Projektowanie zbiorników z tworzyw sztucznych w instalacjach przemysłowych przy zastosowaniu Metody Elementów Skończonych (MES)
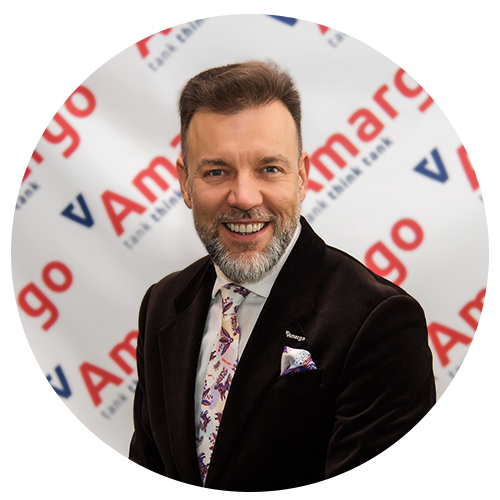
Autor: Szczepan Gorbacz, Prezes Zarządu Amargo
Ekspert z zakresu zbiorników i instalacji z tworzyw sztucznych
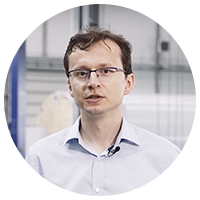
Współautor: Dr inż. Michał Dziendzikowski
Instytut Techniczny Wojsk Lotniczych
Optymalizacja projektowania i przewidywanie reakcji konstrukcji na warunki eksploatacji wymaga uwzględnienia wielu czynników m.in. obciążenia eksploatacyjne, ciśnienie, temperatura, poziom medium, wiatr, opady atmosferyczne, obciążenia wyposażeniem i często ekstremalne warunki pracy. Uznanie znajdują możliwości generowania różnych wariantów bez konieczności wytwarzania prototypów, co wpływa na redukcję kosztów.
Współcześni inżynierowie korzystają z szerokiego wachlarza narzędzi, które pozwalają realizować te cele, umożliwiając tworzenie zoptymalizowanych, trwałych rozwiązań o wysokim poziomie bezpieczeństwa. Jednym z kluczowych podejść wykorzystywanych w procesie projektowania jest Metoda Elementów Skończonych (MES) (ang. finite element method, FEM).
Początków metody elementów skończonych doszukiwać się można w latach 20 i 30 XX wieku, kiedy w USA G. B. Maney i H. Cross oraz A. Ostenfeld w Holandii, korzystając z prac J. C. Maxwella, A. Castiliano i O. Mohra, zaproponowali metodę rozwiązywania zagadnień mechaniki konstrukcji znaną dzisiaj jako metoda przemieszczeń. Uogólnienia tej metody na zagadnienia mechaniki kontinuum dokonali w połowie XX wieku J. Argyris, P. C.Pattan, S. Kelsey, M. Turner, R. Clough i inni. W latach 60 i 70 metoda elementów skończonych przeszła szereg modyfikacji m.in. dzięki pracom O.C.Zienkiewicza, Y.K.Cheunga, R.L.Taylora, które uczyniły z niej współczesne narzędzie służące do rozwiązywania wielu zagadnień m.in. mechaniki ciała stałego, przepływów ciepła, mechaniki płynów, pól elektromagnetycznych [1].
Metoda Elementów Skończonych
MES znajduje szerokie zastosowania w fizyce, a w szczególności w mechanice konstrukcji i mechanice ośrodków ciągłych. Z jej użyciem bada się wytrzymałość konstrukcji, symuluje ich odkształcenia, naprężenia i przemieszczenia, a także przepływ ciepła, przepływ cieczy [2, 3]. Bada się również dynamikę, kinematykę i statykę maszyn, jak również oddziaływania elektrostatyczne, magnetostatyczne i elektromagnetyczne. Metoda stosowana jest również do interpolowania wyników pomiarów wykonywanych na dyskretnym zbiorze punktów np. w meteorologii przy sporządzaniu map synoptycznych.
Aktualne trendy w stosowaniu metody elementów skończonych (MES) skupiają się na kilku kluczowych obszarach. Wśród nich znajduje się przede wszystkim optymalizacja konstrukcji, zwłaszcza w branżach, gdzie produkuje się komponenty w dużych seriach, takich jak przemysł motoryzacyjny czy lotniczy.
