własną struktury ściany zbiornika AmargTANK, brak lub znikome przenikanie ciepła do / ze zbiornika, a finalnie brak potrzeb stosowania izolacji o znacznych grubościach.
- Oszczędność kosztów transportu, manipulacji, dźwigów, montażu, podbudowy, wynikająca z ograniczenia potrzebnych nakładów – zwyczajnie zbiorniki Amargo w porównaniu do innych technologii, w tym bazujących na produkcji z metali, charakteryzują się kilku do nawet kilkunastokrotnie mniejszą masą własną konstrukcji przy znacznej sztywności i wytrzymałości, w efekcie czego łatwy transport i montaż to wymierna odczuwalna już na starcie inwestycji oszczędność kosztów.
- Możliwość stosunkowo łatwej i elastycznej zmiany konfiguracji zbiornika w przyszłości, w tym chociażby położenia czy też ilości oraz średnic króćców – tworzywo termoplastyczne to przyjazny i łatwy w obróbce materiał, podczas spawania/zgrzewania króćców nie dochodzi do uszkodzenia warstwy chemoodpornej, co może mieć miejsce przy zbiornikach metalowych – tu zwyczajnie cały przekrój jest warstwą chemoodporną, a stosowane narzędzia i technologie często porównywane są do obróbki drewna.
Porozmawiajmy o rozwiązaniu Twojego wyzwania
Rozmowa to klucz do sukcesu. Skorzystaj z naszej wiedzy i doświadczenia.