Ocena możliwości wydłużenia okresu żywotności zbiorników z tworzyw sztucznych
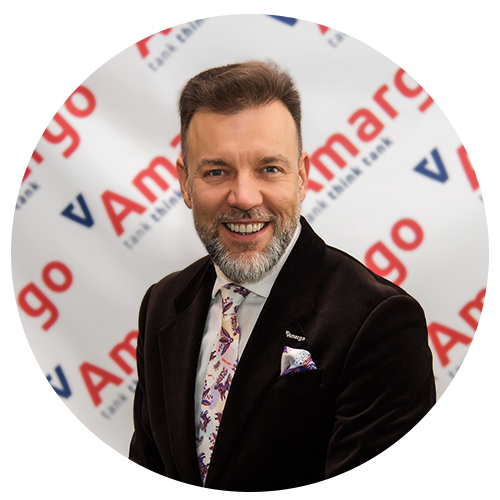
Autor: Szczepan Gorbacz, Prezes Zarządu Amargo
Ekspert z zakresu zbiorników i instalacji z tworzyw sztucznych
Konsultacja merytoryczna: Leszek Lewandowski, Ekspert niezależny ds. Tworzyw Sztucznych
Pracownik Urzędu Dozoru Technicznego w latach 1984–2023 UDT Oddział w Bydgoszczy
W dzisiejszych czasach – postępującego rozwoju i nowych technologii, a jednocześnie dbania o otaczające nas środowisko naturalne – niebezpieczne związki chemiczne, w tym te toksyczne, silnie żrące, trujące oraz inne materiały szkodliwe, występują powszechnie w większości branż zakładów przemysłowych.
Mowa tu nie tylko o zakładach stricte chemicznych, ale również z sektora spożywczego, przetwórczego, papierniczego, a także o praktycznie wszystkich stacjach uzdatniania wody oraz oczyszczalniach ścieków. W artykule stanowiącym początek serii przedstawione zostaną kwestie wymagań prawnych i technicznych, przeglądów oraz oceny stanu technicznego – zarówno te istniejące, jak i nowe, innowacyjne, które są stopniowo wdrażane.
Działania kierowane są na ciągłą poprawę bezpieczeństwa technicznego, co dotyczy nie tylko życia i zdrowia człowieka, ale też ochrony środowiska i mienia.
Zastosowanie zbiorników z tworzyw sztucznych
Najbardziej powszechnymi substancjami chemicznymi, które do bezpiecznego i zgodnego z przepisami [1] magazynowania wymagają dedykowanych chemoodpornych zbiorników podlegających pod dozór Urzędu Dozoru Technicznego, wraz z systemem zabezpieczeń przed wyciekiem w razie awarii, są: kwas solny, kwas siarkowy, ług sodowy, podchloryn sodu oraz koagulanty typu PIX / PAX (siarczany, chlorki żelaza i glinu).
Wymienione związki są stosowane zwłaszcza w procesach demineralizacji wody, czy też po prostu uzdatniania oraz zobojętniania i oczyszczania ścieków komunalnych oraz przemysłowych. To pokazuje, jak obszerna jest grupa zastosowań, a tym samym ilość zbiorników bezciśnieniowych i niskociśnieniowych z tworzyw sztucznych, podlegających dozorowi technicznemu. Jest to bardzo rozległy sektor.
Warto podkreślić, iż zgodnie z tabelą 2 [2], będącą załącznikiem do ww. rozporządzenia, formą dozoru ograniczonego objęte są już zbiorniki o pojemności od 60 l do 1000 l dla czynnika roboczego zaklasyfikowanego jako toksyczny lub bardzo toksyczny, a dla pojemności powyżej 1 m3 tej samej kategorii związków jest to forma dozoru technicznego pełnego. Zgodnie z wymienioną tabelą wszystkie zbiorniki powyżej pojemności 5 m3 (dla każdej kategorii związku) podlegają pełnemu dozorowi technicznemu.
Rewizje okresowe wynikające z przepisów
Zbiorniki podlegające dozorowi technicznemu wymagają okresowych rewizji – zewnętrznych i wewnętrznych, a ich częstotliwość opisuje tabela 1 załącznika rozporządzenia [3]. Dla zbiorników wykonanych z chemoodpornych tworzyw sztucznych (HDPE 100, PP-H / PP-C, PVDF, PVC) i materiałów kompozytowych (z warstwą chemoodporną z dedykowanej żywicy lub z wysoce chemoodpornym linerem z tworzywa) maksymalny okres między rewizjami zewnętrznymi określono na 2 lata, z kolei rewizje wewnętrzne należy wykonywać minimum raz na 10 lat.