Firmy projektujące elementy takie jak bloki silników czy turbosprężarki intensywnie wykorzystują MES, aby zminimalizować wagę i koszty produkcji, jednocześnie spełniając rygorystyczne wymagania wytrzymałościowe. Optymalizacja każdego elementu pozwala zaoszczędzić materiały i zmniejszyć koszty w skali milionów sztuk.
MES znajduje również zastosowanie w analizie złożonych konstrukcji, jak duże zbiorniki czy inne struktury o krytycznym znaczeniu, gdzie tradycyjne metody obliczeniowe mogą być niewystarczające.
W takich przypadkach MES umożliwia precyzyjną analizę miejsc trudno dostępnych lub obarczonych wysokim ryzykiem uszkodzeń, zapewniając bezpieczeństwo i niezawodność konstrukcji.
Metoda elementów skończonych jest zaawansowaną matematyczną metodą obliczeń fizycznych, która polega na zastąpieniu obiektu rzeczywistego (dyskretyzacji obszaru) za pomocą elementów o wymiarach skończonych uśredniających jego stan fizyczny [4].
Oprogramowanie oparte na metodzie elementów skończonych (MES) w formie licencji oferuje wielu dostawców. Wśród najbardziej znanych można wymienić m.in. ANSYS, Inc., Dassault Systèmes (SIMULIA Abaqus), Siemens (Simcenter Nastran), Altair Engineering (HyperWorks, OptiStruct, RADIOSS), Autodesk (Autodesk Nastran, Fusion 360) czy PTC (Creo Simulation Live, Creo Ansys Simulation). Każde z tych oprogramowań różni się funkcjonalnością i specjalizacją. To pozwala użytkownikom dobrać odpowiednie narzędzie w zależności od potrzeb ich branży oraz konkretnego zastosowania.
Jaką rolę odgrywa analiza MES w projektowaniu zbiorników w instalacjach przemysłowych z tworzyw sztucznych?
Zbiorniki to kluczowe elementy infrastruktury przemysłowej wykorzystywane do magazynowania lub przetwarzania substancji w wielu sektorach przemysłu. Najważniejszym wyzwaniem w projektowaniu i eksploatacji zbiorników jest zapewnienie najwyższego poziomu bezpieczeństwa, trwałości i żywotności konstrukcji oraz zgodności z normami, szczególnie gdy przeznaczone są one do pracy z agresywnym substancjami chemicznymi. W procesie doboru zbiornika uwzględniane są specyficzne właściwości materiałów konstrukcyjnych i warunki, w jakich będą one eksploatowane w perspektywie zadanego okresu żywotności (parametry medium, temperatura, ciśnienie, itd.). Ich projektowanie wymaga więc dużej wiedzy i precyzji obliczeniowej.
Naprężenia termiczne a wytrzymałość zbiornika przemysłowego
Naprężenia termiczne w zbiornikach przemysłowych mogą powstawać na skutek zmian temperatury, których pokłosiem mogą być odkształcenia materiału konstrukcyjnego. Zbiorniki o czarnej barwie są szczególnie narażone na nagrzewanie, ponieważ silniej absorbują promieniowanie słoneczne. W wyniku tego, ich powierzchnia może nagrzewać się nierównomiernie.
Na przykład podczas wschodu słońca jedna strona zbiornika zostaje intensywnie ogrzana, co prowadzi do zmiany temperatury i zjawiska rozszerzalności cieplnej. Nierównomierne ogrzewanie powoduje powstanie niejednorodnego pola temperatur, co na skutek rozszerzalności cieplnej generuje w strukturze naprężenia cieplne. Ten efekt jest szczególnie zauważalny w przypadku materiałów polimerowych, dla których współczynnik rozszerzalności cieplnej jest znacznie większy niż dla metali.
W sytuacjach, gdy zbiornik podlega dużym wahaniom temperatury, różne jego części mogą rozszerzać się lub kurczyć z różną intensywnością, co przyczynia się do powstawania naprężeń wewnątrzmateriałowych.
