Nowe możliwości produkcji zbiorników kompozytowych oraz zbiorników ciśnieniowych dla przemysłu
Amargo nieustannie inwestuje w rozwój zaplecza produkcyjnego. W parku maszynowym została zamontowana i uruchomiona kolejna, najnowszej generacji linia nawojowa do produkcji zbiorników chemoodpornych (także ciśnieniowych i z linerem) oraz rur kompozytowych GRP / FRP metodą nawijania ciągłego włókna (szklanego lub węglowego).
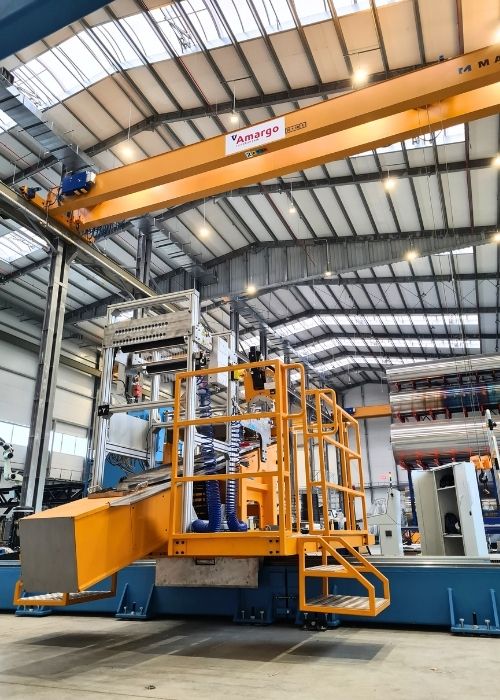
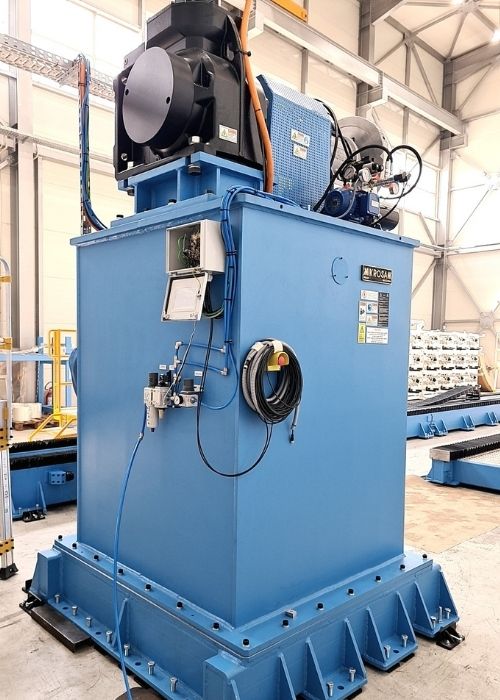
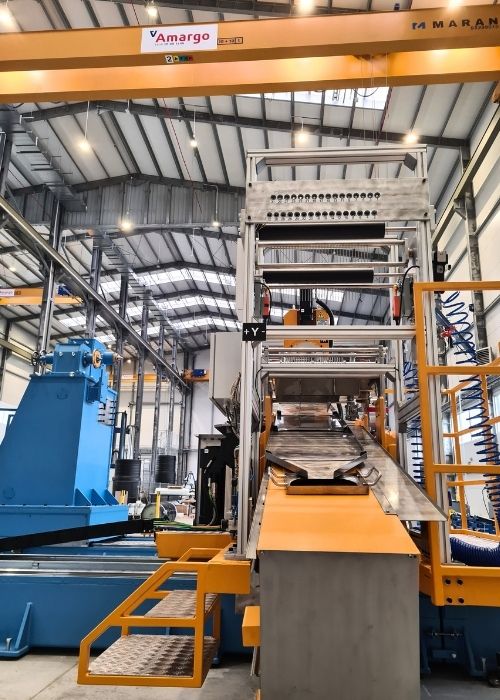
Technologia AmargTank Composite i możliwości nowej linii produkcyjnej
Nowa linia umożliwi produkcję zbiorników przemysłowych kompozytowych opartą na technologii ciągłego nawoju (rowingu).