Warto podkreślić, iż należy bezwzględnie wymagać od projektanta oraz wytwórcy zbiornika, by w ramach uzgadnianej z UDT dokumentacji wykazali wymaganą odporność chemiczną materiałów użytych do wytworzenia zbiornika, zwłaszcza warstw chemoodpornych mających mieć bezpośredni kontakt z przechowywanym medium.
W przypadku zbiorników kompozytowych bez chemoodpornej warstwy w postaci linera z tworzywa termoplastycznego (PE, PP, PVC-U, PVC-C, PVDF, itd.), a jedynie z warstwą żywicy i welonem szklanym (by zawartość włókna szklanego w tej powłoce była minimalna), nie ma możliwości, by okresy między rewizjami wynosiły aż 10 lat. Zapisy normy EN 13121 [4] wskazują w zależności od agresywności związku na konieczność inspekcji technicznej wewnętrznej warstwy antykorozyjnej (bariery chemicznej) po 3 i 5
latach, a kolejno co rok.
Regularne inspekcje wewnętrzne oraz badania stanu technicznego magazynowych zbiorników z tworzyw sztucznych podlegających dozorowi technicznemu, niezależnie od materiałów użytych do ich wytworzenia, są obligatoryjne i wskazane do wykonania z większą częstotliwością. Wszystko po to, by zapewnić bezpieczną eksploatację, ograniczyć ryzyko awarii i rozszczelnienia, a także magazynować substancje żrące, trujące i niebezpieczne w zgodzie z najlepszymi możliwymi standardami panującymi na rynku oraz dobrą praktyką inżynierską. Leży to w interesie właścicieli zbiorników i infrastruktury technicznej zakładów, służb utrzymania ruchu, służb interwencyjnych i jednostek ratownictwa, takich jak np. straż pożarna, a także inspektorów Urzędu Dozoru Technicznego, stanowiących niejako osoby zaufania publicznego i wzór dobrych praktyk dla przedsiębiorstw oraz firm ubezpieczających.
Kolejną istotną sprawą, poza rewizjami wewnętrznymi, jest żywotność zbiornika określona w dokumentacji projektowej (obliczeniowej statyki zbiornika). Podczas planowania rewizji należy w pierwszym kroku bezwzględnie przeanalizować dokumentację projektową danego zbiornika, gdyż zapisy mówiące o założonej żywotności nie są przenoszone do aktualnie używanych dokumentów zgłoszeń zbiorników, paszportów czy też ksiąg rewizyjnych. Żywotność zbiornika lub aparatu sprawdzamy w uzgodnionej przez UDT dokumentacji projektowo-obliczeniowej, która poprzedzała etap wytwarzania.
Przykład
Jeśli żywotność została przez projektanta lub wytwórcę przyjęta jako 10 lat, to de facto po tym okresie zbiornik powinien zostać wycofany całkowicie z eksploatacji. Ewentualne odstępstwa od tej reguły poruszono w dalszej części artykułu.
Bezpieczne wydłużenie okresu żywotności zbiornika
Co i w jaki sposób jest oceniane podczas rewizji wewnętrznej zbiornika zbudowanego z tworzywa sztucznego, np. polietylenu PE-HD? Jakie parametry są analizowane? Jakie kryteria i poziomy oceny jakości uznawane są za akceptowalne i dające podstawy dopuszczenia do dalszej eksploatacji?
Dotyczy to rewizji wewnętrznych, tak zwanych pośrednich, ale również jeszcze bardziej odpowiedzialnych badań rewizyjnych, które mają być podstawą do ewentualnych rozważań tego, czy i na jaki okres możliwe jest wydłużenie użytkowania zbiornika, gdy pierwotnie założony w dokumentacji czas pracy uległ zakończeniu.