Długotrwałe oddziaływanie takich naprężeń może prowadzić do zmęczenia materiału, mikropęknięć, a nawet uszkodzeń strukturalnych. Wszystko to znacznie obniża wytrzymałość zbiornika. Aby temu zapobiec, przy projektowaniu zbiorników dobiera się specjalistyczne tworzywa o wysokiej odporności na zmiany temperatury oraz odpowiedni rodzaj izolacji termicznej po stronie zewnętrznej płaszcza zbiornika.
Analiza MES może znacząco pomóc w ocenie wpływu naprężeń termicznych na wytrzymałość zbiornika przemysłowego, zapewniając precyzyjne informacje i symulacje.
Dokładna analiza rozkładu temperatury pomaga zweryfikować, jak różne części zbiornika reagują na zmienne warunki temperaturowe:
- warunki tzw. cold day zakładające np. temperaturę medium równą 40°C, a temperaturę zewnętrzną -20°C,
- oraz warunki tzw. hot day zakładające np. temperaturę medium równą 40°C i temperaturę zewnętrzną 40°C).
Analizy wykonuje się dla warunków:
- short term (np. 24 godziny)
- oraz long term (perspektywa np. 10 lat).
W wyniku obliczeń możemy dowiedzieć się:
- czy zbiornik spełnia wszystkie założenia konstrukcyjne w perspektywie short term i long term, a jeśli nie to jakie zmiany konstrukcyjne pozwolą ograniczyć powstawanie negatywnych zjawisk (np. pełzania).
- jak izolacja zewnętrzna wpływa na gradient temperaturowy pomiędzy ścianą zewnętrzną a wewnętrzną konstrukcji zbiornika, zwłaszcza dla ścianek o budowie strukturalnej w przekroju, czyli niejednorodnej w każdym punkcie, jak w przypadku technologii AmargTank MultiLayer DoubleWall® [5, 6, 7],