Wykorzystując impregnację mokrą przesycania 32 wiązek włókien szklanych jednocześnie oraz cztery interpolowane osie ruchu maszyny (plus piąta opcjonalna) nowa linia produkcyjna pozwala na produkcję zbiorników kompozytowych (AmargTank Composite) w zakresie średnic od 200 mm do aż 4300 mm i długości do aż 12 000 mm (jest to maksymalny rozstaw punktów mocowania uchwytów wału napędowego / mandreli).
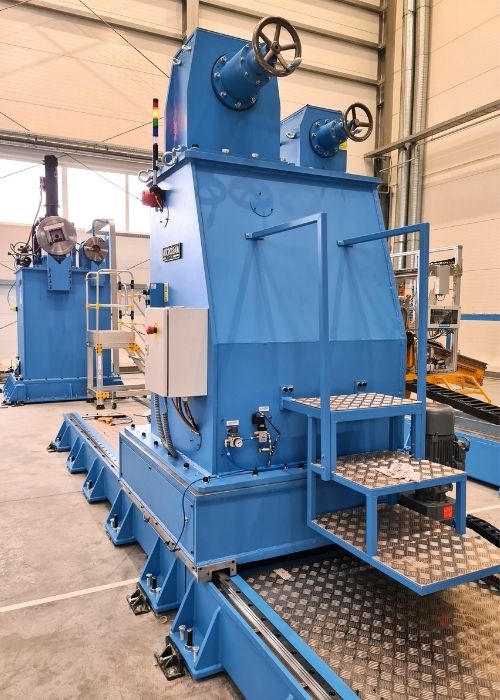
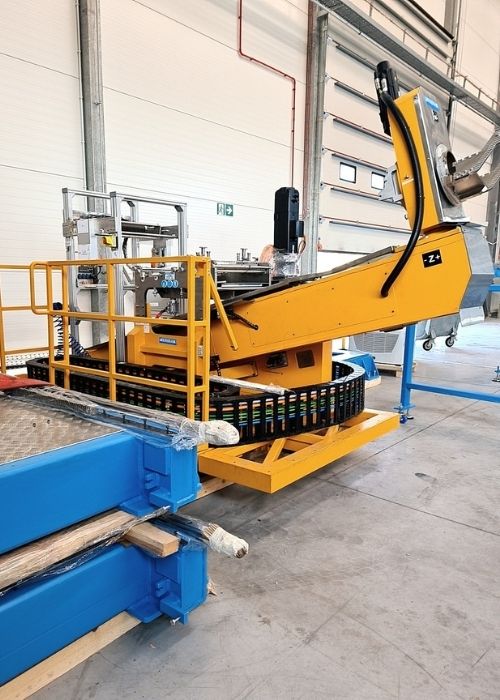
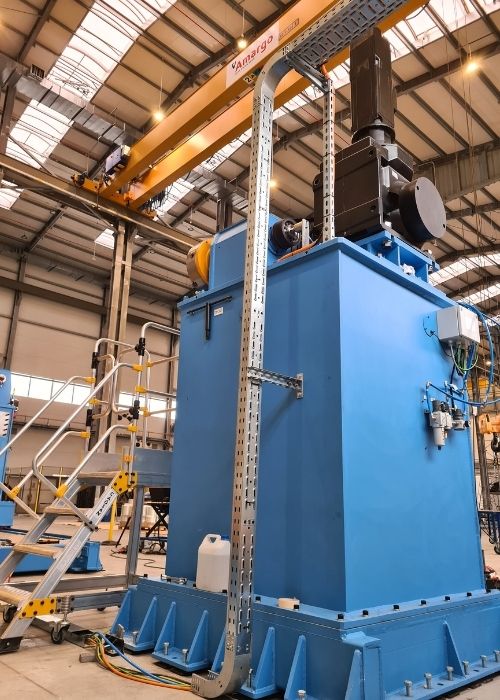
Konstrukcja wózków jezdnych i mocowań maszyny, a w szczególności precyzyjnej, a jednocześnie bardzo szybko poruszającej się głowicy układania włókna, została dobrana jako sztywna, pozbawiona wibracji czy odchyleń – stabilnie mocowana do żelbetowej posadzki hali produkcyjnej. Wszystko z uwagi na możliwy bardzo duży gabaryt produkcji zbiornika oraz jego wagę mogącą wynosić maksymalnie do 10 ton.