Zauważalny jest trend, iż o możliwość wydłużenia cyklu użytkowania zbiorników dozorowych starają się zwłaszcza użytkownicy zbiorników zabudowanych w ciąg instalacji technologicznych na terenie zakładów przemysłowych, gdzie wymiana z tak trudno dostępnej przestrzeni jest bardzo skomplikowana. Wiąże się ona często z wyłączeniem ruchu i pracy na wielu ciągach technologicznych oraz wymaga przykładowo otwarcia dachu w celu wydobycia dźwigiem zbiornika, który jest wciśnięty pomiędzy inne zbiorniki i rurociągi.
Temat metod i zakresu badań tworzywa, pierwotnych poziomów odniesienia i kryteriów oceny jest szczególnie istotny, tym bardziej że w zakresie stali występuje wiele wytycznych, użytecznych metod badania i oceny, dobrych praktyk i standardów, a znajomość tego materiału jest, w przeciwieństwie do tworzywa, na znacznie wyższym poziomie.
W odniesieniu do tworzyw termoplastycznych brak jest jednoznacznych wytycznych, a materiał zachowuje się i reaguje całkowicie odmiennie od tworzyw metalicznych.
Przykładem jest brak możliwości zastosowania na szerszą skalę metody emisji fali akustycznej, badań ultradźwiękowych i radiograficznych, a korozja i ubytek grubości ścianki praktycznie nie występują. Zatem ewentualność zastosowania tradycyjnych, rozpowszechnionych i znanych metod jest wykluczona, co nastręcza nie lada wyzwań, by wykonać to właściwie.
Kryteria i warunki dla wydłużenia okresu eksploatacji zbiornika
Projektując chemoodporny magazynowy zbiornik dozorowy, przyjmuje się założenia:
- Określone warunki pracy urządzenia oraz wanny wychwytującej (lub konstrukcji dwuściennej typu MultiLayer DoubleWall), na podstawie formularzy doboru, w tym opisu warunków pracy, miejsca posadowienia, parametrów medium (temperatura, stężenie, gęstość), kart charakterystyki.
- Określone minimalne poziomy naprężeń i wytrzymałości występujące w poszczególnych obszarach konstrukcji zbiornika, na podstawie charakterystyk odporności chemicznej (oraz współczynników odporności krótko i długoterminowych A2, A2l opisanych w Specyfikacji DVS, PN-EN 1778, Wytycznych DiBT Medienlisten 40), kart materiałowych (wytrzymałości, naprężeń, krzywych pełzania) wybranych do budowy zbiornika z danego tworzywa.
Powyższe założone dane mają zapewnić stabilność całej konstrukcji w w określonym czasie użytkowania.
Przykładowe podejście projektowe przedstawiono skrótowo poniżej. Zgodnie z DVS 2205-2 Dział 4.1 Strenght analyses. 4.1.2 (15) warunek obligatoryjny to przedstawiony iloraz, gdzie:
- licznik opisuje występujące naprężenia w konstrukcji zbiornika tzw. existing stress in the tank,
- mianownik – rated value of the creep rupture strenght… to wartość maksymalna dopuszczalna przy określonym czasie, odczytana dla danego użytego materiału, np. PE100 – na podstawie PE100 DVS 2205-1 (lub na podstawie własnych badań i krzywych pełzania producenta) i przy założeniu współczynnika bezpieczeństwa – safety factor 1,3 (koncepcja częściowego bezpieczeństwa – „safety partial”)
Druga metoda to określenie dopuszczalnego maksymalnego poziomu naprężeń na podstawie krzywych ekwiwalentnego poziomu naprężeń dla danego tworzywa, temperatury, okresu żywotności przy uwzględnieniu współczynników spawania i zgrzewania.
- Mając na względzie powyższe podczas rewizji okresowej, aby merytorycznie ocenić i wydać odpowiedzialną decyzję o możliwości wydłużenia okresu bezpiecznej eksploatacji, wskazanym jest, by ocenić, na ile nastąpił spadek parametrów wytrzymałościowych tworzywa względem bazowych, tj. przyjętych w obliczeniach oraz zastosowanych do budowy.
- Ponadto należy zweryfikować, czy doszło do jego nadmiernego wyeksploatowania, np. w wyniku przekroczenia warunków temperaturowych względem tych zadeklarowanych w formularzu doboru zbiornika (nadmierne naprężenia, spadek jednostkowej wytrzymałości – na jednostkę powierzchni przekroju poprzecznego ścianki cylindra – w wyniku wzrostu elastyczności materiału na skutek przekroczeń temperatur).