- jak zmienia się temperatura ściany zewnętrznej wraz z wysokością zbiornika,
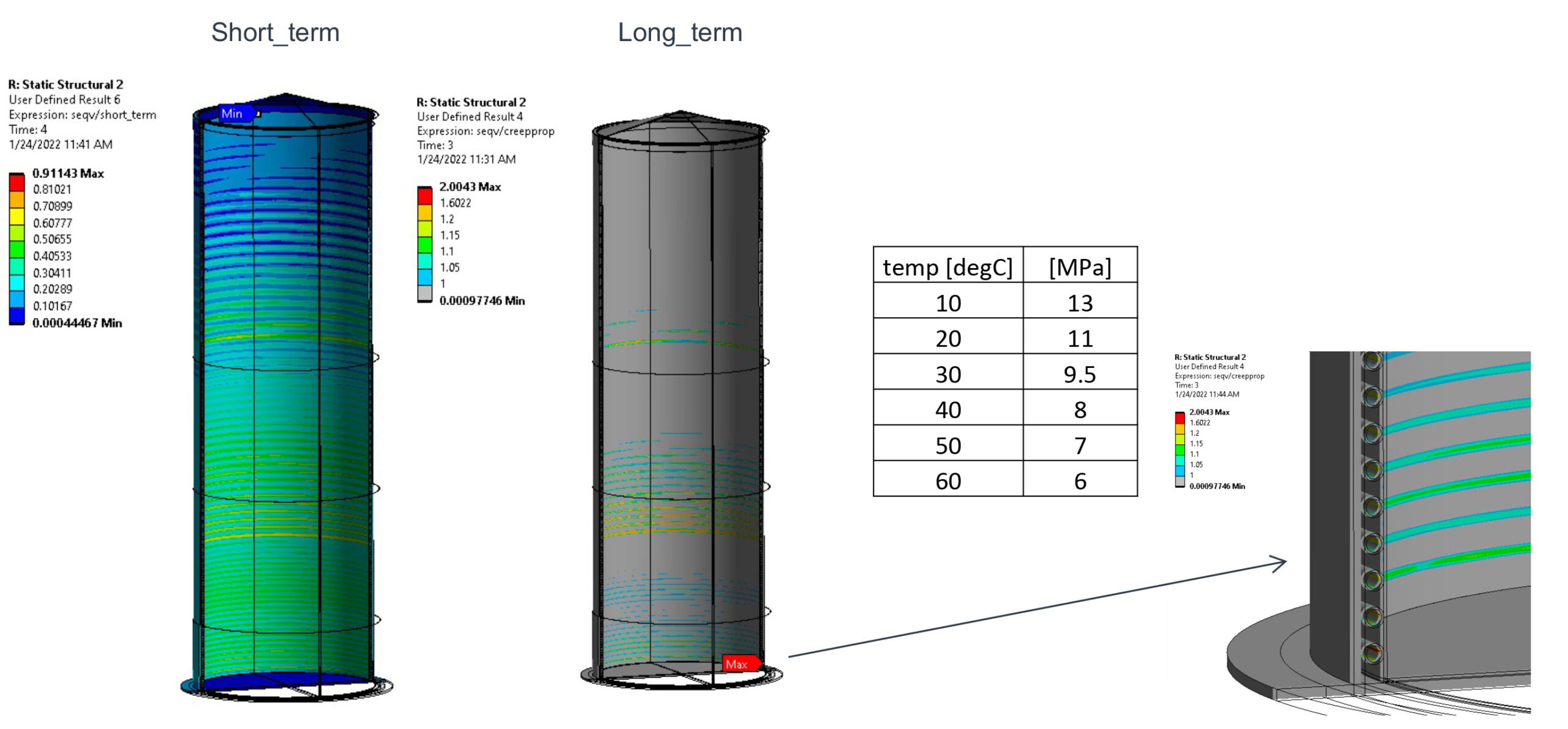
Rys. 1. Przykład wyników badań statyki konstrukcji zbiornika ze środkowym profilem rurowym w warunkach cold day i perspektywach short term i long term [źródło: materiały własne Amargo®]
Zjawisko pełzania niskotemperaturowego polietylenu (PE) a analizy wytrzymałościowe
Pełzanie to zjawisko powolnej, trwałej deformacji materiału pod wpływem stałego obciążenia, które występuje w temperaturach niższych od temperatury topnienia. W przypadku polimerów zjawisko to jest zazwyczaj kojarzone z wyższymi temperaturami. W przypadku natomiast polietylenu PE, który jest (poza propylenem PP) jednym z najczęstszych materiałów konstrukcyjnych zbiorników, może ono wystąpić również w niższych temperaturach, uznawanych za bezpieczne dla tworzyw termoplastycznych. Jest to szczególnie istotne przy długotrwałym obciążeniu, np. w rurociągach lub zbiornikach.
W niskich temperaturach pełzanie PE przebiega wolniej niż w wysokich, jednak nadal może prowadzić do stopniowej deformacji materiału. Proces ten jest uzależniony od kilku czynników, takich jak rodzaj PE (PE-HD, PE-LD), poziom naprężeń, czas trwania obciążenia, a także otoczenie i warunki pracy, w których materiał pracuje.
Zjawisko pełzania niskotemperaturowego jest istotnym czynnikiem w ocenie trwałości elementów wykonanych z polietylenu i musi być brane pod uwagę przy długotrwałej eksploatacji. Z tego względu powinno być ono uwzględniane w toku obliczeń wytrzymałościowych i analizy MES.