Kompozyty – gdy kończy się odporność termoplastów na warunki pracy
– Amargo od ponad 18 lat wspiera wiele gałęzi przemysłu, dostarczając zbiorniki chemoodporne wraz z kompletnymi instalacjami oraz niezbędnym dodatkowym wyposażeniem i układami sterowania. Gdy warunki pracy zbiornika, w tym: środowisko korozyjne, temperatura i ciśnienie, są bardzo wymagające – rozwiązania oparte na materiałach z grupy termoplastów, np. polietylenie PE100, czy polipropylenie PP-H – przestają być wystarczające. Konieczne jest wówczas zastosowanie konstrukcji zbiorników z żywic (np. vinyloestrowych / epoksyvinyloestrowych Derakane 411 – 350 Momentum, Derakane 470-300 R Momentum, Atlac 580 ACT, ARALDITE 1564 lub epoksydowych) oraz zbrojenia włóknem szklanym, najlepiej z wykorzystaniem włókien ciągłych, np. JUSHI – TEX 2400 ECR-2400-386T – mówi Szczepan Gorbacz, Prezes Zarządu Amargo.
– W celu zwiększenia odporności chemicznej ścian zbiornika stosuje się dodatkowo wysoce odporne chemicznie warstwy wewnętrzne – tzw. linery, uzyskując rozwiązania hybrydowe, znane na rynku jako „dual-laminate”. Wówczas barierę chemoodporną stanowi materiał z grupy fluorowców, taki jak PVDF, E-CTFE czy PFA. Rozwiązania oparte na konstrukcji kompozytowej z linerem charakteryzują się przede wszystkim wytrzymałością, bardzo długą żywotnością i niską wagą. To główne powody, dla których rozwiązanie znajduje przewagę nad zbiornikami stalowymi.
Z możliwości nowej linii skorzystają nie tylko zakłady i koncerny przemysłowe czy biura projektowe, ale także przedsiębiorstwa produkujące większe układy i maszyny, a chcące do kompletu zamawiać dedykowaną konstrukcję wytrzymałego zbiornika kompozytowego.
Na dostawcę nowej linii Amargo wybrało firmę Mikrosam z Macedonii, która jest uznanym na całym świecie liderem w dziedzinie maszyn i know-how dla przemysłu kompozytowego.
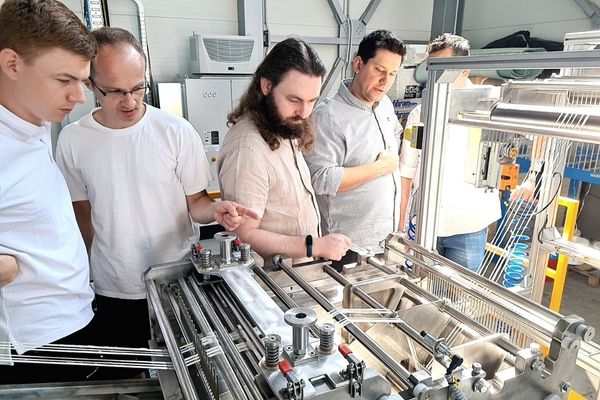
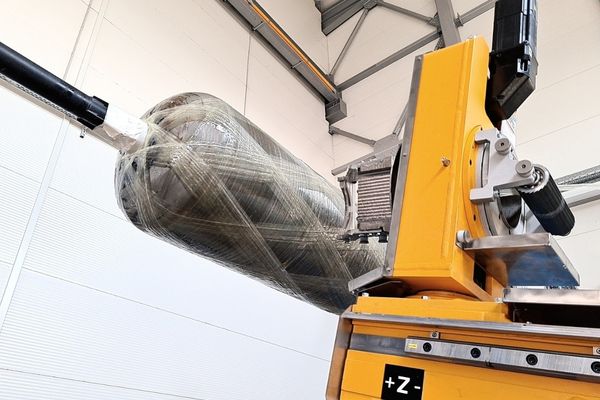
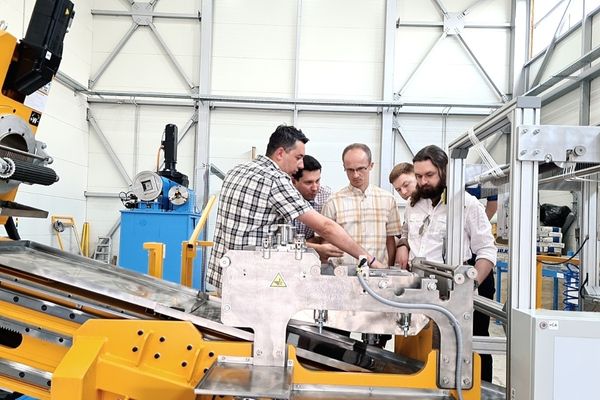