- W końcu należy ocenić, czy aktualne parametry są powyżej lub poniżej krzywej pełzania danego materiału, np. polietylenu wysokiej gęstości molekularnej PE-HD klasy PE 100 (10 N/mm2) / PE 100 RC (dodatkowo Resistance to Crack – odporny na powolną propagację pęknięć).
Przykładowy zakres badań
Szczegółowy zakres badań okresowych podczas rewizji zbiornika tworzywowego dla rewizji pośredniej określa inspektor UDT wykonujący inspekcję. Dotyczy to np. zbiornika po 10 latach przy żywotności do lat 20.
W przypadku badań doraźnych w ramach oceny możliwości wydłużenia okresu eksploatacji ponad ten założony przez wytwórcę w dokumentacji, kolejne kroki realizowane są na wyraźny pisemny wniosek eksploatującego zainteresowanego wydłużeniem okresu eksploatacji. Jest to realizowane przy zaangażowaniu wytwórcy zbiornika, który przygotowuje stosowną opinię załączaną do wniosku eksploatującego. Dodatkowym załącznikiem może być także program badań.
Dedykowany zespół ekspertów i specjalistów tworzyw sztucznych jednostki inspekcyjnej UDT opracowuje szczegółowy program badań i analiz.
W obu opisanych przypadkach jako pierwsza dokonywana jest ocena wizualna – jako podstawowa, stosunkowo łatwa i szybka metoda służąca identyfikacji jawnych, znacznych uszkodzeń mechanicznych, wad, pęknięć, rys czy spęcznień oraz odbarwień, zmian twardości czy zmiany kształtu. Są one efektem aktywnych mechanizmów degradacji, które od razu dyskwalifikowałyby przechodzenie do dalszych etapów.
Przykłady uszkodzeń zbiorników
Dodatkowe badania, jakie z reguły wykonuje się w celu oceny zmiany parametrów charakterystycznych tworzywa (opisanych hasłowo powyżej), są tzw. badaniami niszczącymi.
Warto podkreślić, że w stosunku do tworzyw termoplastycznych powszechnie znane metody nieniszczących badań (NDT) nie wykazują wysokiej wiarygodności oraz przydatności do oceny stopnia degradacji materiału. Dotyczy to m.in. popularnej dla stali metody ultradźwiękowej, także z zastosowaniem głowic rolkowych i urządzeń typu Omniscan. Metody te świetnie sprawdzają się do weryfikacji na etapie wytwarzania celem oceny przykładowo jawnych wad w przekroju, spoinach
czy też zgrzewach.
Badania niszczące wymagają m.in. wyłączenia zbiornika i instalacji z pracy, ustawienia rusztowań, odizolowania, pobrania próbek z danego zbiornika, np. w trzech wytypowanych miejscach, w obecności inspektora UDT i przez wykwalifikowaną firmę posiadającą uprawnienia w zakresie napraw i modernizacji zbiorników dozorowych z tworzyw termoplastycznych.
Wycięte fragmenty płaszcza lub dna zbiornika (o wymiarach przykładowo 30 × 30 cm) trafiają do Centralnego Laboratorium Dozoru Technicznego lub innego uznanego przez UDT laboratorium.
Po wykonaniu badań i opracowaniu ekspertyzy, w przypadku pozytywnych wyników należy wykonać niezbędną dokumentację naprawy, uzgodnić ją w UDT, zbiornik naprawić poprzez szczelne uzupełnienie ubytków – zaspawanie w uszkodzonych miejscach, a na koniec przeprowadzić procedury odbiorowe. Całość prac wykonuje uprawniona przez Urząd Dozoru Technicznego firma.