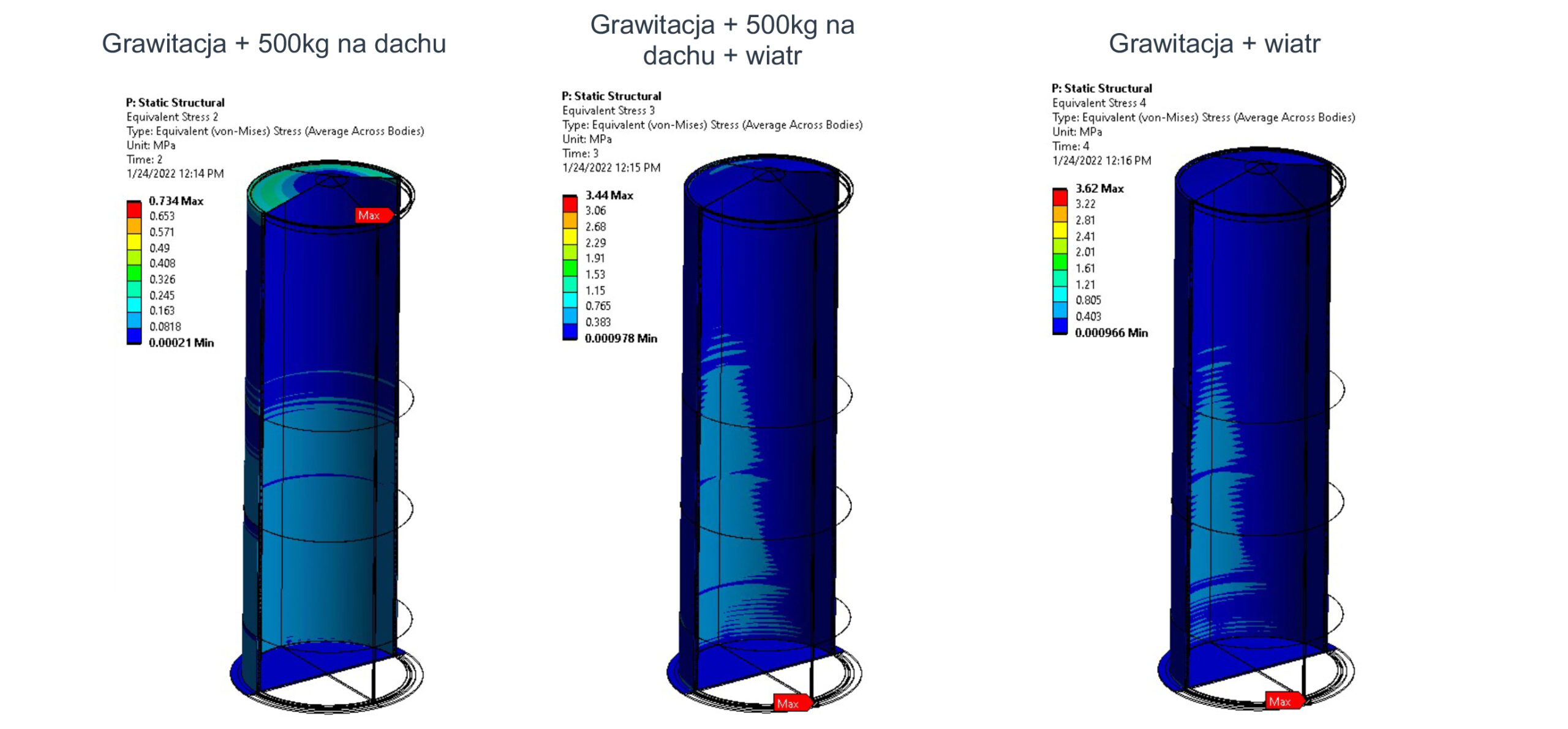
Rys. 2. Przykład wyników badania wpływu poszczególnych obciążeń mechanicznych na stateczność konstrukcji zbiornika ze środkowym profilem rurowym [źródło: materiały własne Amargo®]
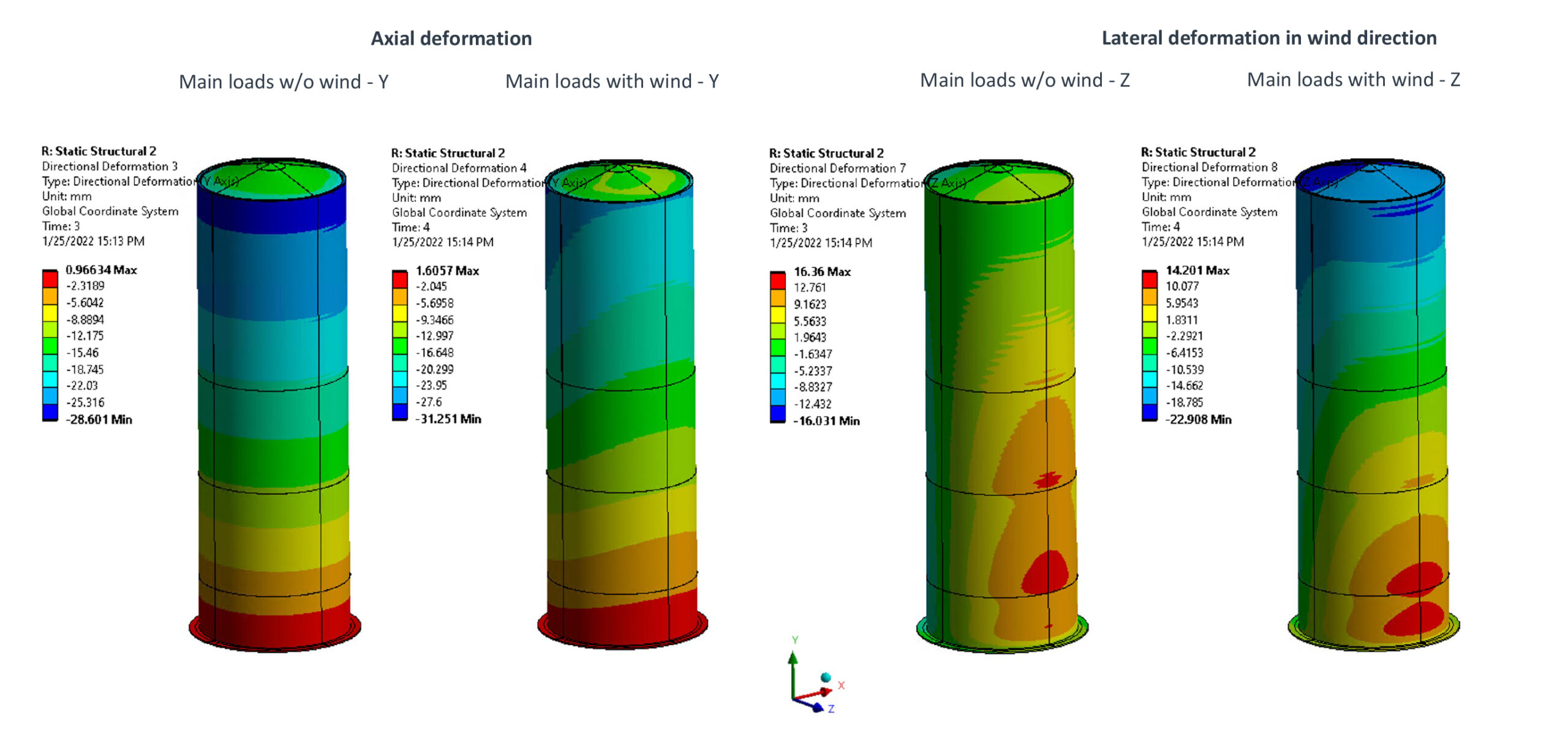
Rys. 3. Przykład wyników badania odkształcenia zbiornika dla różnych kombinacji obciążeń do cold day [źródło: materiały własne Amargo®]
Cykliczność pracy zbiornika a jego żywotność
Istotny wpływ na żywotność konstrukcji zbiornika ma cykliczność jego pracy, czyli powtarzalność zmian temperatury czy ciśnienia w trakcie eksploatacji. Każdy cykl obciążeń wpływa na powstawanie odkształceń materiału. Te z kolei mogą prowadzić do zmęczenia strukturalnego, czyli osłabienia wytrzymałości zbiornika.
Powtarzające się cykle obciążeń mogą powodować powstawanie mikropęknięć. W dłuższym okresie mogą się one rozwijać, skutkując poważniejszymi uszkodzeniami, takimi jak pęknięcia zmęczeniowe. Zjawisko to jest szczególnie groźne, gdy zbiornik wykonany jest z materiału o niskiej odporności na zmęczenie. Zagrożeniem jest brak odpowiedniego monitorowania zbiornika, które umożliwiłoby wykazanie przekroczenia dopuszczalnych poziomów minimalnych.
Analiza MES jest pomocna w symulacji zachowania materiału pod wpływem powtarzających się cykli obciążeniowych. Dzięki temu możliwe jest dokładniejsze przewidywanie żywotności zbiornika i identyfikacja potencjalnych miejsc uszkodzenia.
Wydłużenie żywotności zbiornika w warunkach cyklicznej pracy jest możliwe dzięki optymalnemu projektowaniu, uwzględniającemu cykle obciążeniowe oraz stosowaniu materiałów o wysokiej odporności na zmęczenie.