Zalety zbiorników kompozytowych przeznaczonych do pracy z agresywną chemią
Wśród praktycznych zalet zbiorników kompozytowych z nawojem z włókna szklanego lub węglowego należy wymienić:
- możliwość zaoszczędzenia ok. 50% masy przy niezmienionej objętości – konstrukcja całkowicie metalowa to masa rzędu 1,4 kg/l – natomiast zbiornika wykonanego tylko z materiałów kompozytowych – od 0,3 kg/l do 0,45 kg/l
- bardzo wysoka sztywność/wytrzymałość, którą zapewniają włókna (małą gęstość zapewnia osnowa polimerowa),
- wysoką odporność chemiczną na silnie utleniające substancje,
- w porównaniu do tworzyw standardowych możliwość pracy w wyższych temperaturach,
- możliwość stosowania linerów z tworzywa,
- możliwość wzmocnienia właściwości materiału za pomocą środków pomocniczych poprawiających właściwości mechaniczne, dielektryczne, cieplne, chemiczne lub przetwórcze,
- możliwość uzyskania większego kształtu sfery,
- w porównaniu do zbiorników o tej samej odporności, ale wykonanych ze stali nierdzewnej, koszt zbiorników kompozytowych jest znacznie niższy.
Ponadto technologia umożliwia wykorzystanie surowców mniej uciążliwych dla środowiska naturalnego i środowiska pracy, takich jak:
- żywice UV-utwardzalne (różnych typów np. Arkema Elium C595 z włoknem R25H 3B 2400 Tex),
- żywice epoxy recyklingowalne (np. EzCiclo RB240-A / BL Filament Winding marki Swancor)
- żywice poliestrowe/winyloestrowe bezstyrenowe,
- żywice epoksydowe (bezrozpuszczalnikowe),
- żywice pochodzenia naturalnego (biopochodne) lub z częściowym ich udziałem i inne surowce „BIO”.
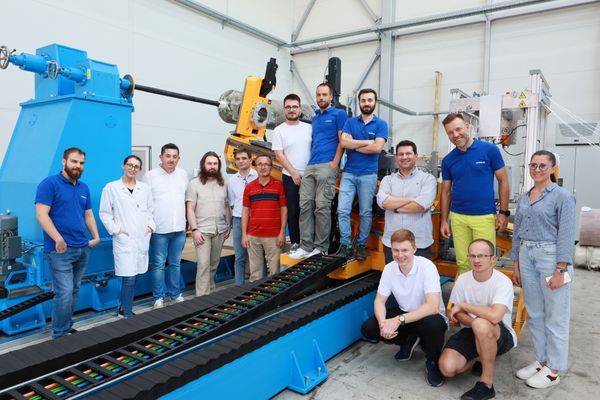
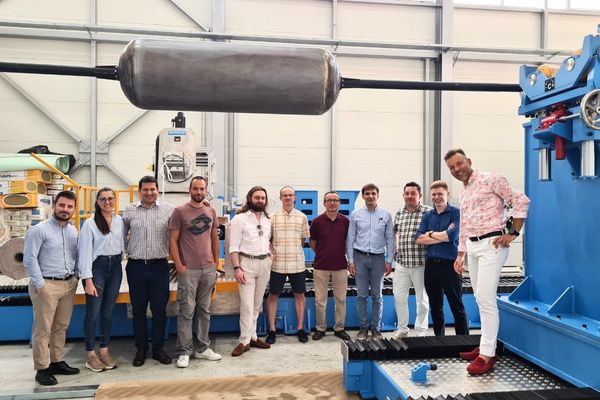
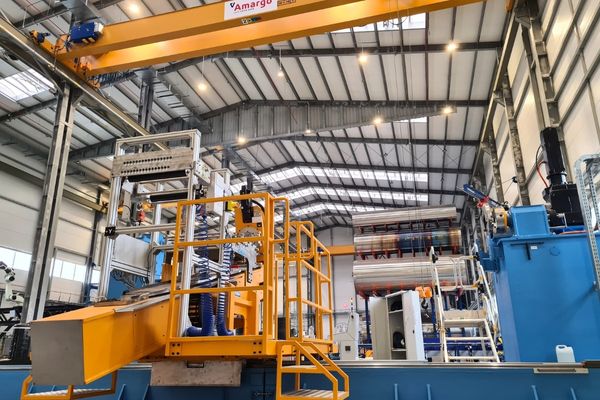
Wdrożenie nowej linii technologicznej poprzedziły spotkania, szkolenia i testy przeprowadzane wspólnie z przedstawicielami Politechniki Wrocławskiej, które odbywały się zarówno w siedzibie firmy Mikrosam – dostawcy linii oraz w zakładzie Amargo.