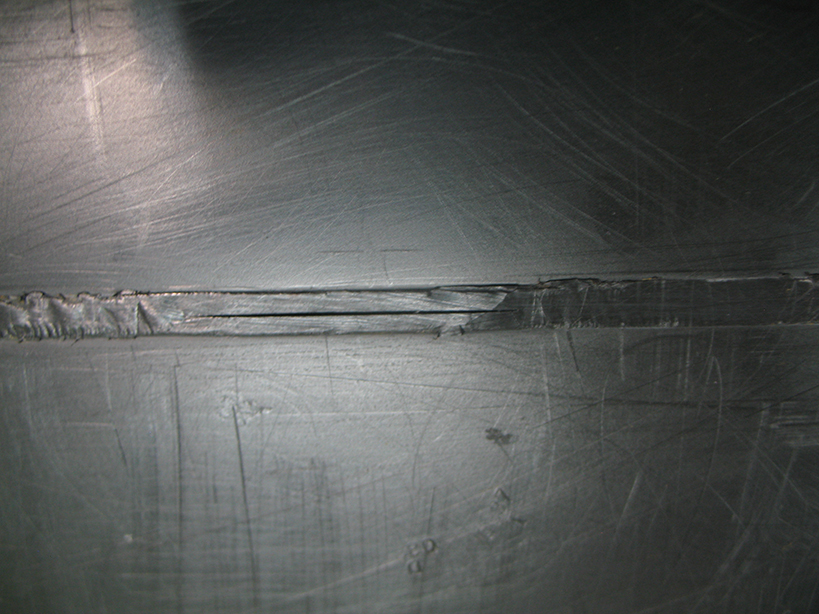
Rozszczelnienie spoiny na płaszczu zbiornika w wyniku znacznego przekroczenia termicznych parametrów pracy określonych przy projektowaniu.
Weryfikacja awarii zbiornika: widoczne rozszczelnienie spoiny
przy zabrudzeniu powierzchni skrystalizowanym ługiem sodowym.
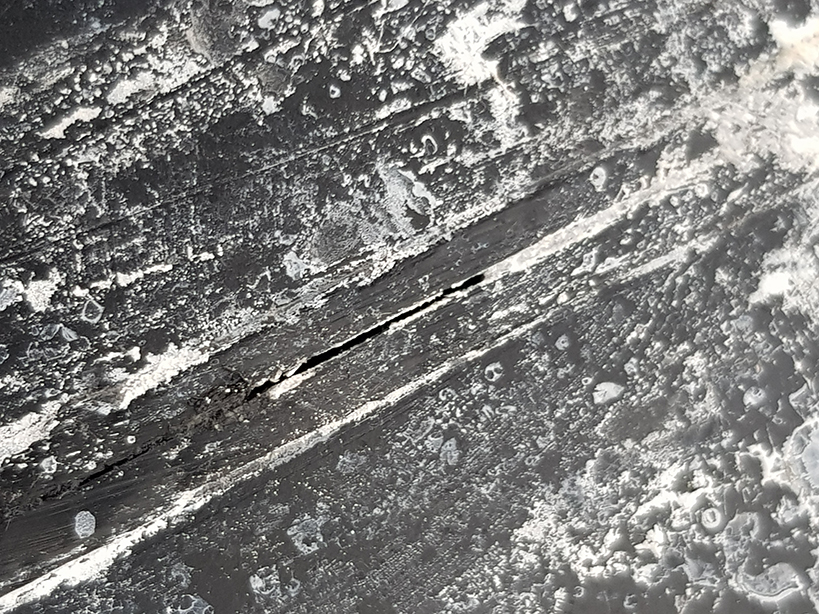
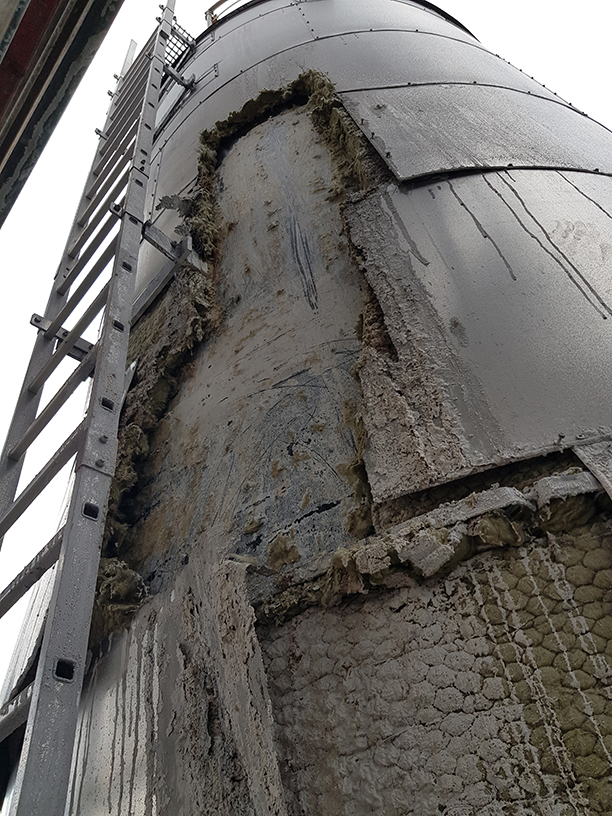
Zdjęcia korozji poszycia płaszcza aluminiowego osłaniającego izolację cieplną zbiornika magazynowego ługu sodowego na skutek pęknięcia spoiny powodującej wyciek żrącej substancji.