W przypadku zbiorników przemysłowych, szczególnie przeznaczonych do magazynowania substancji żrących, trujących lub ciekłych zapalnych, kluczową rolę w monitorowaniu stanu technicznego odgrywają regularne inspekcje i badania, umożliwiające wczesne wykrycie wszelkich nieprawidłowości. Identyfikacja pęknięć, defektów i innych uszkodzeń, zanim doprowadzą one do poważniejszych problemów, pozwala na podejmowanie odpowiednich działań konserwacyjnych, napraw lub wymiany wadliwych elementów, co znacząco zmniejsza ryzyko awarii i wydłuża żywotność zbiornika. Zapobieganie takim usterkom ma kluczowe znaczenie dla bezpieczeństwa personelu i mienia zakładu, środowiska oraz efektywnej eksploatacji. Ważne są również procedury kontrolne, jak analiza naprężeń i regularne badania nieniszczące, aby wcześnie wykryć potencjalne uszkodzenia.
Odpowiednie „zarządzanie” naprężeniami termicznymi jest kluczowe dla zachowania wymaganej żywotności i bezpiecznej eksploatacji zbiorników w zmiennych warunkach pracy.
Monitorowanie stanu konstrukcji i pracy zbiorników przemysłowych z tworzyw sztucznych umożliwi system TankSense360® [5-7], do projektowania którego wykorzystane są Metody Elementów Skończonych (MES) / FEM – Finite Elements Method. System jest w trakcie prac badawczo-rozwojowych realizowanych przez zespół Amargo® wraz ze specjalistami z Wydziału Inżynierii Materiałowej Politechniki Warszawskiej oraz ekspertami z zakresu badań materiałowych. Idea systemu TankSense360® została przedstawiona w numerze 1/2024 Biuletynu Urzędu Dozoru Technicznego „INSPEKTOR” [8].
Wydłużenie żywotności zbiornika w warunkach cyklicznej pracy jest możliwe dzięki optymalnemu projektowaniu, uwzględniającemu cykle obciążeniowe oraz stosowaniu materiałów o wysokiej odporności na zmęczenie.
Informacje z modelowania MES w systemach monitorowania zbiorników
Modelowanie MES przy projektowaniu konstrukcji stanowi istotny element cyfrowej transformacji w ramach przemysłu 4.0. Dzięki wiarygodnym danym materiałowym oraz powtarzalności procesów technologicznych możliwe jest bardzo dokładne przewidywanie zachowania konstrukcji pod wpływem działających na nią obciążeń w trakcie eksploatacji. Pozwala to już na etapie projektowania przewidzieć szereg zjawisk, które mogą wystąpić, uwzględniając czynniki wpływające na obciążenia w konkretnym przypadku, a także zoptymalizować konstrukcję przy zachowaniu najwyższego poziomu bezpieczeństwa.
Model MES zbiornika wraz z warunkami brzegowymi dla rozkładu obciążeń może stanowić istotny element jego tzw. cyfrowego bliźniaka lub cyfrowego paszportu, w którym gromadzone są wszelkie informacje eksploatacyjne z całego cyklu życia produktu, w tym dane o uszkodzeniach.
W przypadku wyposażenia zbiorników w inteligentne sieci czujników monitorujących informacje o stanie i odkształceniach konstrukcji, modele MES mogą umożliwić wykorzystanie tych danych do oceny stopnia zużycia zapasu bezpieczeństwa konstrukcji oraz prognozowania okresu bezpiecznej eksploatacji poszczególnych egzemplarzy zbiorników.
Możliwe będzie przejście od systemu eksploatacji opartego na ściśle określonym okresie trwałości do eksploatacji według stanu technicznego, co pozwoli na bardziej efektywne wykorzystanie zasobów oraz zwiększenie poziomu bezpieczeństwa.