Rozwiązania monitorujące stan techniczny konstrukcji zbiornika przemysłowego
Chemoodporne zbiorniki ciśnieniowe zaprojektowane do przechowywania medium pod wysokim ciśnieniem mogą mieć różne kształty i rozmiary oraz być wykonane z różnych materiałów konstrukcyjnych. Ponieważ agresywne środki chemiczne przechowywane pod podwyższonym ciśnieniem mogą powodować znaczne szkody zarówno dla ludzi, jak i środowiska, konieczne jest opracowanie systemów wczesnego wykrywania uszkodzeń i monitorowania integralności strukturalnej takich zbiorników.
Rozwiązanie może również pomóc w zmniejszeniu kosztów konserwacji związanych z okresowymi inspekcjami konstrukcji (rewizjami wewnętrznymi) i nieprzewidzianymi przerwami operacyjnymi spowodowanymi niemonitorowanym rozwojem uszkodzeń, a także zmniejszyć związane z tym obciążenie dla środowiska.
Inżynierowie Amargo i naukowcy z uczelni technicznych (Politechniki Warszawskiej oraz Politechniki Wrocławskiej) opracowują specjalne systemy detekcji – czujniki, które mogą mierzyć fale sprężyste wzbudzane przez przetworniki PZT (piezoelektryczne), instalowane na zewnętrznej warstwie GFRP.
– System zapewni stałe monitorowanie stanu technicznego konstrukcji zbiornika wraz z wczesnym wykrywaniem sytuacji odbiegających od normy, co skutecznie zapobiegnie awariom i uszkodzeniom – jest to tak zwany „system konserwacji predykcyjnej”. Dodatkowo, Amargo przewiduje rozwiązania technologii Digital Twin, czyli stworzenie cyfrowego bliźniaka zbiornika, co w dobie Przemysłu 4.0 jest bardzo pożądane przez służby serwisowe i remontowe zakładów przemysłowych, szczególnie w branży chemicznej – podkreśla Szczepan Gorbacz.
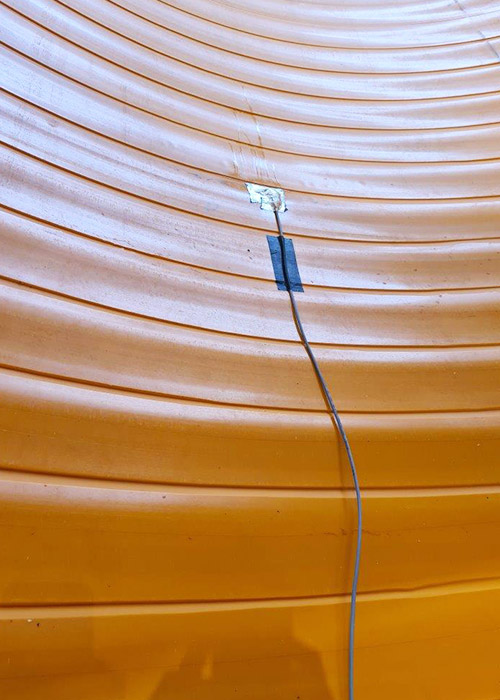
Baza wiedzy
Pełna kontrola nad zbiornikiem – czy to możliwe?
Zespół Amargo TANK Think Tank wraz z zewnętrznymi specjalistami z Politechniki Warszawskiej, Wydziału Inżynierii Materiałowej, ekspertami z zakresu metodologii MES / FEM – Final Elements Method, a także przy konsultacji i uzgodnieniu ze specjalistami Urzędu Dozoru Technicznego, opracowuje projekt dedykowanych systemów monitoringu zbiorników oraz magazynu energii.