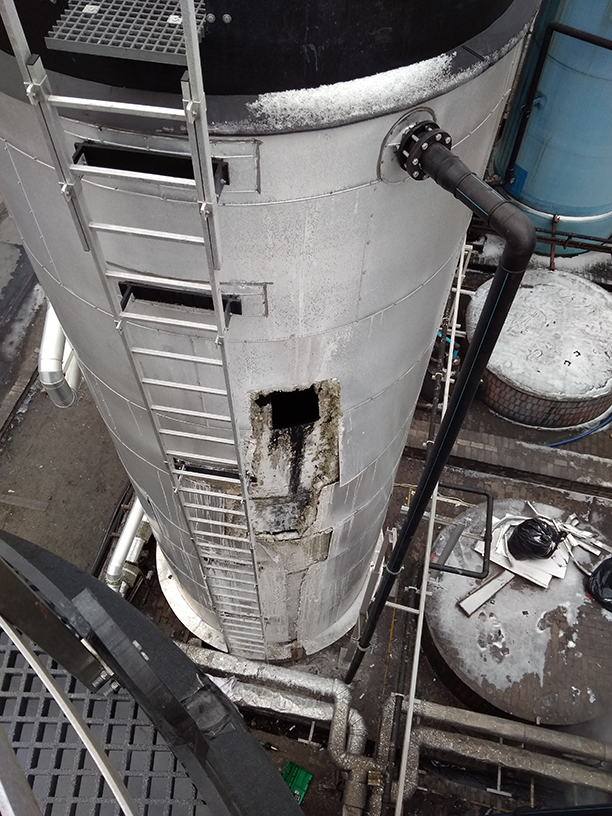
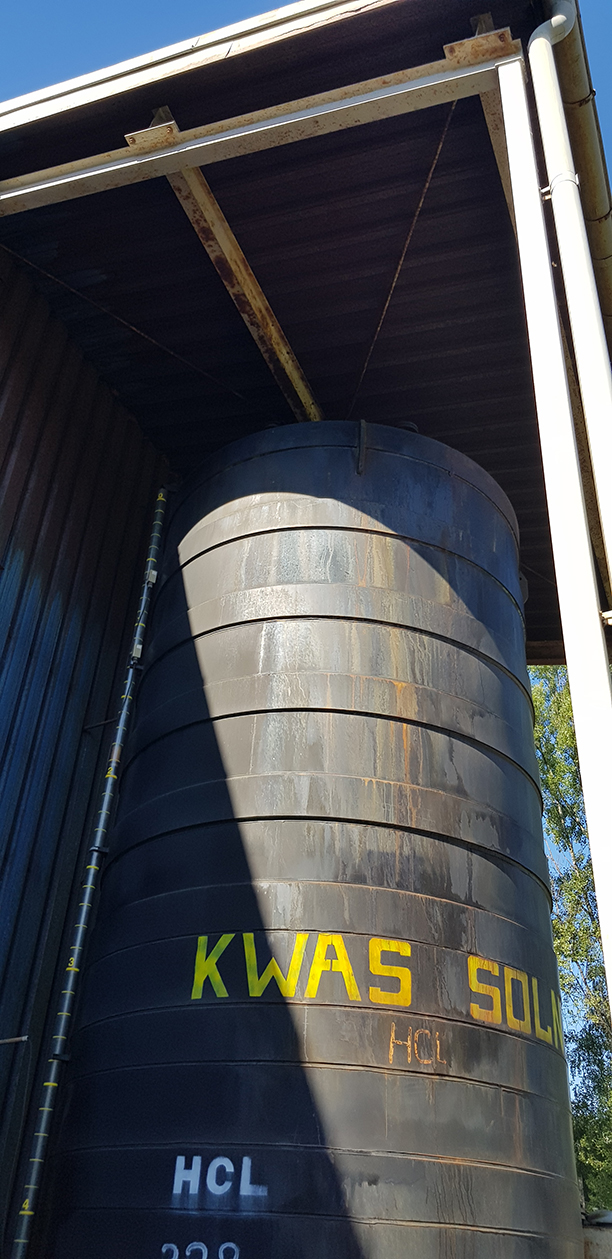
Zdjęcia wyeksploatowanego zewnętrznego polietylenowego zbiornika kwasu solnego po przekroczeniu założonego okresu żywotności, który został wymieniony na nowy; widoczne odbarwienia, naloty, deformacja kształtu w wyniku utraty pierwotnych parametrów wytrzymałościowych tworzywa.