Praktyczne korzyści MES w projektowaniu zbiorników przemysłowych
Zastosowanie Metody Elementów Skończonych w projektowaniu zbiorników przemysłowych z tworzyw sztucznych umożliwia precyzyjną ocenę bezpieczeństwa konstrukcji. Pozwala na przewidywanie miejsc potencjalnych awarii oraz identyfikację słabych punktów konstrukcji. Wśród takich wymienić można obszary narażone na nadmierne naprężenia czy zmęczenie materiału np. spoiny, połączenia dna z cylindrem czy ściany wielowarstwowe. Dzięki temu można skutecznie zapobiegać uszkodzeniom, zwiększając bezpieczeństwo zbiorników na przykład poprzez zwiększenie grubości ścianek, dodanie wzmocnień czy zmianę materiału.
MES pozwala na optymalizację konstrukcji. Dzięki symulacjom można minimalizować ilość materiału bez kompromisów na wytrzymałości. To z kolei wpływa na obniżenie kosztów produkcji, co jest istotne z ekonomicznego punktu widzenia.
Analiza różnych warunków pracy zbiornika, takich jak zmienna temperatura, ciśnienie czy obciążenia dynamiczne, czy też symulacje uwzględniające warunki cykliczne, pozwalają na dostosowanie projektu do rzeczywistych warunków eksploatacyjnych.
Istotną kwestią jest możliwość redukcji kosztów związanych z przeprowadzaniem testów na konstrukcjach rzeczywistych. Dzięki symulacjom komputerowym projektanci mogą zweryfikować różne warianty konstrukcji w środowisku wirtualnym, co znacznie przyspiesza proces projektowania i pozwala ograniczyć liczbę kosztownych prototypów.
Zrównoważone projektowanie oraz użytkowanie zbiorników przemysłowych wymaga synergii zaawansowanych technologii projektowania, doboru odpowiednich materiałów oraz nowoczesnych rozwiązań. Mogą one wspierać użytkowników w monitorowaniu stanu konstrukcji w czasie rzeczywistym. Dzięki takim działaniom możliwe jest wydłużenie żywotności zbiorników, zwiększenie ich bezpieczeństwa oraz zmniejszenie kosztów związanych z konserwacją i naprawami.
KONSULTACJA MERYTORYCZNA:
MGR INŻ. LESZEK LEWANDOWSKI
Ekspert niezależny ds. Tworzyw Sztucznych
Pracownik Urzędu Dozoru Technicznego w latach 1984–2023 UDT Oddział w Bydgoszczy
Literatura:
- Jerzy Podgórski, Ewa Błazik-Borowa: „Wprowadzenie do Metody Elementów Skończonych w Statyce Konstrukcji”, IZT, Lublin 2001.
- O. Zienkiewicz, C. Taylor, R. Leroy, The finite element method. Vol. 1, Basic formulation and linear problems, McGraw-Hill Publishing Company.
- O. Zienkiewicz, C. Taylor, R. Leroy, The finite element method. Vol. 2, Solid and fluid mechanics dynamics and non-lineary, McGraw-Hill Publishing Company.
- Osiński J.: Obliczenia wytrzymałościowe elementów maszyn z zastosowaniem metody elementów skończonych. Oficyna Wydawnicza Politechniki Warszawskiej, Warszawa, 1997.
- https://www.amargo.pl/wp-content/uploads/2021/08/technologia-amargtank-safeseamless-metoda-nawojowa-produkcja-zbiornikow-rurowych.pdf [dostęp: 11.2024].
- https://www.amargo.pl/wp-content/uploads/2022/11/Specyfikacja-zbiornikow-chemoodornych_technologia-nawojowa.pdf [dostęp: 11.2024].
- https://www.amargo.pl/akademia-taed/strefa-projektanta/ [dostęp: 11.2024].
- S. Gorbacz, A. Boczkowska, P. Kozera, M. Dziendzikowski, „Inteligentny zbiornik chemoodporny. Trend czy realna potrzeba?”, 1/2024 magazyn Urzędu Dozoru Technicznego „INSPEKTOR” https://www.udt.gov.pl/images/INSPEKTOR_1_2024_WCAG.pdf [dostęp: 11.2024]
Materiał został opracowany i opublikowany w 3-4/2024 numerze magazynu Urzędu Dozoru Technicznego „INSPEKTOR”.
Kliknij tutaj, by pobrać artykuł w formacie .pdf
Porozmawiajmy o rozwiązaniu Twojego wyzwania
Rozmowa to klucz do sukcesu. Skorzystaj z naszej wiedzy i doświadczenia.