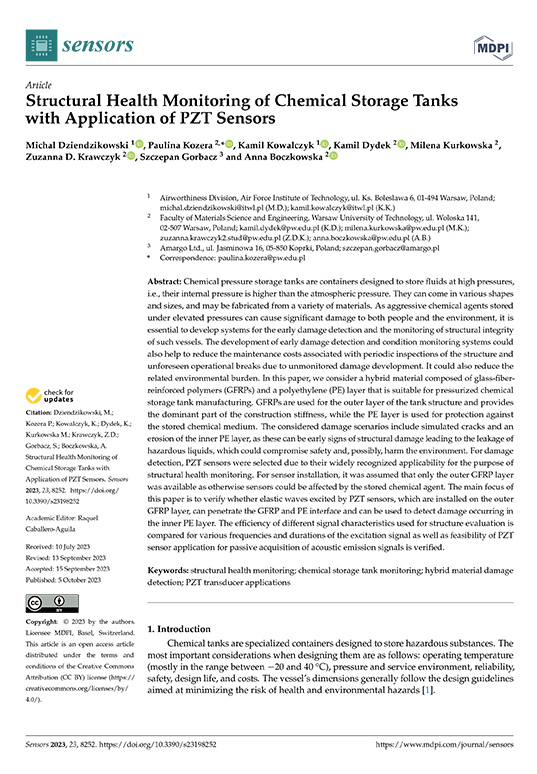
Publikacja naukowa
Amargo w awangardzie nowoczesnych rozwiązań na rynku zbiorników chemoodpornych
Zespół Amargo we współpracy z naukowcami z PW opracował prototyp systemu monitoringu warstwy ochronnej hybrydowego zbiornika chemoodpornego. Opracowany system umożliwił detekcję uszkodzeń warstwy linera (pęknięć/wżerów) na wczesnym etapie rozwoju, zanim zagrożą one integralności konstrukcji. Wyniki badań opublikowano w międzynarodowym czasopiśmie naukowym Sensors. Publikacja „Structural Health Monitoring of Chemical Storage Tanks with Application of PZT Sensors” jest do pobrania pod poniższym linkiem. Zapraszamy do lektury i kontaktu ze specjalistami Amargo.
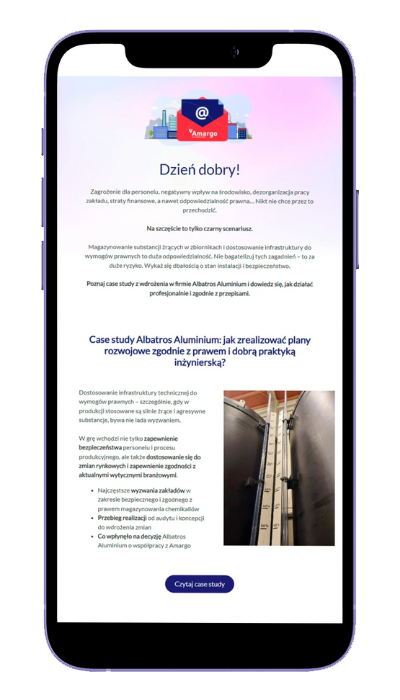
*Administratorem danych jest AMARGO sp. z o.o. sp. k. z siedzibą w Koprkach, ul. Jaśminowa 16, 05-850 Ożarów Mazowiecki, adres e-mail: ado@amargo.pl. Dane podane w powyższym formularzu będę przetwarzane w celu przesłania pliku z poradnikiem firmy Amargo, z uwagi na uzasadniony interes administratora, polegający na odpowiadaniu na kierowane zgłoszenie. Jeżeli wyrażą Państwo chęć, adres e-mail będzie przetwarzany również w celu dostarczenia newsletteru, a więc świadczenia zamówionej usługi. Posiadają Państwo określone prawa wobec przetwarzanych danych osobowych, tj. dostępu, sprostowania, usunięcia, ograniczenia, przenoszenia, wyrażenia sprzeciwu wobec przetwarzania, jak i wniesienia skargi do odpowiedniego organu (Prezes Urzędu Ochrony Danych Osobowych, ul. Stawki 2, 00-193 Warszawa). Podanie danych jest dobrowolne, aczkolwiek konieczne do spełnienia określonego celu. Więcej informacji o przetwarzaniu danych osobowych zawartych jest w Polityce Prywatności.