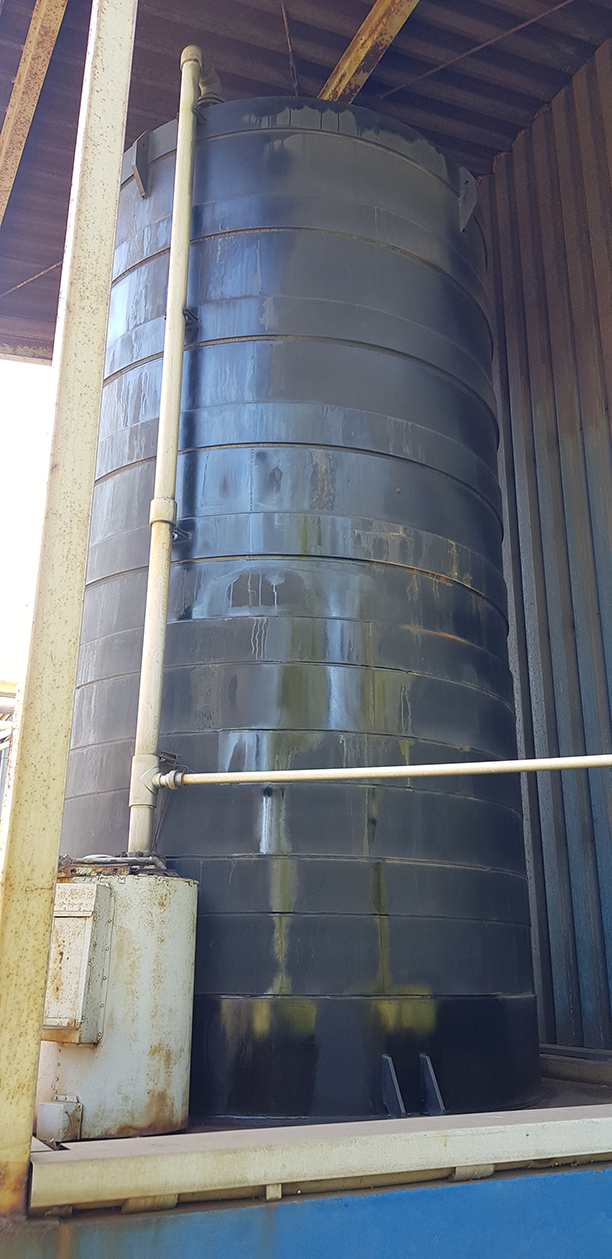
Nowe rozwiązania
Wskaźniki zamiast próbek
Opisane wyżej czynności oraz procedury są niewątpliwie czasochłonne i skomplikowane dla niewprawionego użytkownika nieznającego procedur i przepisów, a tym samym zazwyczaj dość kosztowne.
Znacznym ułatwieniem w realizacji powyższego procesu są wprowadzone kilka lat temu przez firmę Amargo unikalne elementy wskaźnikowe montowane w każdym nowo produkowanym zbiorniku dozorowym. Elementy te są wykonane z identycznego tworzywa i partii materiału jak cały zbiornik, wraz z próbkami spoin, i montowane na stałe w najniższej partii zbiornika. Dzięki temu są poddane stałej pracy z pełnym obciążeniem chemicznym.
W dalszym ciągu wprowadzamy nowe rozwiązania i udoskonalenia, których celem jest odwzorowanie w elementach wskaźnikowych występujących zmiennych obciążeń i naprężeń, identycznych jak w pobocznicy zbiornika.
Pobranie elementu wskaźnikowego
Pobranie ww. elementów wskaźnikowych nie wymaga wycinania, a tym samym dziurawienia cylindra zbiornika. Elementy są spawane do dna zbiornika, a ich pobranie wiąże się z „wyłamaniem” w odpowiednim miejscu lub przecięciem. Dzieje się to zawsze bez ingerencji w elementy konstrukcyjne zbiornika, a więc bez kłopotliwych i kosztownych prac związanych z naprawą „dziurawego” zbiornika.
Przygotowanie zbiornika do badań
Celem umożliwienia oceny wizualnej wnętrza zbiornika podczas rewizji zbiornik należy odpowiednio przygotować od strony przepisów i wymagań BHP oraz fizycznie.
Dotyczy to obu przypadków:
- fizycznego pobrania próbek (fragmentów) zbiornika,
- pobrania elementu wskaźnikowego.
Oznacza to dokładne opróżnienie, usunięcie wszelkich osadów oraz nalotów, a także wypłukanie i zneutralizowanie zbiornika. W kolejnym kroku istotna jest stała wentylacja, a przed wejściem inspektora – dokonanie pomiaru składu atmosfery wnętrza oraz zapewnienie trójnogu bezpieczeństwa, szelek, lin i oświetlenia.
Aby pozbyć się przekonań, że rewizja UDT może dezorganizować funkcjonowanie zakładu, dobrą praktyką jest dostarczenie i zmontowanie instalacji wraz ze zbiornikiem zastępczym w ramach usługi przygotowania zbiornika do badań, podczas gdy badany zbiornik i instalacja są wyłączone z ruchu. Pozwala to na niezakłóconą pracę zakładu przemysłowego.
Takie holistyczne podejście jest w dzisiejszych czasach niezwykle ważne i cenione przez użytkowników.
Precyzyjna analiza zbiornika w całym cyklu życia dzięki systemom monitoringu jako nieocenione wsparcie w podejmowaniu decyzji o wydłużeniu eksploatacji
Ciągłe monitorowanie stanu naprężeń jest szeroko stosowane w astronautyce, lotnictwie, czy energetyce jądrowej.
Zespół Amargo TANK Think Tank wraz z zewnętrznymi specjalistami z Politechniki Warszawskiej, ekspertami z zakresu metodologii MES, tj. metody elementów skończonych (ang. FEM – Final Elements Method), a także przy konsultacji i uzgodnieniu z ekspertami i specjalistami Urzędu Dozoru Technicznego, opracowuje dedykowane systemy ciągłego monitoringu zbiorników. Są one wyposażone w układ specjalistycznych czujników przeznaczonych do montażu na zbiornikach na etapie wytwarzania. Ich zadaniem jest pomiar wszystkich kluczowych parametrów przez cały okres cyklu życia zbiornika.
Niesie to za sobą możliwość podejmowania odpowiedzialnych decyzji w zakresie oceny technicznej stanu zbiornika, w tym wydłużenia okresu żywotności.
Ideą projektu jest wyeliminowanie potrzeby ingerencji w konstrukcję i wyłączania zbiornika z eksploatacji. Ma je zastąpić dokonywana przez algorytmy i aplikacje analiza odczytów z czujników zebranych na przestrzeni lat eksploatacji, a to wszystko przy równoległym, precyzyjnym rejestrowaniu warunków eksploatacji zbiornika.
Literatura:
- Rozporządzenie Ministra Gospodarki z dnia 16 kwietnia 2002 r. w sprawie warunków technicznych dozoru technicznego, jakim powinny odpowiadać zbiorniki bezciśnieniowe i niskociśnieniowe przeznaczone do magazynowania materiałów trujących lub żrących (Dz.U. z 2002 r. Nr 63, poz. 572).
- Tabela 2. Formy dozoru technicznego zależne od czynnika roboczego i pojemności zbiornika. Załącznik do Rozporządzenia Ministra Gospodarki z dnia 16 kwietnia 2002 r. (Dz.U. z 2002 r. Nr 63, poz. 572).
- Tabela 1. Częstotliwość badań okresowych. Załącznik do Rozporządzenia Ministra Gospodarki z dnia 16 kwietnia 2002 r. (Dz.U. z 2002 r. Nr 63, poz. 572).
- PN-EN 13121-3:2016-08. Naziemne zbiorniki z tworzyw sztucznych wzmocnionych włóknem szklanym – Część 3: Projektowanie i wykonanie.
Porozmawiajmy o rozwiązaniu Twojego wyzwania
Rozmowa to klucz do sukcesu. Skorzystaj z naszej wiedzy i doświadczenia.